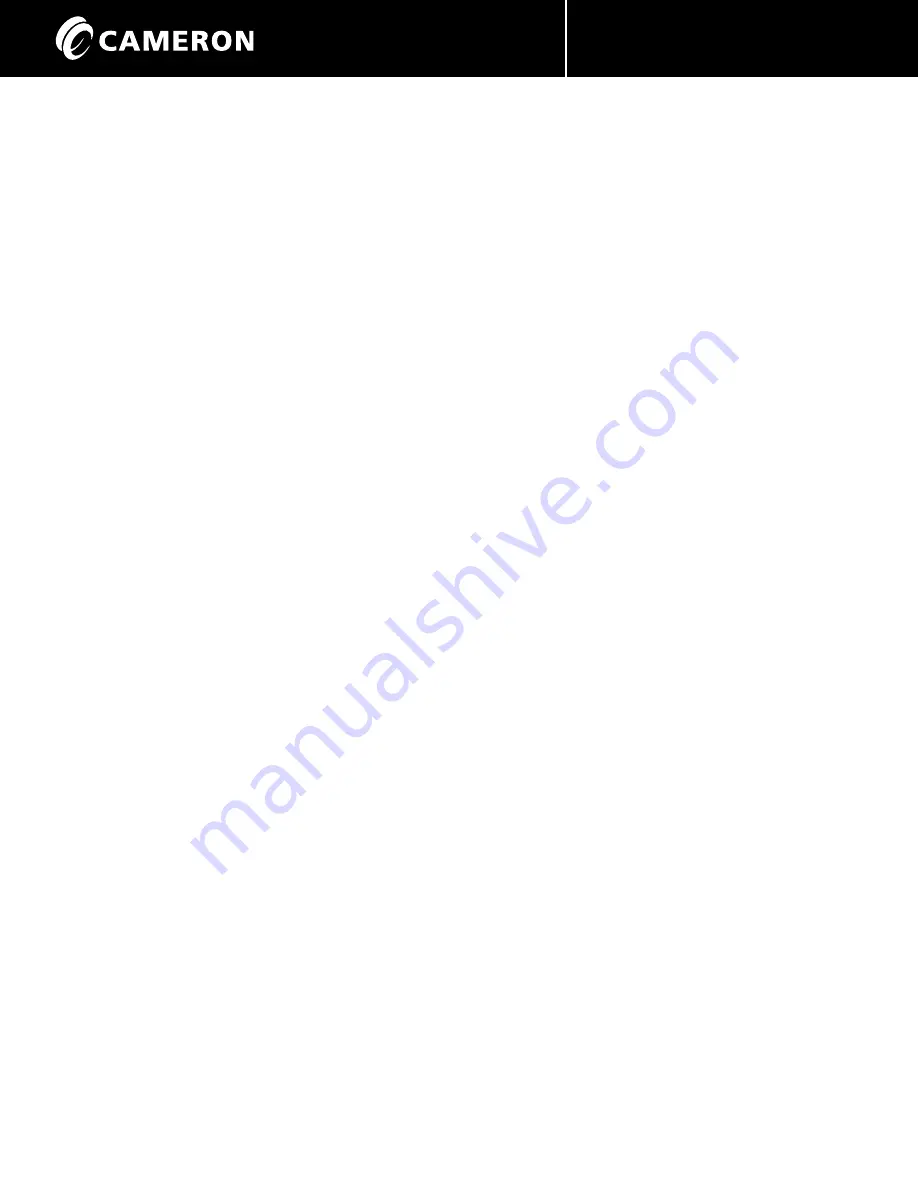
E N G I N E E R E D & P R O C E S S V A L V E S
07/2011 / IOM-GEN-TWIN-03
25
Installation, Operation and Maintenance Manual
OPERATOR ASSEMBLY
1.
Install the two bearings (28) at the top end of the upper stem (5).
NOTE: These are radial thrust bearings and must be installed such that the widest surfaces of the inner race ways are back to back.
INCORRECT INSTALLATION WILL RESULT IN SERIOUS DAMAGE.
2.
Apply a smooth even coating of Permatex Number 3D to the bottom flange of the upper housing (2) and fasten to the lower
housing (1) with studs (32) and nuts (40). The dowel pin (43) is a press fit in the lower housing and a slip fit in the upper housing.
Its function is to properly align the roller grooves.
3.
Apply a liberal coating of grease to all surfaces of upper stem (5) and lower stem (4).
4.
Thread the two stems together such that the drive pin (14) in the upper stem comes against the shoulder at the top of the lower
stem and the detent recess in the upper stem is exactly in line with the roller opening in the lower stem. This operation may
require several attempts as the threads are multiple start and do not always assemble correctly with the first try.
5.
Install the indicator shaft sub-assembly up through both stems and secure with the roll pin (44) in the bottom of the lower stem.
6.
Install O-Ring (23) in the lower housing (1).
7.
Place the roller (21) in the side opening of the lower stem (4). A liberal application of grease will hold it in place.
8.
Place the stems with bearings and roller assembled down through the top of the upper housing until the lower of the two
bearings (28) rests on the shoulder in the upper housing.
9.
Apply a smooth even coating of Form-a-Gasket
®
to the surface of the guide pin boss on the lower housing (1).
10. Insert the guide pin (16) to fully engage the slot in the lower stem and fasten with cap screws (33).
11. Place the gear key (20) in the keyway of the upper stem (5).
12. Place the tapered roller bearing cones (29) on each end of the worm shaft (7) with the large diameter of the cone taper against
each shaft shoulder.
13. Assemble the cups (30) on the cones (29).
14. Apply a smooth even coating of Form-a-Gasket
®
to the surfaces of the bearing retainer bosses on the gear housing (3).
15. Fasten the blind bearing cap (9) in place with capscrews (36).
16. Install the worm shaft (7) in the gear housing.
17. Install the O-Ring (22) in the bearing cap (10) and fasten in place with capscrews (36). Be sure to re-install the plastic shims
between the gear housing and the bearing cap.
18. Install worm gear (6) in gear housing with hub down. (Toward smallest opening).
19. Apply a smooth coating of Form-a-Gasket
®
to top flange of upper housing.
20. Place the gear housing with assembled parts on top of the upper housing guiding the worm gear keyway over the key (20) in the
upper stem, and fasten to the upper housing with capscrews (38).
21. Install ball bearing (27) over upper stem and secure with nut (17).
22. Fill the gear housing with grease up to the top of the worm gear.
23. Apply a smooth even coating of Form-a-Gasket
®
around top surface of gear housing.
24. Install the grease seal (26) in the gear housing cover (8). Slide the cover over the indicator shaft (12) and the ball bearing (27) and
secure to the top of the operator housing with capscrews (35).
25. Install the stem protector (24) and secure the indicator flag (11) in place with set screw (39).
26. Install the handwheel (13) with key (19), washer (18), capscrew (34) and spinner handle (31).
GENERAL VALVE
®
Twin Seal
™
Model 1276G