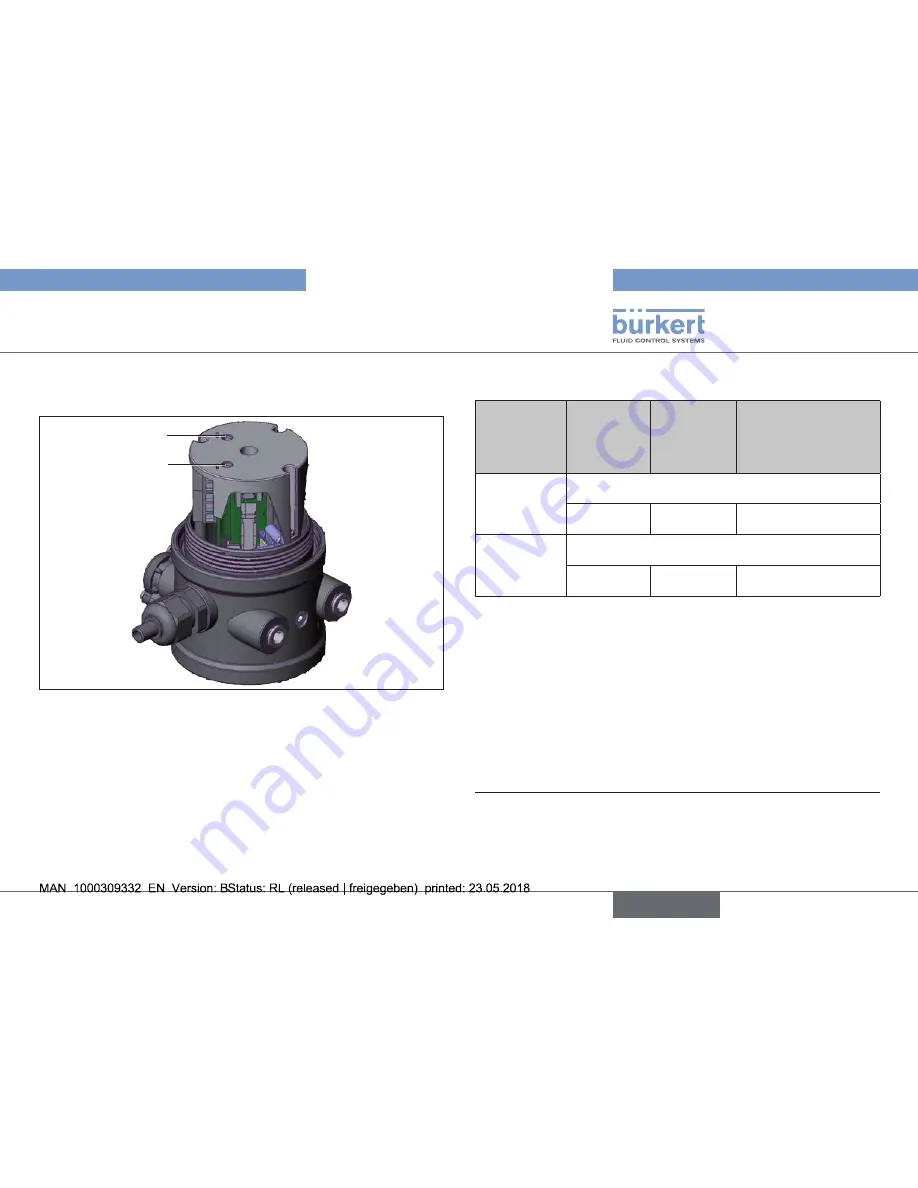
27
Electrical installation
9.4.
Display elements: End position
LEDs
LED Top
LED Bottom
Fig. 25: End position LEDs
9.4.1. Display elements LEDs
Version
with 3-wire
proximity
switches
Version
with 2-wire
proximity
switches
Version with 2-wire
proximity switches
by NAMUR (Ex
version)
6)
End
position top
LED Top
is lit yellow
is lit yellow
goes out
End
position
bottom
LED Bottom
is lit yellow
is lit yellow
goes out
Tab. 7: End position LED yellow
The version with micro switches (mechanical limit switches) does
not include any LED to indicate position.
6)
In the case of the version with 2-
wire
initiators according to NAMUR
the LED function is inverse for technical reasons, i.e. the LED glows
when the end position is not reached and goes out when the end
position is reached.
english
Type 8697
Summary of Contents for 8697
Page 32: ......
Page 33: ...www burkert com ...