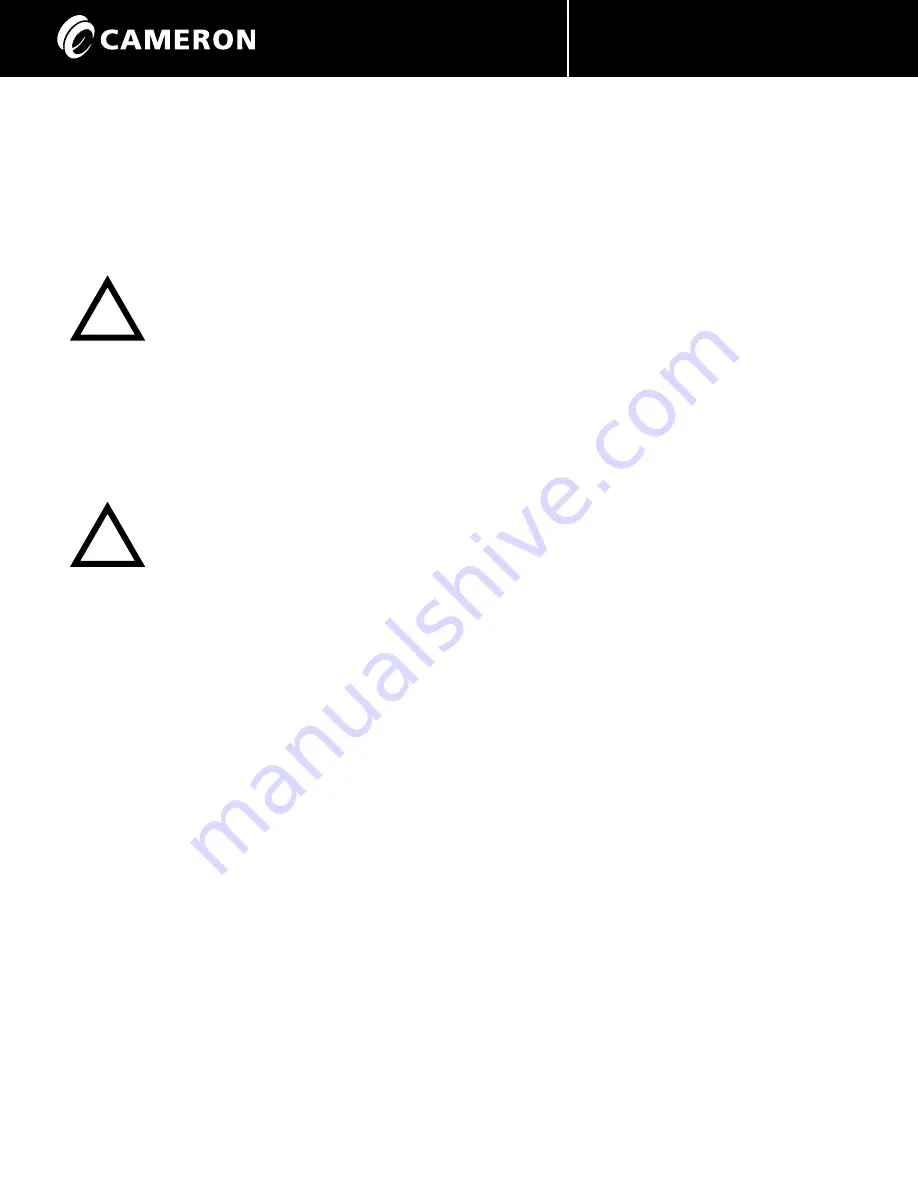
D I S T R I B U T E D V A L V E S
6
03/2011 / IOM-NAV-BALL-S30
Installation, Operation and Maintenance Manual
!
CAUTION
5.
Avoid rapid application of excess welding material. Weld each end of the valve with a continuous bead
using a 1/8 in. maximum diameter electric welding rod.
6.
Thoroughly clean (by pigging and/or flushing) weld slag from valve bore and line before turning ball
to closed position.
Proper installation into the line should be done in accordance with the following procedure:
Caution: Ensure that all test fluids contain corrosion inhibitors and are compatible with valve
seat and seal material.
1.
Preliminary Testing. Completely flush the system or the line to minimize damage to the seats and ball
surface which might be caused by weld slag or other foreign matter resulting from
installation procedures.
2.
Line Testing. When performing this test, the valve should be in the half-open position to ensure that
the body cavity is completely filled with the test media and to prevent accidental over pressure
of the seats.
Caution: Line may be tested at a maximum of 1 ½ times the valve’s cold working pressure
rating without consulting the factory.
3.
Seat Testing. When testing the seats with the valve in the closed position, do not exceed the valve’s cold
working pressure rating.
4.
Upon completion of testing, purge all test fluids from the valve and return to the required operating
position, either fully open or fully closed.
Operation
NAVCO S30 ball valves operate from fully open to fully close by a 90 degree turn of the handle. The handle
aligned with the pipe always means the valve is open and with the handle perpendicular to the pipe means the
valve is closed.
Additionally, the stems have flats that align the handle and can be used to indicate ball position. The bore of
the ball is parallel with the faces of the stem flats.
NAVCO S30 valves may be power actuated. See the S30 flyer for ISO 5211 mounting configuration.
Pneumatic and hydraulic actuators, whether of the fail-open, fail-close, or fail-last position type, have OPEN
or CLOSED indicators on the top of each unit. On pneumatic actuators, make sure filters and lubricators (if
recommended by the actuator manufacturer) are installed prior to valve and actuator installation. Should any
maintenance be necessary, obtain the part number from the unit’s nameplate and contact the nearest Cameron
representative.
!
CAUTION