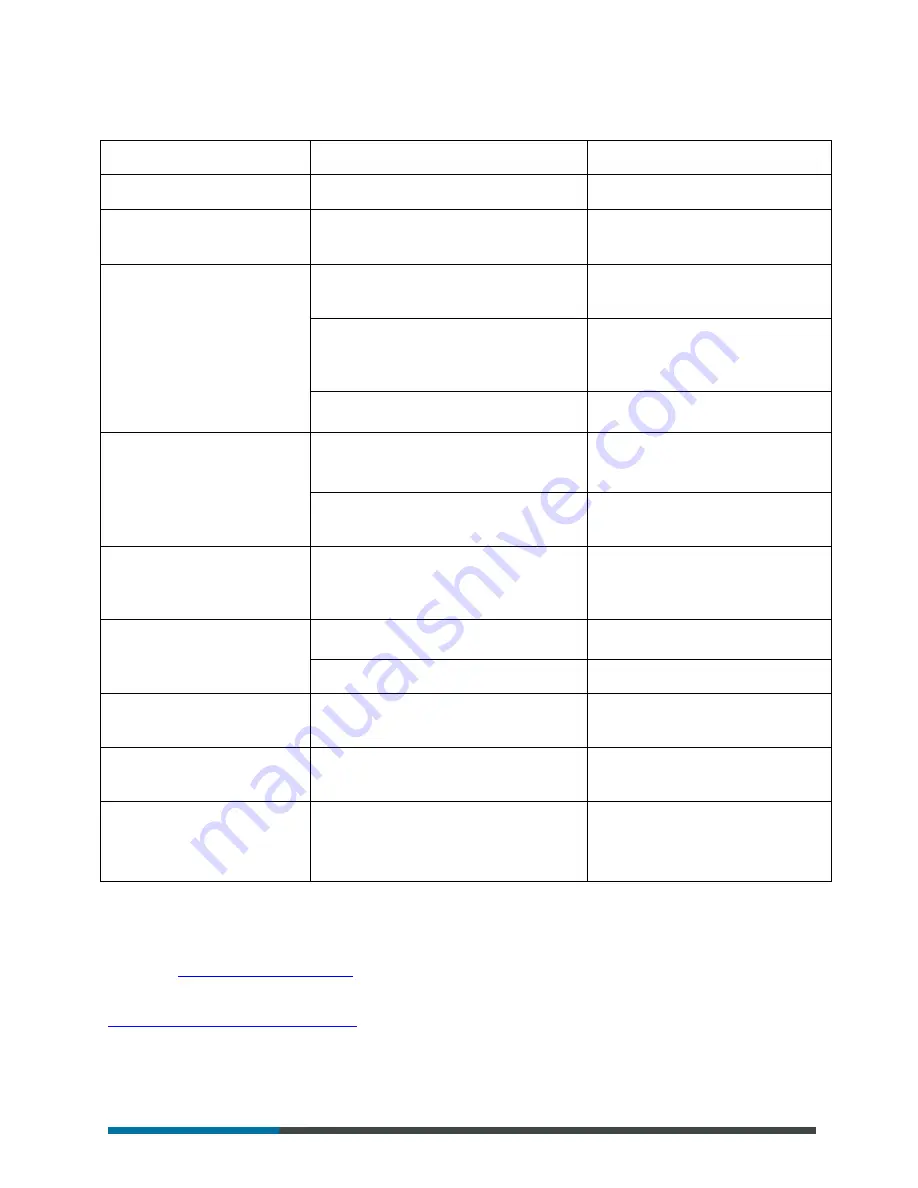
CPB-515 Operation and Maintenance Manual
– TTS 45, 70, 80,100, 110 Series (10-2017)
23
7.0 TROUBLESHOOTING
Problem
Possible cause
Solution
Uneven tread wear
High amount of roading
Swap tracks side to side
Splits/opening on the
side or top of tread
High amount of roading or
overheat of tread
Swap tracks side to side,
replace tracks if necessary
Chunking on guide
lug sides
Track not aligned properly
Align track, see “Track
Alignment Adjustment”
section
Improper break-in of track
Operate in dry dusty
conditions, see “Track
Break-
in” section.
Side slope operation
Contact Dealer
Breakaway of track
guide lugs
Material or workmanship defect
(clean separation)
Contact Dealer
Debris/material ingestion into
track system. (jagged
separation)
Clean material off of drive
wheel
Correct tensioning not
possible
Verify position of track
detensioning bolt at rear idler
assembly
Bolt fully retracted with no
preload on spring applied
High temperature of
idler or roller axle hub
Bearing failure
Replace damaged bearing
Lack of lubricant
Check oil level in reservoir
service
Noise from idler or
roller axle hub
Bearing failure
Replace damaged bearing
Mud/dirt build up on
idlers/midrollers
Operation in muddy, wet, or
sticky soil types
Clean mud/dirt regularly to
prevent track damage.
System dog tracking
or problems with track
alignment
Alignment adjustment incorrect.
Undercarriages parallelism is
out of tolerance
Adjust alignment per
procedures. Otherwise,
contact your Dealer
8.0 ADDITIONAL INFORMATION
Additional information on Camso track systems, tracks, and our other products may be
found at
For any questions or corrections regarding this manual, please email us at
. You can also contact our Customer Service Desk @
317-671-7327 or 1-844-226-7624.
Please include the manual publication number and edition as found in the footer