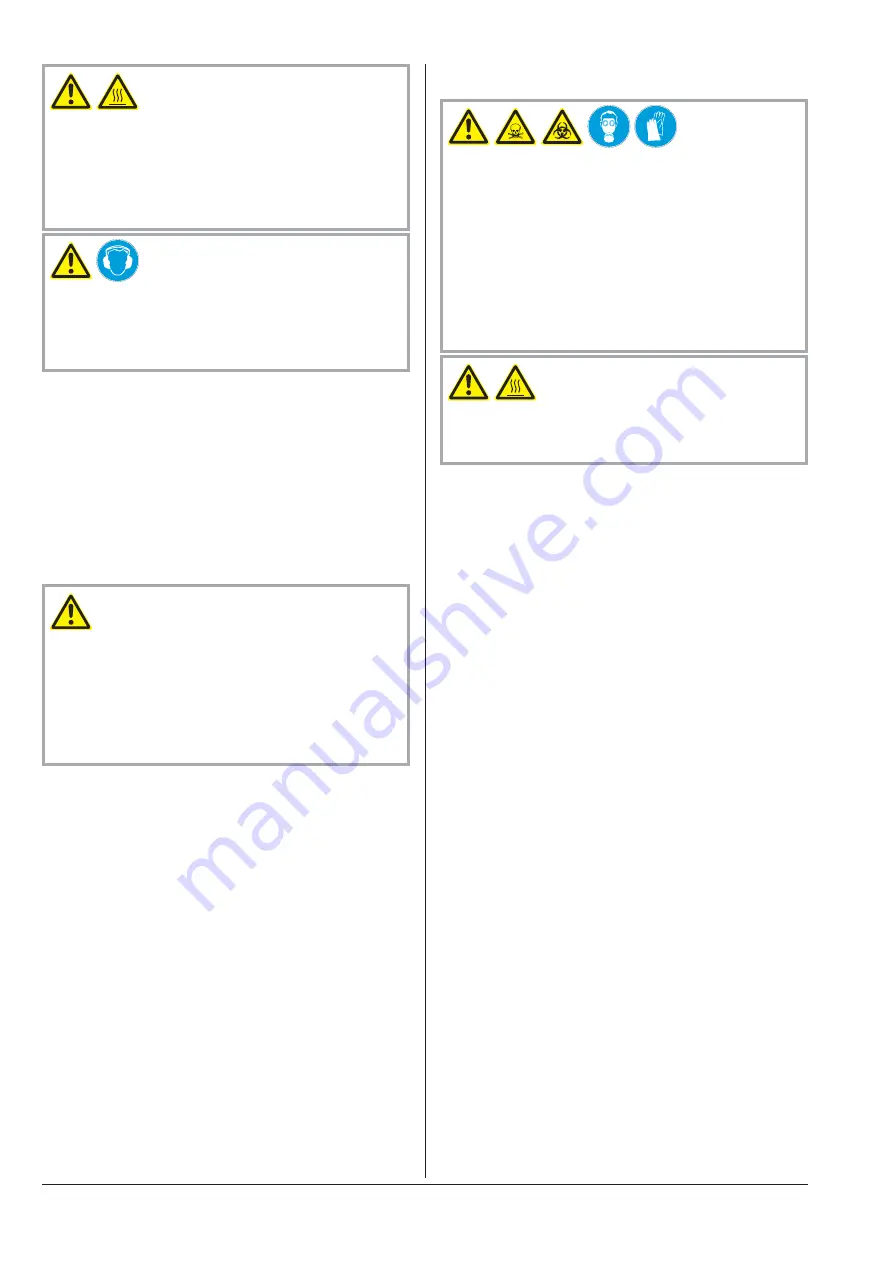
CAUTION
_ac
During operation the surface of the vacuum pump may reach tem-
peratures of more than 70 °C.
Risk of burns!
The vacuum pump shall be protected against contact during opera-
tion, it shall cool down prior to a required contact or heat protection
gloves shall be worn.
CAUTION
_a4
The vacuum pump emits noise of high intensity in a narrow band.
Risk of damage to the hearing.
Persons staying in the vicinity of a non noise insulated vacuum
pump over extended periods shall wear ear protection.
●
Make sure that all provided covers, guards, hoods etc. remain
mounted
●
Make sure that protective devices will not be disabled
●
Make sure that cooling air inlets and outlets will not be covered or
obstructed and that the cooling air flow will not be affected ad-
versely in any other way
●
Make sure that the installation prerequisites (
Ú
page 5: Installation
Prerequisites) are complied with and will remain complied with,
particularly that a sufficient cooling will be ensured
Conveying Condensable Vapours
Version “Aqua”:
CAUTION
_a
Due to the corrosion protection coating CPC the vacuum pump is
capable of conveying water vapour.
Very humid process gases and/or adverse operating cycles can lead
to residual condensates, though, which cause corrosion.
If this is the case, it is necessary to counteract residual condensates
by warming up the vacuum pump, conveyance of ambient air after
process end and regular draining of the anti-pulsation chamber (j).
◆
Close the shut-off valve in the suction line
◆
Warm up the vacuum pump for approx. 10 minutes
At process start:
◆
Open the shut-off valve in the suction line
At the process end:
◆
Close the shut-off valve in the suction line
◆
Open the ambient air valve
◆
Operate the vacuum pump for another approx. 10 minutes
◆
Close the ambient air valve
◆
Regularly drain condensate from the anti-pulsation chamber (j)
Maintenance
DANGER
_age32
In case the vacuum pump conveyed gas that was contaminated
with foreign materials which are dangerous to health, harmful ma-
terial can reside in filters.
Danger to health during inspection, cleaning or replacement of fil-
ters.
Danger to the environment.
Personal protective equipment must be worn during the handling
of contaminated filters.
Contaminated filters are special waste and must be disposed of
separately in compliance with applicable regulations.
CAUTION
_ac
During operation the surface of the vacuum pump may reach tem-
peratures of more than 70 °C.
Risk of burns!
●
Prior to disconnecting connections make sure that the connected
pipes/lines are vented to atmospheric pressure
Maintenance Schedule
Note
: The maintenance intervals depend very much on the individual
operating conditions. The intervals given below shall be considered as
starting values which should be shortened or extended as appropriate.
Particularly heavy duty operation, such like high dust loads in the envi-
ronment or in the process gas, other contaminations or ingress of pro-
cess material, can make it necessary to shorten the maintenance
intervals significantly.
Monthly:
●
Make sure that the vacuum pump is shut down and locked against
inadvertent start up
In case an inlet air filter (h) is installed:
◆
Check the inlet air filter (h), if necessary clean (with com-
pressed air) or replace
In case of operation in a dusty environment:
◆
Clean as described under
Ú
page 8: Every 6 Months:
Every 3 Months:
●
Make sure that the vacuum pump is shut down
●
Check the level of the synchronising gear oil
The level shall be slightly above the middle of the sight glass (e, 76).
The level of the synchronising gear should stay constant over the life-
time of the oil. If the level does fall, the gear is leaky and the vacuum
pump requires repair (Busch service).
Every 6 Months:
●
Make sure that the housing is free from dust and dirt, clean if nec-
essary
●
Make sure that the vacuum pump is shut down and locked against
inadvertent start up
●
Remove the acoustic enclosure
Note
: Make sure that the foam mats do
n o t
get soaked with water
●
Clean the fan cowlings, fan wheels, the ventilation grilles and cool-
ing fins
●
Mount the acoustic enclosure
Maintenance
MM 1324, 1202, 1252, 1322, 1200, 1250, 1320 AV
page 8
0870133276 / 070328