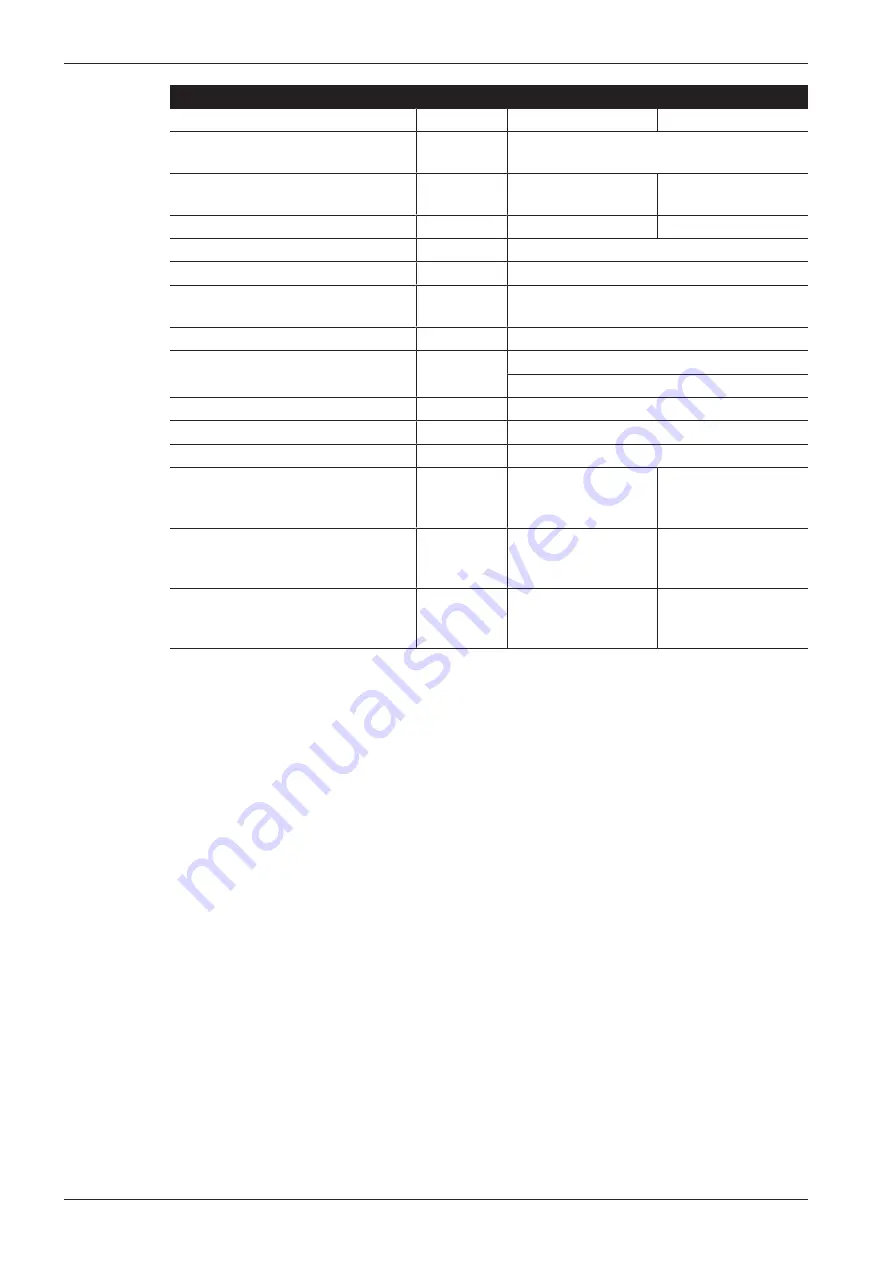
13 | Technical Data
34 | 40
Instruction Manual DOLPHIN LM 0100-0800 A, LT 0130-0750 A_EN_en
LT 0630 A
LT 0750 A
Pumping speed (50Hz / 60Hz)
m³/h
500 / 578
617 / 710
Ultimate pressure (50Hz / 60Hz)
hPa (mbar)
abs.
33 / 33
Maximum overpressure (50Hz /
60Hz)
bar(g)
2.0 / 2.0
2.0 / 2.0
Nominal motor rating (50Hz / 60Hz)
kW
15 / 22
18.5 / 30
Nominal motor speed (50Hz / 60Hz)
min
-1
1450 / 1750
Permitted motor speed range
min
-1
1000 … 1750 (~34 … 60 Hz)
Noise level (EN ISO 2151)
(50Hz / 60Hz)
dB(A)
≤
75 /
≤
76
Vibration velocity – unfiltered (RMS)
mm/s (in/s)
≤
4.0 (
≤
0.16)
Max. allowable gas inlet tempera-
ture
°C
Gas dry
►
120
Gas saturated
►
100
Ambient temperature range
°C
5 … 40
Relative humidity
at 30 °C
90%
Ambient pressure
Atmospheric pressure
Operating liquid requirements
(once through operation only)
m
3
/h
33 mbar
►
3.0
400 mbar
►
1.8
800 mbar
►
1.4
33 mbar
►
3.0
400 mbar
►
1.6
800 mbar
►
1.3
Weight without motor (bare shaft
machine)
Cast iron / full stainless steel
kg
207 / 219
223 / 236
Weight with motor
50 Hz Europe motor / 50 & 60 Hz
multi-voltage
kg
389 / 439
430 / 447