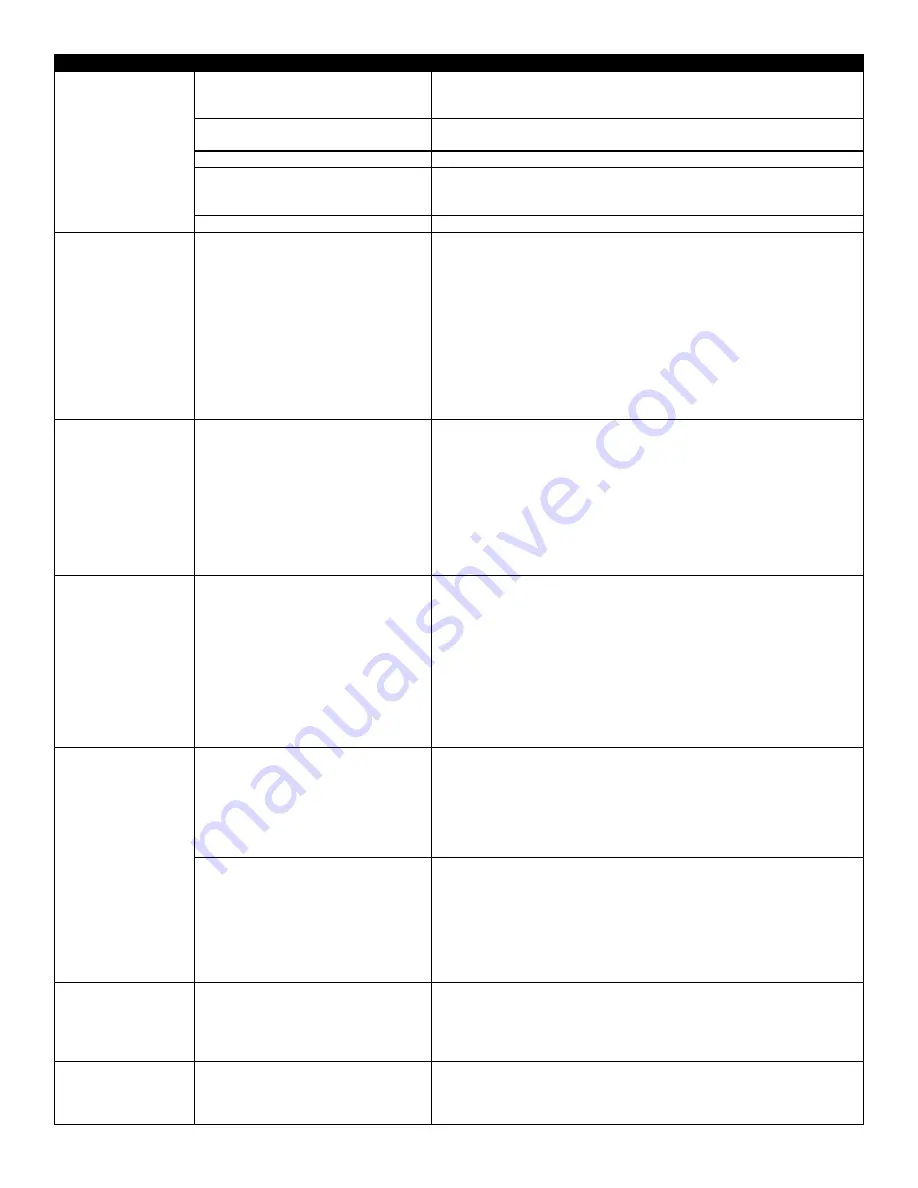
66
COMPONENT
FAILURE MODE
ANALYSIS
Noisy Operation
• Supply Gas Issue
• Refer to Part 3 Gas Connection in this manual.
• Natural Gas Pressure reads between 4” w.c. and 14” w.c.
• L.P. Gas Pressure should be at 11” w.c.
• Air/Gas Mixture Issue
• Refer to Section 8.3 Gas Valve Adjustment Procedure for proper
combustion setting.
• Air Inlet and/or Vent configuration
• Refer to Part 2 Venting and Air Supply
• Dirty/ Damaged Burner
• Refer to Burner Maintenance in section 10.5 of this manual for the
burner removal and inspection procedure. Clean or replace the
burner, if required.
• Air in the piping system
• Purge all air from the piping system
Auto Reset High
Limit Trips
• The outlet temperature has
exceeded the set point
temperature specified.
• Alert: 67, 79, 137, 303-310
• ILK OFF
• Verify that the system is full of water and that all air has been
properly purged from the system.
• Verify that ∆T does not exceed 60°F across the heat exchanger
• Verify that the boiler is piped properly.
• Verify that 120 VAC is being supplied to the boiler pump on a call
for heat. If voltage cannot be detected check wiring.
• Verify that the pump is circulating when 120VAC is detected. If not,
pump impeller may be stuck.
• If 120 VAC is present during a call for heat, but the pump still does
not circulate, replace the pump.
• Check outlet sensor for proper functionality. At 77
o
F (25
o
C) the
sensor will show 10kΩ of resistance.
Manual Reset High
Limit Trips (if
equipped)
• Manual Reset Safety High Limit
tripped, outlet temperature in
excess of 210
o
F
• Alert: 67, 79, 137, 303-309
• ILK OFF
• Verify that the system is full of water and that all air has been
properly purged from the system.
• Verify that the boiler is piped properly.
• Verify that 120 VAC is being supplied to the boiler pump on a call
for heat. If voltage cannot be detected check wiring.
• Verify that the pump is circulating when 120 VAC is supplied. If so,
pump impeller may be stuck. Use a flat head screwdriver on face of
pump to turn impeller manually.
• If 120 VAC is present during a call for heat, but the pump still does
not circulate, replace pump.
Delta-T Limit
Tripped
• Inlet and Outlet temperature has
exceeded 70
o
F
• Alert: 124
• Verify that the system is full of water and that all air has been
properly purged from the system.
• Verify that the boiler is piped properly.
• Verify that 120VAC is being supplied to the boiler pump on a call
for heat. If voltage cannot be detected check wiring.
• Verify that the pump is circulating when 120VAC is detected. If not,
pump impeller may be stuck.
• If 120VAC is present during a call for heat, but the pump still does
not circulate, replace the pump.
• Purge all air from the piping
• Verify boiler water pressure exceeds 30 PSI
Temperature
Overshoot
• Stack temperature has exceeded
the limit temperature.
• Alert: 125
• The stack temperature has exceeded the maximum temperature
allowed.
• CPVC: 194
o
F
• PPE: 230
o
F
• AL29-4C, Stainless Steel: 300
o
F+
• Measure the resistance of the flue sensor at room temperature, it
should be approximately 10kΩ.
• Outlet temperature has exceeded
target temperature.
• Alert: 67, 79, 137, 303-309
• ILK OFF
• Check outlet sensor. It should be firmly inserted in well
• Water flow may be too low and allows burner to run longer than
required creating a reservoir of hot water in the center of the heat
exchanger. Check Central Heat and/or DHW PID parameters
P=60, I = 20, D=0 provides quickest response.
• Lower target to modulate burner off sooner
• If modulating pump is supplied, increase the pump speed to
prevent outlet temperature overshoot.
Sensor Not
Connected
• Inlet sensor, Alert: 91
• Outlet sensor, Alert: 92
• DHW sensor, Alert: 93
• Flue sensor, Alert: 95
• Outdoor sensor, Alert: 96
• Verify sensors are connected
• Verify wiring.
• Measure resistance of sensors at room temperature, 10kΩ
sensors.
• Replace sensor if necessary
Fan Not Turning
• Fan refuses to rotate
• Alert 122, 123, 128, 129, 130, 131,
132
• Check fan power wires
• Fan signal wires are interchanged
• Minimum fan speed must be greater than 800 RPM
Summary of Contents for ADVANTUS AVH 500
Page 2: ......
Page 3: ......
Page 38: ...31 Figure 23 Recommended Piping with Reverse Return and Variable Primary Flow...
Page 88: ...81 PART 12 EXPLODED VIEW Figure A...
Page 89: ...82 Figure B FAN BURNER ASSEMBLY AV500 600 some items may not be as shown...
Page 90: ...83 Figure C FAN BURNER ASSEMBLY AV800 4000 some items may not be as shown...
Page 91: ...84 Figure D Figure E...
Page 92: ...85 Figure F Figure G...
Page 93: ...86 Figure H CONTROL BOARD ASSEMBLY...
Page 100: ...93 PART 13 ELECTRICAL DIAGRAMS...
Page 101: ...94...
Page 102: ...95...