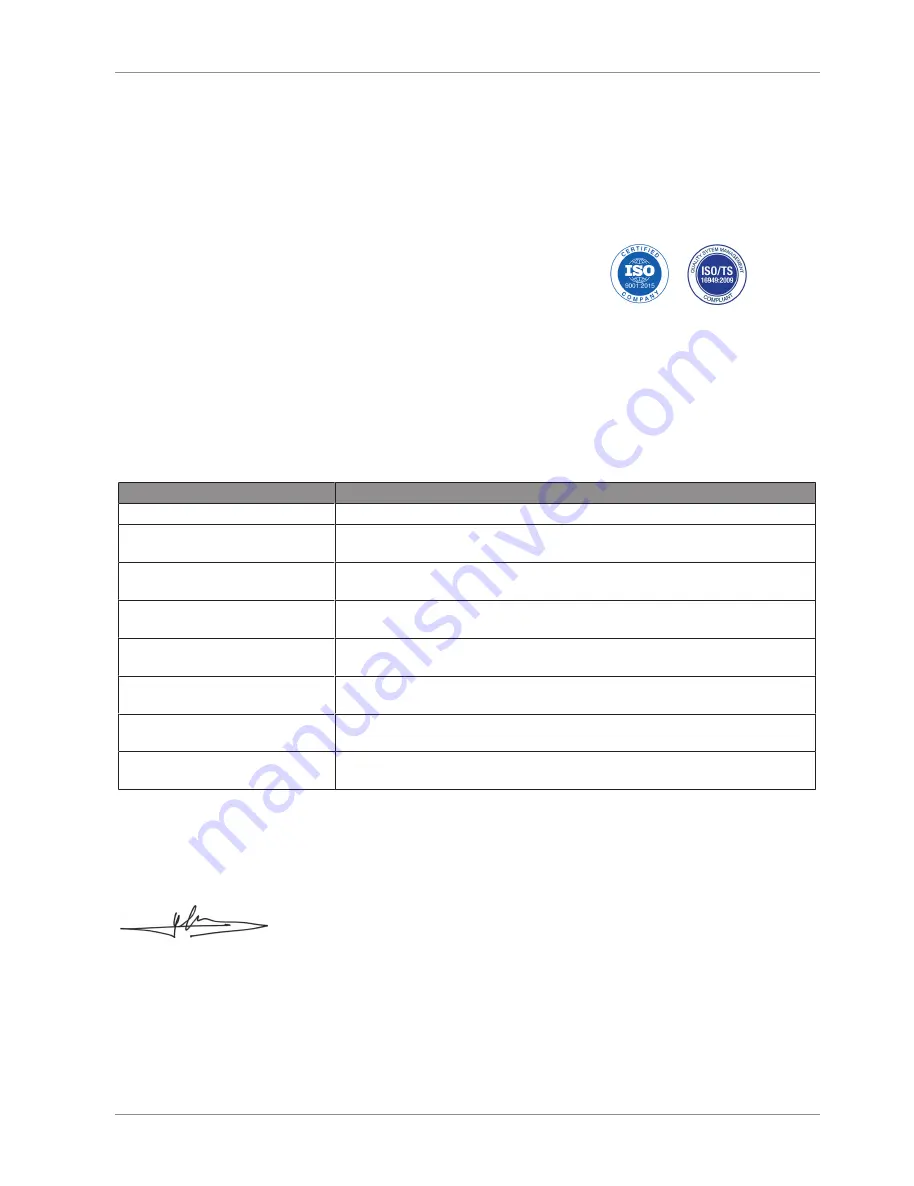
EU Declaration of Conformity | 15
0870567093_NC0630C_ACV_A0002_IM_en
35 / 36
15 EU Declaration of Conformity
This Declaration of Conformity and the CE-mark affixed to the nameplate are valid for the machine within the
Busch scope of delivery. This Declaration of Conformity is issued under the sole responsibility of the manufacturer.
When this machine is integrated into a superordinate machinery the manufacturer of the superordinate machinery
(this can be the operating company, too) must conduct the conformity assessment process for the superordinate
machine or plant, issue the Declaration of Conformity for it and affix the CE-mark.
The manufacturer
Ateliers Busch S.A.
Zone Industrielle
CH-2906 Chevenez
declare that the machine(s):
COBRA NC 0630 C
has (have) been manufactured in accordance with the European Directives:
– ‘Machinery’ 2006/42/EC
– ‘Electromagnetic Compatibility’ 2014/30/EU
– ‘RoHS’ 2011/65/EU, restriction of the use of certain hazardous substances in electrical and electronic equip-
ment
and following the standards.
Standard
Title of the Standard
EN ISO 12100:2010
Safety of machinery - Basic concepts, general principles of design
EN ISO 13857:2008
Safety of machinery - Safety distances to prevent hazard zones being reached
by the upper and lower limbs
EN 1012-1:2010
EN 1012-2:1996 + A1:2009
Compressors and vacuum pumps - Safety requirements - Part 1 and Part 2
EN ISO 2151:2008
Acoustics - Noise test code for compressors and vacuum pumps - Engineering
method (grade 2)
EN 60204-1:2006
Safety of machinery - Electrical equipment of machines - Part 1: General re-
quirements
EN 61000-6-2:2005
Electromagnetic compatibility (EMC) - Generic standards. Immunity for indus-
trial environments
EN 61000-6-4:2007 + A1:2011
Electromagnetic compatibility (EMC) - Generic standards. Emission standard
for industrial environments
EN ISO 13849-1:2015
(1)
Safety of machinery - Safety-related parts of control systems - Part 1: General
principles for design
Person authorised to compile the technical file:
Gerd Rohweder
Busch Dienste GmbH
Schauinslandstr. 1
DE-79689 Maulburg
Chevenez, 11.01.2018
Christian Hoffmann, General director
(1)
In case control systems are integrated.
All manuals and user guides at all-guides.com