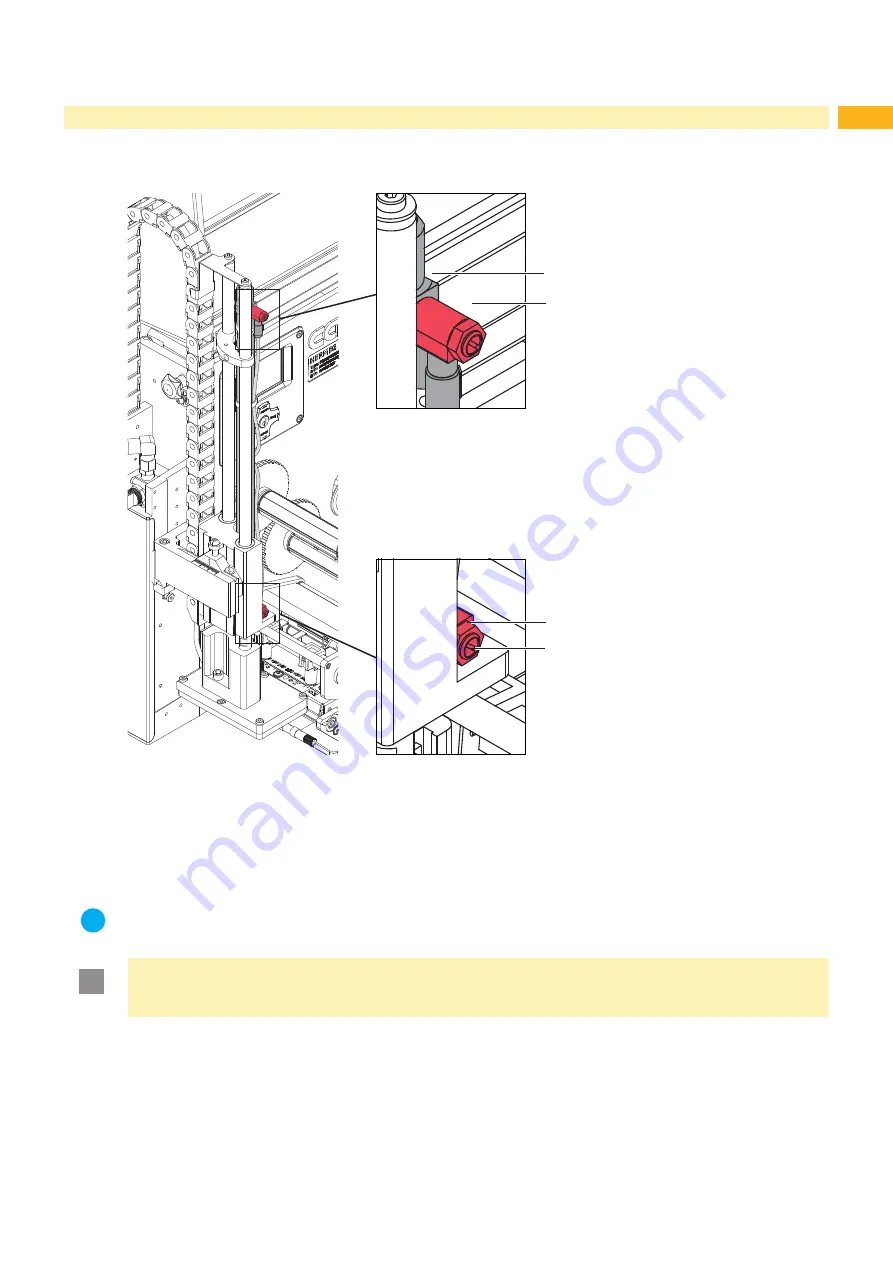
18
19
5
Adjustments
5.2
Pneumatic Adjustments
5.2.1 Adjusting the Pad Movement Speed
1
2
4
3
Fig. 21
Throttle valves on the cylinder
The speed of the pad movement can be regulated via two throttle valves (1, 3).
Adjust the pad movement speed as necessary.
To increase the downward speed turn counterclockwise the screw (4) at the lower valve (3).
To increase the upward speed turn counterclockwise the screw (2) at the upper valve (1).
i
Notice!
The application pressure of the pad is mainly dependent on the downward speed of the pad.
In order to reduce the application pressure turn clockwise the screw (4).
!
Attention!
The time for the downward movement of the pad may not exceed 2 seconds
Otherwise the error message "
Lower position
" will appear.