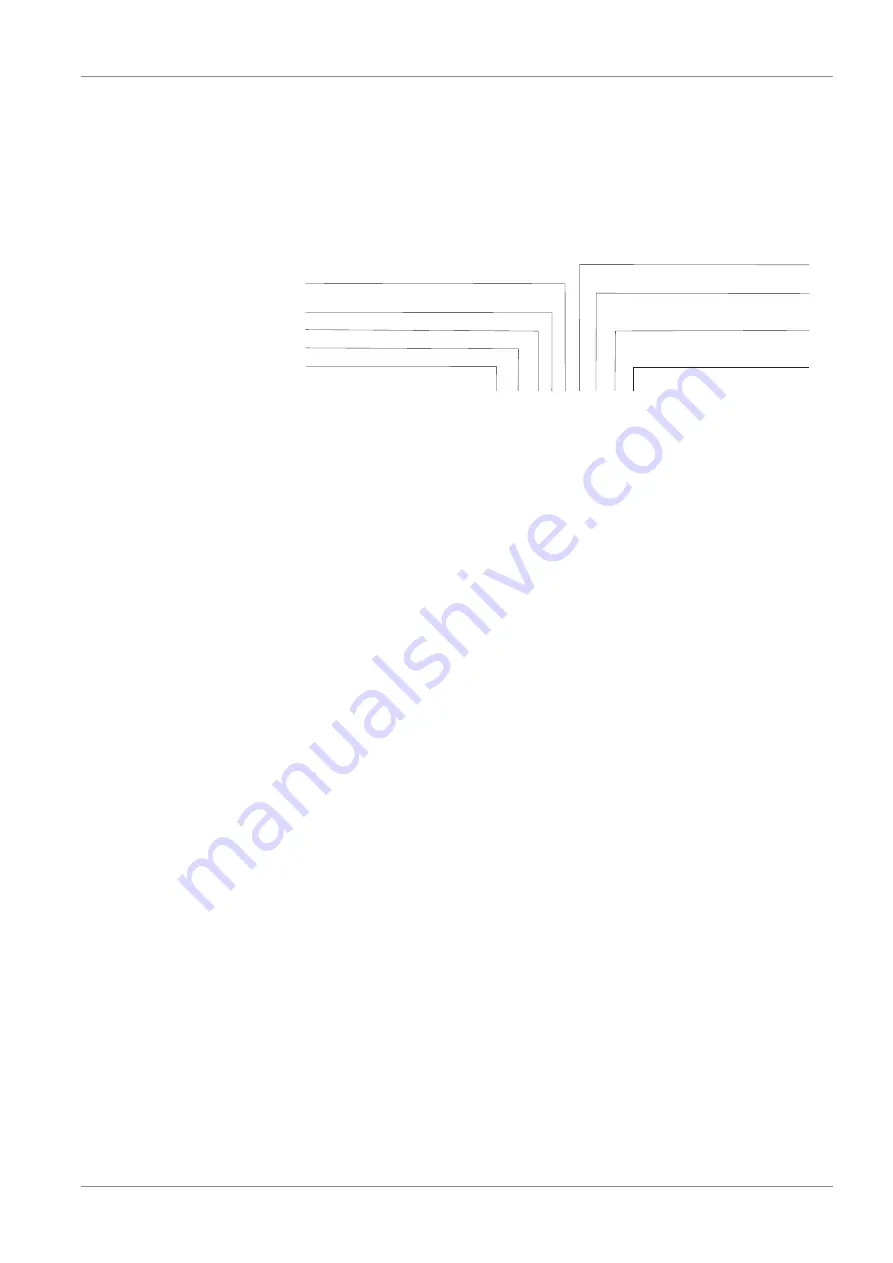
Product Description | 2
Instruction Manual Supplement DOLPHIN VL Systems ATEX_EN_en
9 / 36
2.5 VL System Description
In addition to the nameplate of the vacuum pump, a specific nameplate for the VL sys-
tem is placed onto the base plate.
The VL system description is written on the system’s nameplate. It is defined as in the
following example:
VL 0320 A T K O ZZ M E
Design status of vacuum pump
Size of the vacuum pump
VL = Compact liquid ring vacuum system
M = single stage (LM) vacuum pump
T = two stage (LT) vacuum pump
Motor reference
K = Cast iron construction / 316 stainless steel
M = 316 stainless steel throughout
X = System suitable for non-hazardous area
E = ATEX system
P = Chemical seals (PTFE/FFKM seals and elastomers)
M = Standard seals (Viton)
O = Once through liquid system
P = Partial recirculation liquid system
T = Total recirculation liquid system (plate heat exchanger)
S = Total recirculation liquid system (shell and tube exchanger)
2.6 Start Controls
The machine comes without start controls. The control of the machine is to be provided
in the course of installation.
2.7 Control Concept
2.7.1 Once Through Operation
Operating liquid is continuously supplied to the system whilst it is operating via the inlet
pipe. The process gas and operating liquid are discharged from the vacuum pump to-
gether into the separator vessel (SV) where they are separated. The gas leaves through
the discharge connection and the operating liquid through the operating liquid outlet
connection at the bottom of the separator.
At the operating liquid inlet the Y-strainer (ST) prevents particles greater than 0.1 mm
entering the vacuum pump.
Operating liquid control valve (OPC) allows the operating liquid flow rate to be regulat-
ed for optimum performance of the system, with compound pressure gauge (CG) indi-
cating the operating liquid pressure at the vacuum pump inlet.
The suction non-return valve (NRV) prevents operating liquid from flowing back into the
process when the system stops under vacuum.
The system is stopped if either the flow switch (FS) or resistance thermometer (TSA) lim-
its are reached.
2.7.2 Partial Recovery (Open Circuit)
Approximately 50% of the operating liquid is recirculated within the system whilst addi-
tional liquid is added via the fresh liquid line to maintain the liquid temperature. The pro-
cess gas and operating liquid are discharged from the vacuum pump together into the
separator vessel (SV) where they are separated. The gas leaves through the discharge
connection, whilst the operating liquid level is maintained as excess liquid drains from the
separator overflow connection (OPO). The level indicator (LI) provides visual indicator of
the liquid level in the system.
Through the site control system (by others) the operating liquid temperature is moni-
tored by resistance thermometer (TSA1) opening and closing the solenoid valve (OPV) to
allow fresh cooler liquid into the system. Recommended temperature variation around
the set point for switching is 3°C.
Summary of Contents for DOLPHIN VL 0100 A
Page 34: ...Note...
Page 35: ...Note...