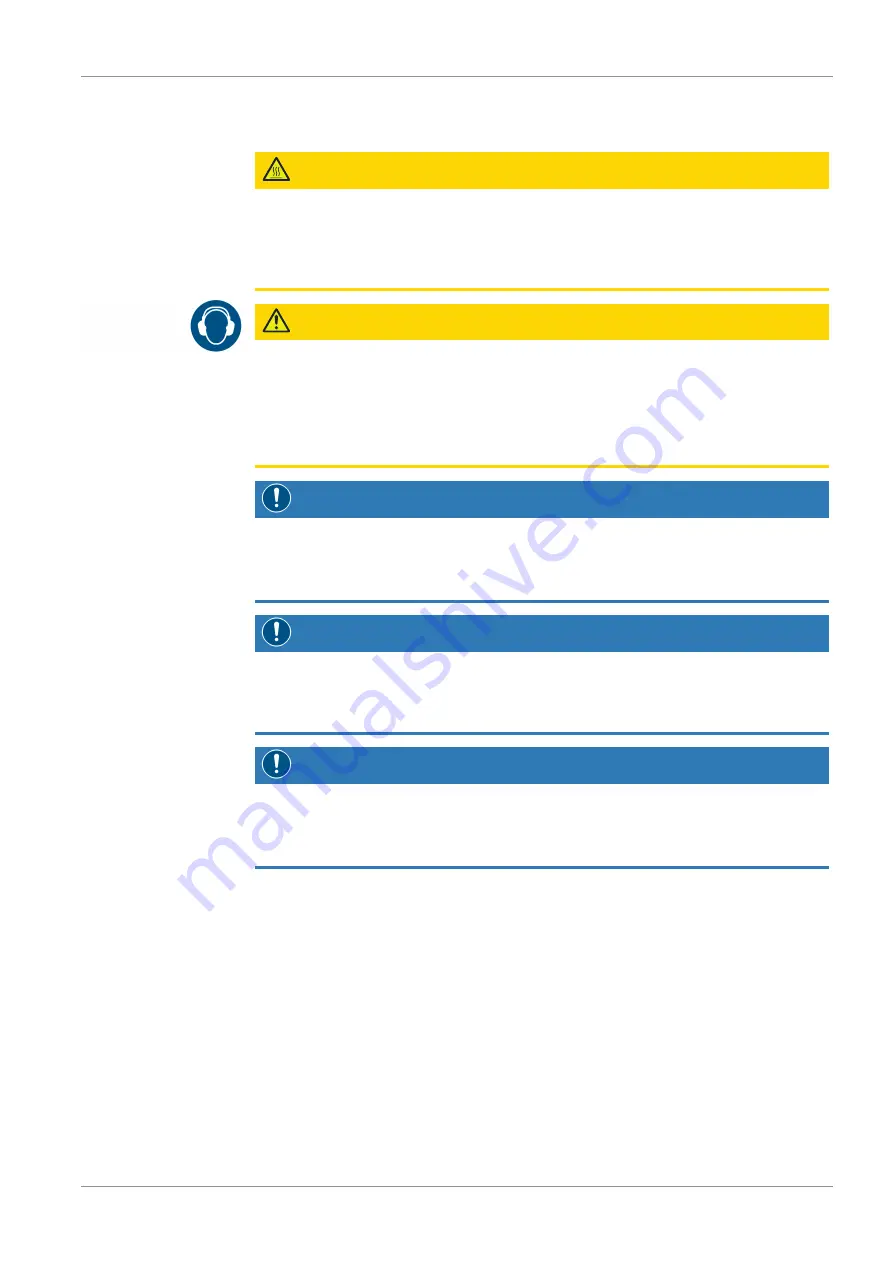
Commissioning | 6
0870203785_WZ3600A_-0001_IM_en
15 / 28
6
Commissioning
CAUTION
During operation the surface of the machine may reach temperatures of more than
70°C.
Risk of burns!
• Avoid contact with the machine during and directly after operation.
CAUTION
Noise of running machine.
Risk of damage to hearing!
If persons are present in the vicinity of a non noise insulated machine over extended
periods:
• Make sure that ear protection is being used.
NOTICE
The machine can be shipped without oil.
Operation without oil will ruin the machine in short time!
• Prior to commissioning, the machine must be filled with oil, see
.
NOTICE
Lubricating a dry running machine (compression chamber).
Risk of damage to the machine!
• Do not lubricate the compression chamber of the machine with oil or grease.
NOTICE
The machine is running at 90 Hz when starting a pump down cycle.
Risk of damage to the machine!
• Read the instructions of the chapter
.
• Make sure that the installation conditions (see
) are met.
• Turn on the water supply.
• Switch on the machine.
• Make sure that the maximum permissible number of starts does not exceed 6 starts
per hour. Those starts should be spread within the hour.
• Make sure that the operating conditions comply with the
• After a few minutes of operation, perform an
.
As soon as the machine is operated under normal operating conditions:
• Measure the motor current and record it as reference for future maintenance and
troubleshooting work.