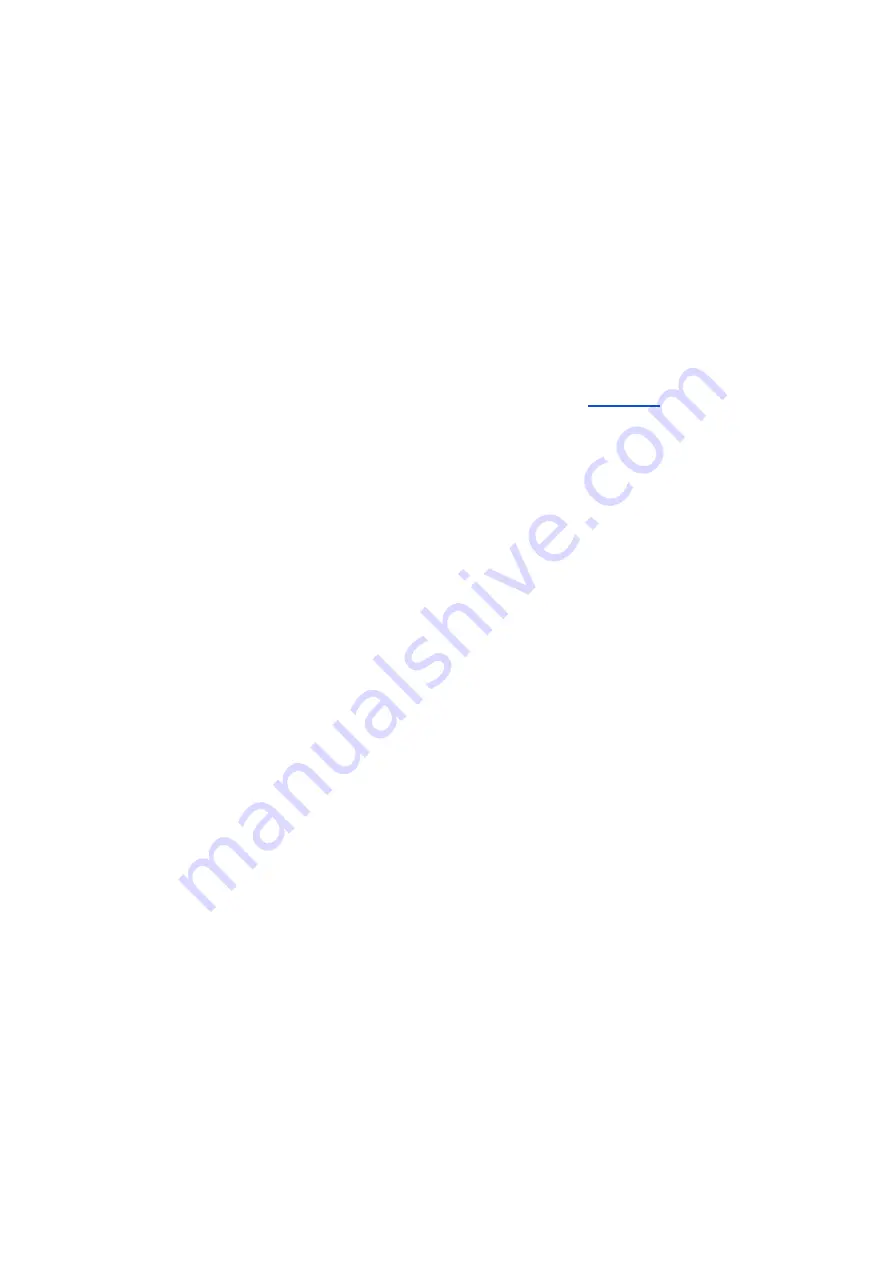
3.4 The Line-Limit Tube
The winch is supplied with a line-limit tube fitted to the line. This item is vital for the correct operation
of the winch.
The sheave assembly mounted at the end of the extending boom incorporates both the main pulley
and, above the line, a smaller wheel. This upper wheel detects when the line-limit tube enters the
sheave assembly and triggers a switch which has two functions, as follows:-
1. It tells the winch to stop pulling the line in, preventing the profiler from impacting the sheave
assembly
2. When performing the pre-launch configuration it enables the winch to position the profiler
automatically a certain distance from the sheave assembly (see
).
The line-limit tube consists primarily of a flexible tube, one that engages with the upper wheel to rotate
it but without applying excessive force to the sheave assembly. In normal operation, because the
recovered line cannot stop instantly, the tube is carried a little distance through the sheave assembly.
The tube is fitted to the line immediately above the line’s suspension loop, the loop that carries the
profiler’s attachment shackle. In this position it typically stops the line recovery with the shackle 65mm
above the plane of the winch’s mounting platform. If the boat’s freeboard is such that this does not
allow reliable communications then the platform may need to be raised, as already mentioned.
7