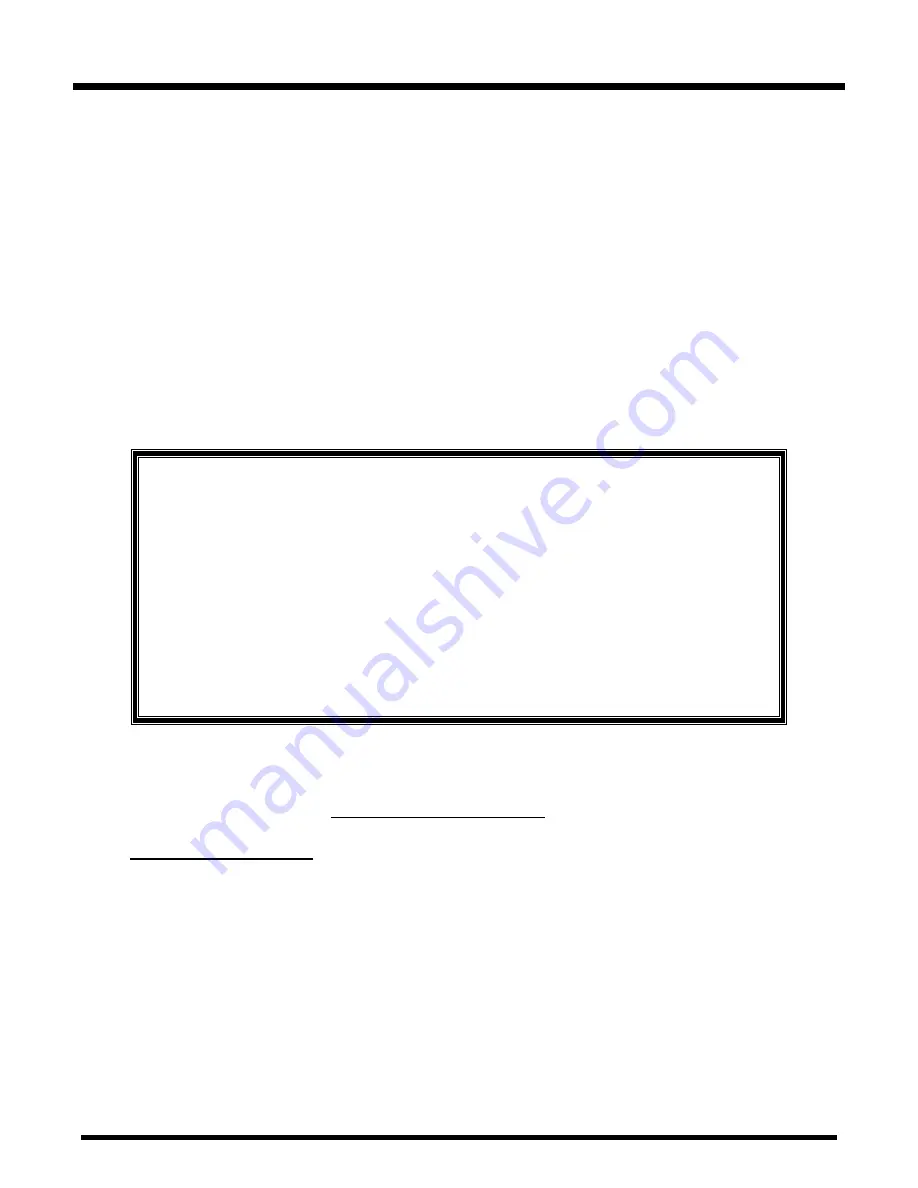
ITH-Series Technical Manual
Page 25
Cambridge
Engineering
Inc.
Venting / Combustion Air Ducting
General Requirements
Refer to the
National Fuel Gas Code,
ANSI Z223.1 (NFPA 54), as well as all local requirements
for general venting guidance.
Series ITH Infrared Heaters may be installed vented or unvented.
Series ITH Infrared Heaters may be vented horizontally or vertically using conventional venting
materials.
If heater is to be vented horizontally, the vent from building must:
o
Be not less than seven feet above grade when located adjacent to public walkways.
o
Terminate at least three feet above any forced air inlet located within ten feet.
o
Terminate at least four feet below, four feet horizontally from or one foot above any door,
window, or gravity inlet into any building.
o
Be located at least one foot from any opening through which vent gases could enter a building.
o
Be beyond any combustible overhang.
o
Be installed at a height sufficient to prevent blockage by snow.
Optional outside air supply may be directed to the heater horizontally or vertically.
I
MPORTANT
-
Maximum total vent length allowed for any model heater is 30'.
-
Maximum total fresh air inlet duct length allowed for any model heater is
30'.
-
Total of vent length plus outside air supply duct length cannot exceed 50' for
any heater with minimum heat exchanger length.
-
If condensation in the vent pipe or outside air supply duct is a problem,
shorten or adequately insulate the section
Note:
The above stated requirements assume a maximum of 2 elbows in the
total combination of vent and air supply duct. Subtract 5' of allowable length for
each elbow if 3 or more elbows are used.
Unvented Operation
Requirements for combustion air supply and dilution air vary by jurisdiction, building type and
specific installation details.
See local codes for guidance
. In general, where heaters are installed
without direct outside combustion air, fresh air ventilation must be provided to the building space.
Verify applicable codes.
Optional outside air supply is not recommended for unvented heaters due to possible pressure
imbalances in the building space.
Ensure that minimum combustible clearances are maintained for unvented heaters. Refer to Table
2 for required clearance dimensions.