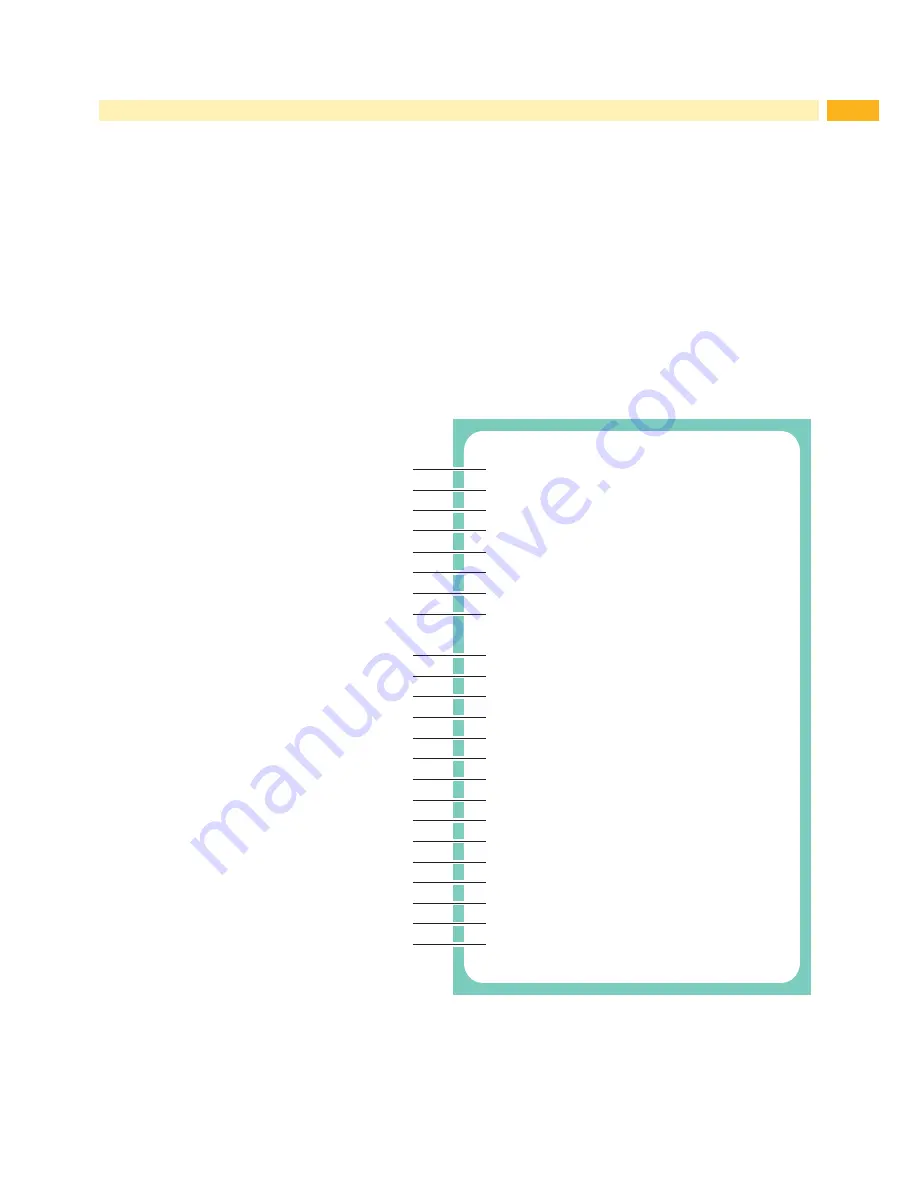
23
6 Operation
6.3
Label Calibration and Self Test
Label Calibration
The printer can automatically detect and store label height.
That means the host computer does not need to transmit the label height to the printer.
Self Test
Self-test function lets you check whether the printer is functioning normally.
Here is how you run the label size calibration and self test.
1. Check that the label stock is loaded correctly.
2. Turn off the printer.
3.
Turn the printer on again, keeping the FEED button pressed. When the LED starts to flash red, release the FEED
button. The printer will now measure the label stock and store the label height.
4. Once the printer has successfully measured the label stock, it will print a self-test label.
The contents of a self-test printout are listed below.
Modell & Version
MACH1/200:GX.XXX
USB ID setting
USB S/N:12345678
Serial port setting
Serial port:96,N,8,1
MAC address of Ethernet port
MAC Addr:xx-xx-xx-xx-xx-xx
IP protocol setting
DHCP Enable
IP address of Ethernet port
IP xxx.xxx.xxx.xxx
Gateway setting
Gateway xxx.xxx.xxx.xxx
Netmask setting
Sub-Mask xxx.xxx.xxx.xxx
##################################
Number of DRAM installed
1 DRAM installed
Image buffer size
Image buffer size:1500 KB
Number of forms
0000 FORM(S) IN MEMORY
Number of graphics
0000 GRAPHIC(S) IN MEMORY
Number of fonts
000 FONT(S) IN MEMORY
Number of Asian fonts
000 ASIAN FONT(S) IN MEMORY
Number of Databases
000 DATABASE(S) IN MEMORY
Number of Scalable fonts
000 TTF(S) IN MEMORY
Free memory size
4073 KB FREE MEMORY
Speed, Density, Ref. Point, Print direction
^S4 ^H8 ^R000 ~R200
Label width, Form length, Stop position
^W102 ^Q100,3 ^E18
Cutter, Label Dispenser, Mode
Option:^D0 ^O0 ^AD
Sensor Setting
Reflective AD:1.96 2.84 2.49[0.88_23]
Code Page
Code Page:850
Printer is on factory default
Default state=Yes