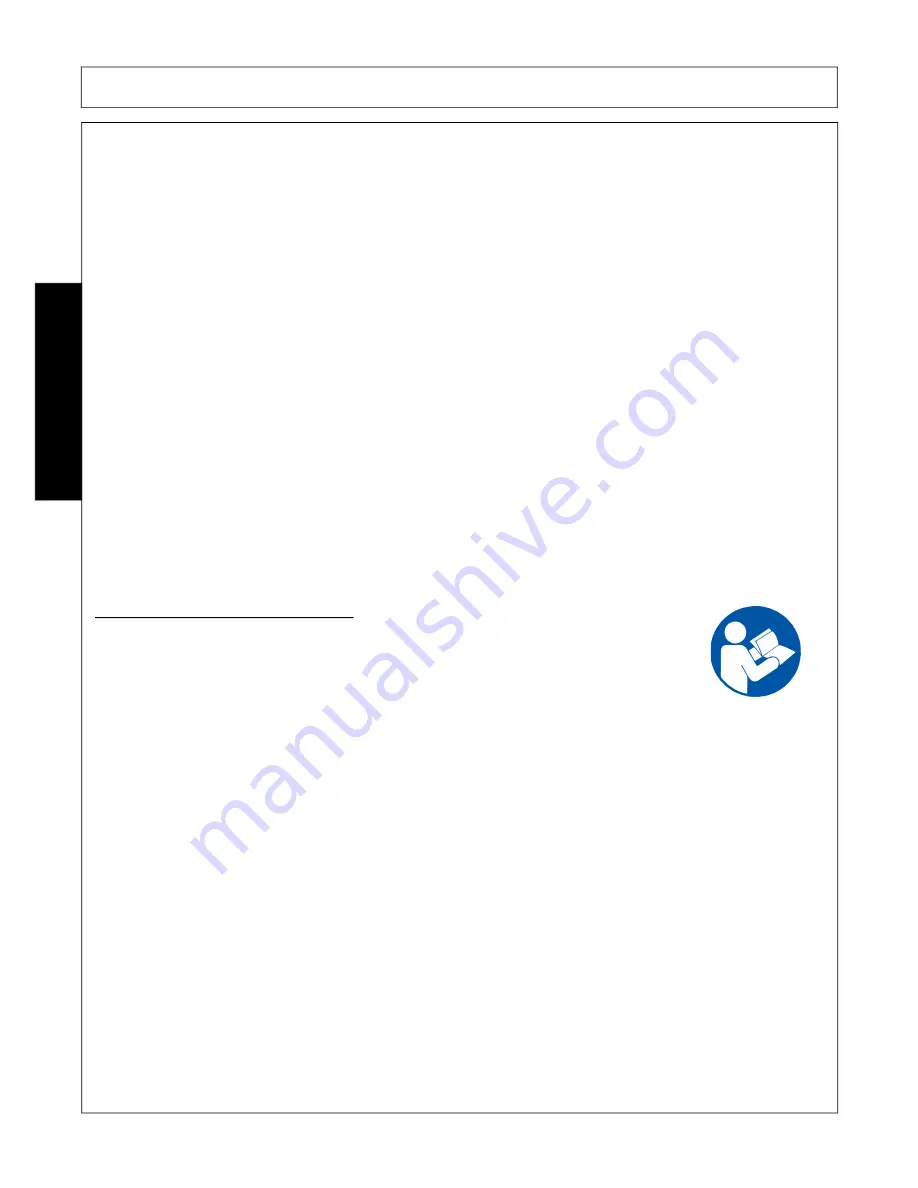
OPERATION
DHP8, DHP10, DHP12 05/21
Operation Section 4-2
O
PE
R
AT
IO
N
© 2021 Alamo Group Inc.
DISC HARROW
OPERATION INSTRUCTIONS
The tillage implement is manufactured with quality material by skilled workers. This implement is ideal in
horticultural, agricultural, or commercial applications.
It is the operator’s responsibility to be knowledgeable of all potential operating hazards and to take every
reasonable precaution to ensure oneself, others, animals, and property are not injured or damaged by the
implement, tractor, or a thrown object. Do not operate the implement if passersby, pets, livestock, or property
are directly in front or to the rear of the unit.
This section of the Operator’s Manual is designed to familiarize, instruct, and educate safe and proper
implement use to the operator. Pictures contained in this section are intended to be used as a visual aid to
assist in explaining the operation of a tillage implement. Some pictures may show shields removed for
purposes of clarity. The operator must be familiar with the implement and tractor operation and all associated
safety practices before operating the implement and tractor. Proper operation of implement, as detailed in this
manual, will help ensure years of safe and satisfactory use of the implement
.
IMPORTANT:
To avoid implement damage, retorque all bolts after the first 10 hours of operation. Refer to the
Torque Chart at the end of the Maintenance Section to ensure bolts are properly tightened.
READ AND UNDERSTAND THE ENTIRE OPERATING INSTRUCTIONS AND SAFETY SECTION OF THIS
MANUAL AND THE TRACTOR MANUAL BEFORE ATTEMPTING TO USE THE TRACTOR AND
IMPLEMENT.
If you do not understand any of the instructions, contact your nearest authorized dealer for a
full explanation. Pay close attention to all safety signs and safety messages contained in this manual and
those affixed to the implement and tractor.
OPS-U- 0001
READ, UNDERSTAND, and FOLLOW the following Safety Messages. Death or serious
injury may occur unless care is taken to follow the warnings and instructions stated in the
Safety Messages. Always use good common sense to avoid hazards.
(SG-2)
Summary of Contents for DHP10
Page 5: ...Safety Section 1 1 SAFETY SECTION...
Page 17: ...SAFETY DHP8 DHP10 DHP12 05 21 Safety Section 1 13 SAFETY 2021 Alamo Group Inc Decals...
Page 19: ...Introduction Section 2 1 2021 Alamo Group Inc INTRODUCTION SECTION...
Page 25: ...Assembly Section 3 1 2021 Alamo Group Inc ASSEMBLY SECTION...
Page 34: ......
Page 35: ...Operation Section 4 1 OPERATION SECTION...
Page 62: ......
Page 63: ...Maintenance Section 5 1 2021 Alamo Group Inc MAINTENANCE SECTION...
Page 65: ...MAINTENANCE DHP8 DHP10 DHP12 05 21 Maintenance Section 5 3 2021 Alamo Group Inc MAINTENANCE...
Page 66: ......
Page 68: ...DHP8 DHP10 DHP12 SOM 05 21 P N 50072116 Printed U S A DHP8 DHP10 DHP12 DISC HARROW...