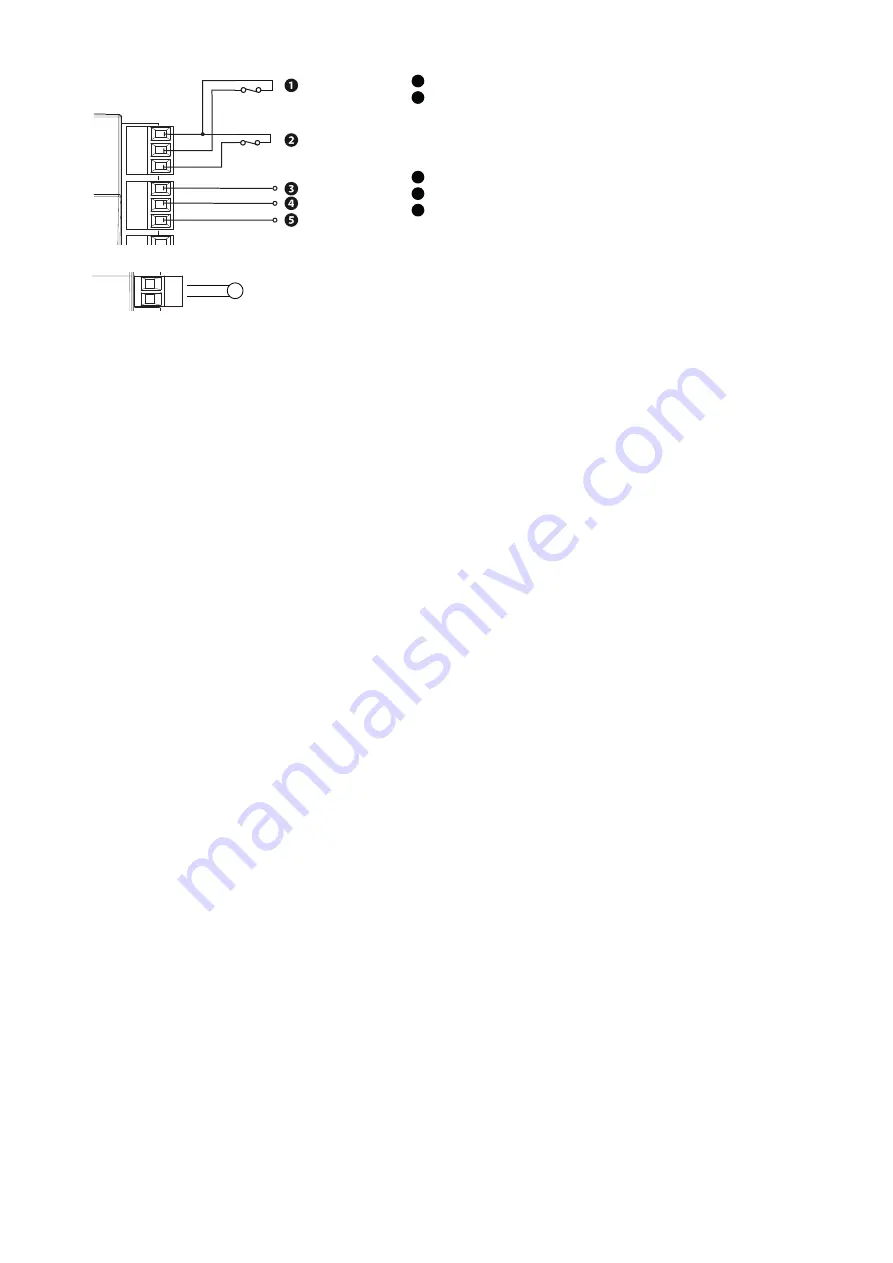
Page
19
- Manual
FA01947-EN
- 03/2023 - © C
AME S.p.A. - The contents of this manual may be changed at any time and without notice. - T
ranslation of the o
riginal instructions
Connecting the gearmotor with encoder and limit switches
C
X
+ E -
FC F
A
F
1
Opening limit-switch (NC contact)
2
Closing limit-switch (NC contact)
Encoder
3
Green cable
4
Brown cable
5
White cable
M N
M
24 V DC gearmotor