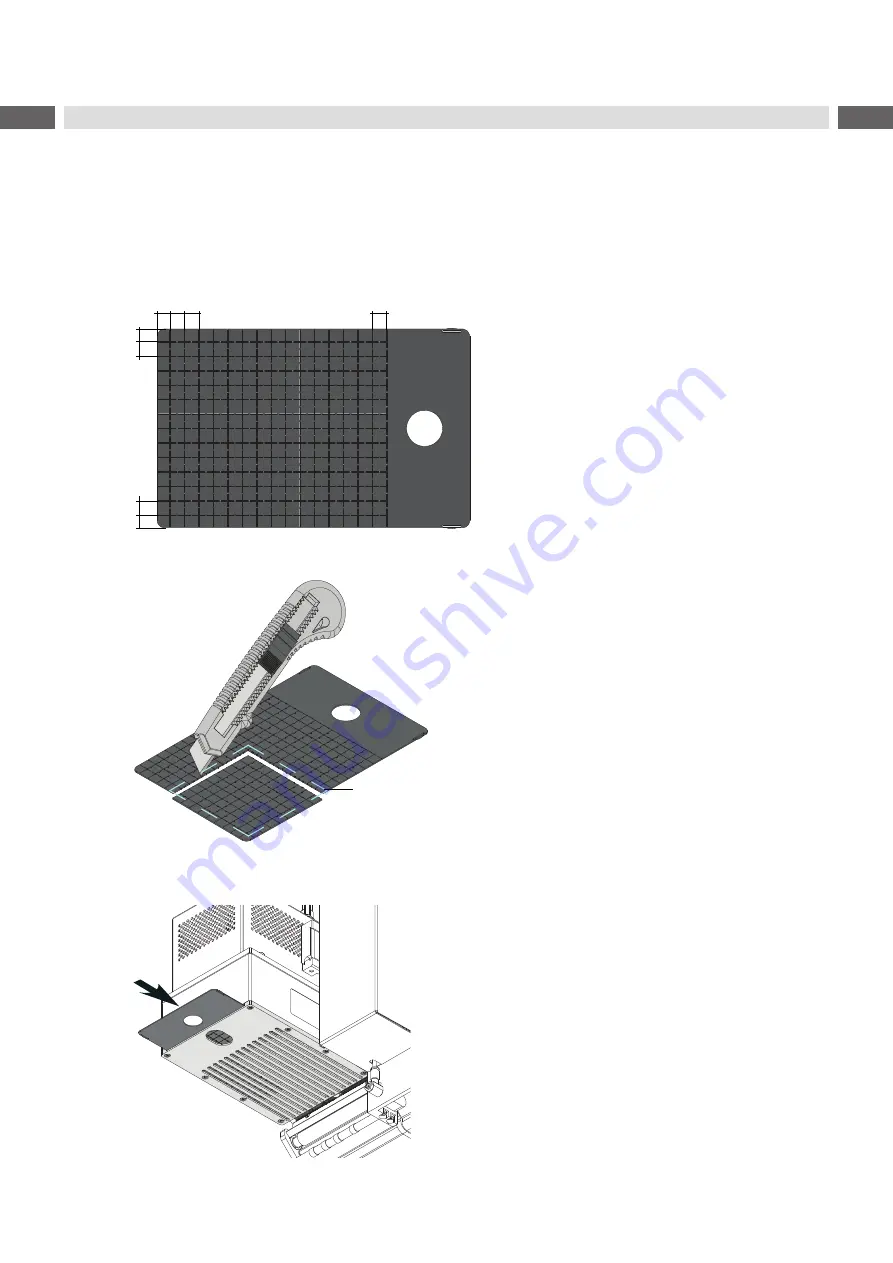
16
16
In order to get the perfect label application it is necessary to set the jets of the applicator to the size and shape of the
used label.
Ideally the settings will have been set by the manufacturer with predetermined labeling material.
Should this not be possible the following steps will assist with the initiation and/or adjustments.
6.2
Sizing the Former Plate
Take a former plate from the accessories kit.
7 8 8
8
7
8
8
7
...
dimensions in mm
Fig. 13
Former plate
Etikett
Fig. 14
Cutting the aperture
1. Place the label on the former plate. Use the front
and a side edge as orientation.
2. Mark the label size on the on thefomer plate.
3. Cut the next inside perforation..
The aperture must be smaller the the label.
Fig. 15
Slide in the former plate
4. Slide the former plate complete into the blow
module. The aperture must be on the base plate
side.