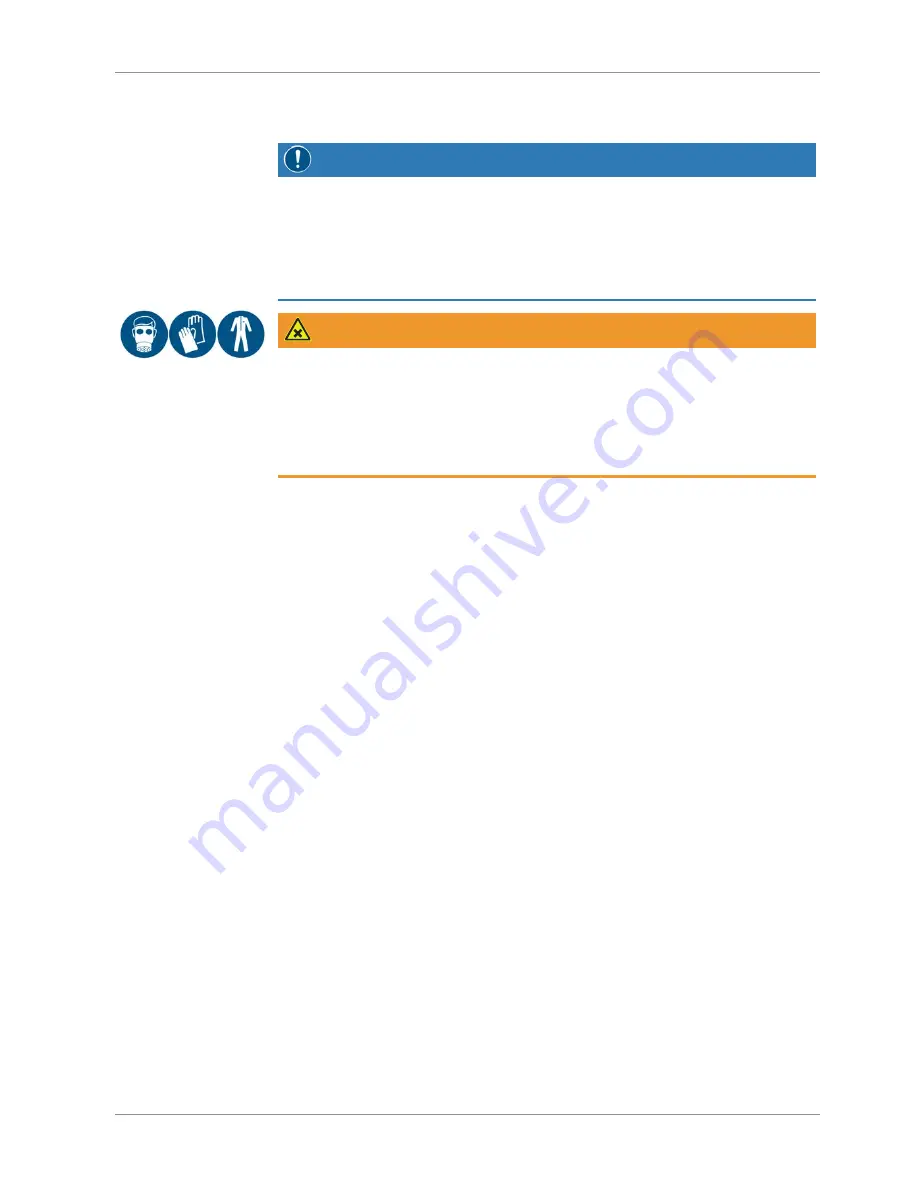
Overhaul | 8
0870569784_RA_RC1000-1600B_-0003_IM_en
19 / 28
8
Overhaul
NOTICE
Improper assembly.
Risk of premature failure!
Loss of efficiency!
• It is highly recommended that any dismantling of the machine that goes beyond any-
thing that is described in this manual should be done through Busch.
WARNING
Machines contaminated with hazardous material.
Risk of poisoning!
Risk of infection!
If the machine is contaminated with hazardous material:
• Wear appropriate personal protective equipment.
In case of the machine having conveyed gas that was contaminated with foreign materi-
als which are dangerous to health:
• Decontaminate the machine as good as possible and state the contamination
status in a ‘Declaration of Contamination’.
Busch will only accept machines that come with a complete filled in and legally binding
signed ‘Declaration of Contamination’.
(Form downloadable from
www.buschvacuum.com
)
9
Decommissioning
• Shut down the machine and lock against inadvertent start up.
• Vent the connected lines to atmospheric pressure.
Version with water-oil heat exchanger:
• Turn off the water supply.
• Disconnect the water supply.
• Open the water by-pass valve (WBV).
• Blow through the water cooling inlet with compressed air.
• Disconnect all connections.
In case of storage is planned:
• See
Storage [
}
7]
.
9.1 Dismantling and Disposal
• Drain the oil.
• Remove the exhaust filters.
• Remove the oil filter.
• Separate special waste from the machine.
• Dispose of special waste in compliance with applicable regulations.
• Dispose of the machine as scrap metal.
All manuals and user guides at all-guides.com