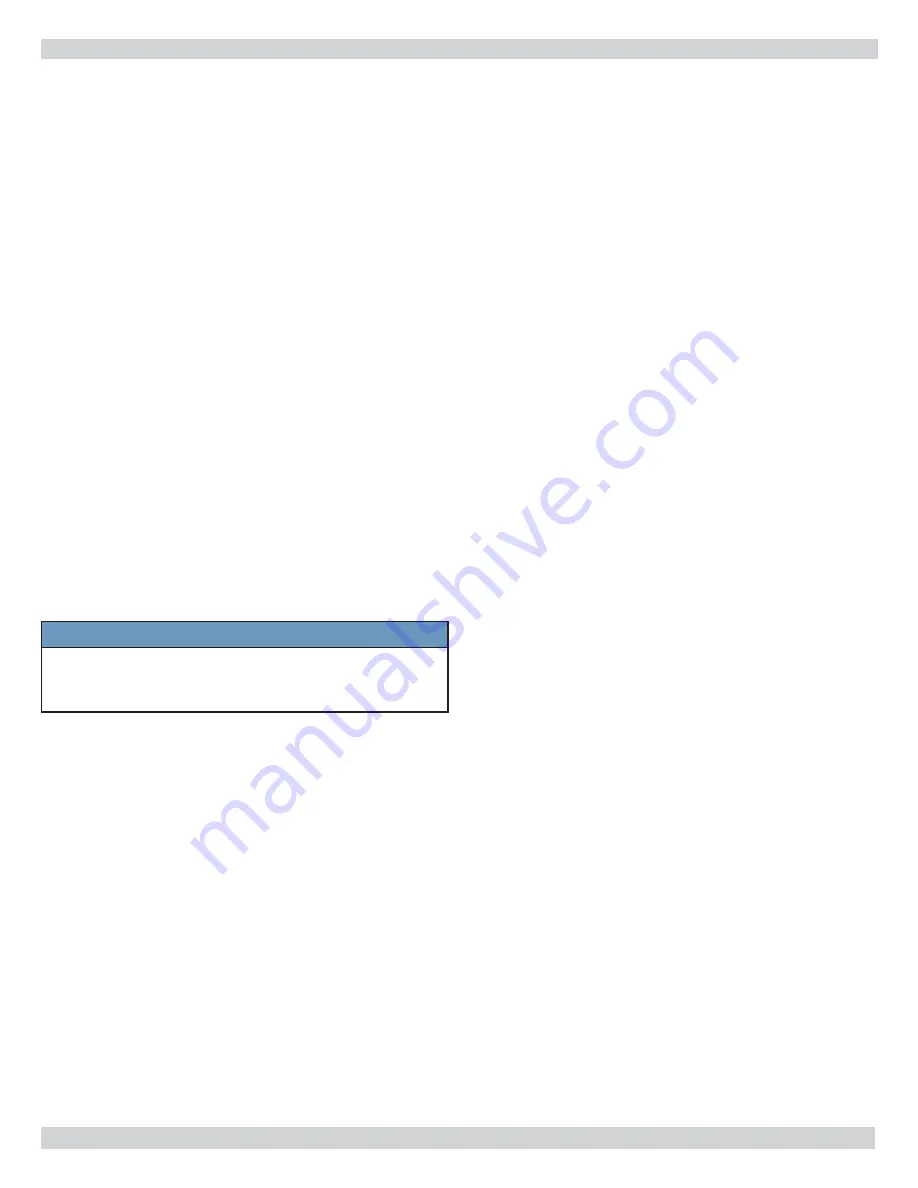
20
• Room used for supplying combustion air should be
isolated from any area served by exhaust fans.
• Refer back to the section on Fresh Air For Combustion
for additional sizing guidelines.
Draft Regulators:
Barometric draft regulator is required
for controlling draft through boiler. Mount barometric draft
regulator in chimney connector. Refer back to section on
“Chimney And Chimney Connections”. Once draft regulator
is installed, use draft gauge to adjust to proper opening:
A. Combustion chamber over
fi
re draft will be
approximately -0.01” WC to -0.02” WC.
B. Stack draft will be approximately -0.02” WC. to
-0.04” WC.
C. Larger installation, greater draft will be required in
stack to obtain desired over
fi
re draft.
Start:
Fill entire system with water. Vent all air from
system following section for Filling The Boiler.
Fuel Units And Oil Lines
:
• Install oil line(s) to oil burner.
• Recommend using heavy wall copper tubing and
fl
ared
fi
ttings, not compression
fi
ttings.
• All connections and joints must be absolutely airtight.
Use an appropriate non-hardening thread sealing
compound on the threaded connections, not Te
fl
on
tape.
• See fuel unit data sheet furnished with the burner for
sizing, lift, and length of tubing recommendations.
Oil burner is equipped with single stage fuel unit
with bypass plug removed for single pipe installation.
Satisfactory where fuel supply is on same level as or
above burner permitting gravity
fl
ow of oil. Per NFPA 31
requirements, never exceed 3 psig pressure to inlet side of
fuel unit.
When necessary to lift oil to burner, two pipe installation
is required. Run return line between fuel unit and oil
supply. When two pipe installation is used, bypass plug
(furnished with burner) must be installed in fuel unit. Refer
to fuel unit instructions furnished with burner for speci
fi
c
instructions on installing bypass plug. Do not exceed fuel
unit manufacturer’s recommendations for running vacuum.
NOTICE
If lift exceeds 14 feet for Beckett burners or 11 feet
for Riello burners, two stage fuel unit is required
with return line.
Install oil
fi
lter of adequate size inside building between
tank shutoff valve and oil burner. For ease of servicing,
locate shutoff valve and
fi
lter near oil burner.
Air Supply For Combustion:
• Do not install boiler in rooms with insuf
fi
cient air, unless
corrective steps are taken.
• It may be necessary to install windows or cut holes in
a door to rooms used for supply air to obtain suf
fi
cient
combustion air and prevent less than atmospheric air
pressure in that room.
• If there is a lack of combustion air, burner
fl
ame will be
dark orange and formation of soot will occur in heating
unit.
• In buildings of conventional frame, brick, or stone
construction that do not have utility rooms, basement
windows, or stair doors, air in
fi
ltration is normally
adequate to provide enough air for combustion and for
operation of barometric draft control.
OPERATING THE BOILER
Nozzles And Electrodes
:
Use proper size, spray angle,
and spray pattern nozzle. Refer to recommended nozzle
selection charts.
To install nozzle, remove nozzle line electrode assembly,
if necessary remove retention ring assembly, and install
and tighten nozzle. Take care not to damage electrode
insulators or bend electrode tips.
After installing nozzle, reassemble nozzle line electrode
assembly and set electrode tip spacing.
Depending on burner type, electrode tip spacing may
need to be set prior to reassembling nozzle line electrode
assembly.
Refer to following pages for setting electrode tip spacing.
Refer to Oil Burner Speci
fi
cations chart for proper pump
pressure and head adjustment.
Summary of Contents for BW4BAH-91
Page 22: ...22 OPERATING THE BOILER Figure 13 Burner Adjustments and Settings...
Page 28: ...28 ELECTRICAL WIRING Figure 16 Honeywell L7248L Control With Beckett AFG Burner...
Page 29: ...29 Figure 17 Honeywell L7248L Control With Riello F5 F10 Burner ELECTRICAL WIRING...
Page 31: ...NOTES...
Page 32: ...CAC BDP 7310 West Morris St Indianapolis IN 46231...