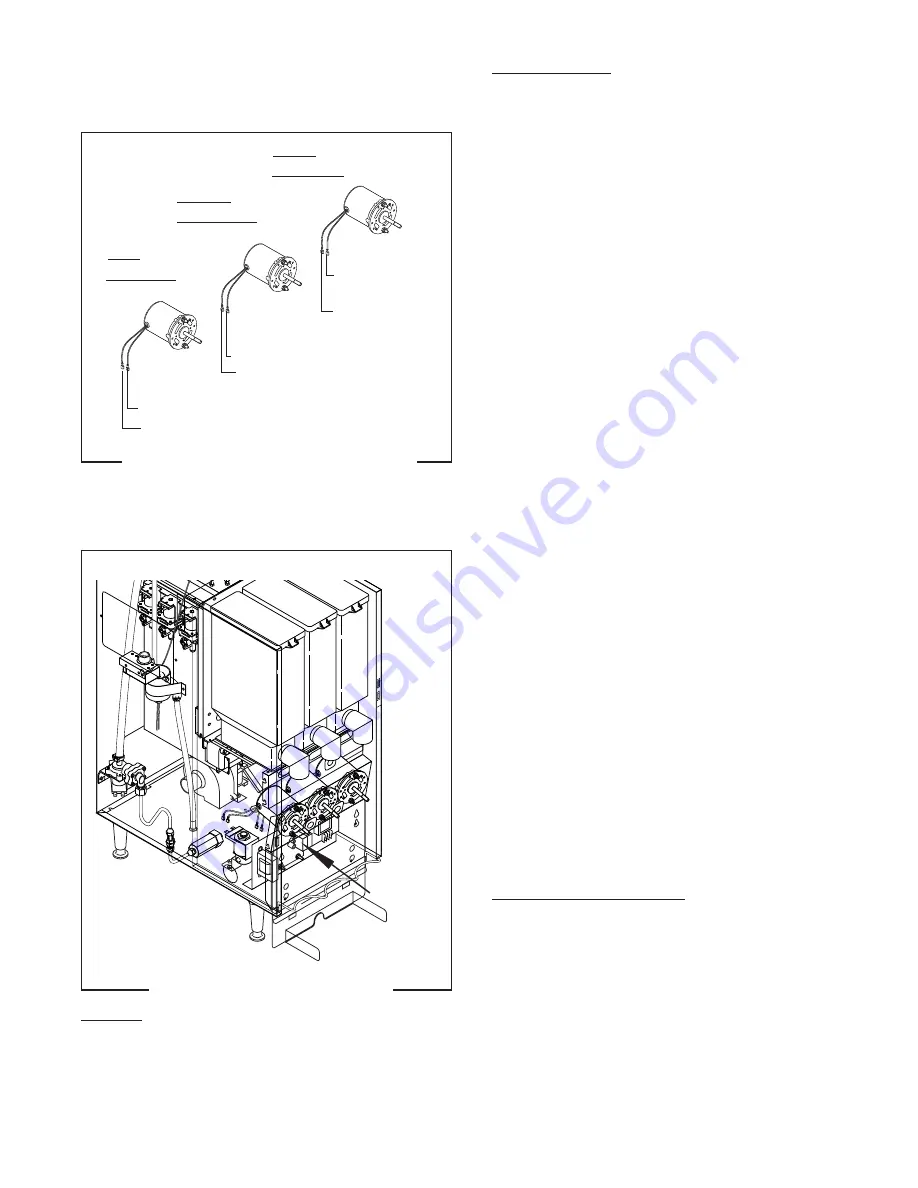
21
SERVICE (cont.)
HOPPER DELAY BOARD
FIG. 14 HOPPER DELAY BOARD
P1445.40
Location
The hopper delay board is located behind the
lower front access panel mounted in the center of the
component bracket.
Test Procedures:
1. Disconnect the dispenser from the power source.
2. Disconnect the eight pin plug on the main wiring
harness from the eight pin connector on the hop-
per delay board.
3. With the rinse/run switch in the “Run”, lower
position, check the voltage across the white and
black wires of the main wiring harness with a
voltmeter. Connect the dispenser to the power
source. The indication must be:
a) 120 volts ac for two wire 120 volt models.
b) 120 volts ac for three wire 120/208 volt or 120/
240 volt models.
c) 240 volts ac for two wire 240 volt models.
4. Disconnect the dispenser from the power source.
If voltage is present as described, proceed to #5.
If voltage is not present as described, refer to the wir-
ing diagram and check the dispenser wiring harness.
5.
Reconnect the eight pin connector of the hopper
delay board to the main harness.
6.
Check the voltage across the terminals on the
auger motor with a voltmeter. Press and hold the
appropriate dispense switch. Connect the dis-
penser to the power source. After a delay of .7
seconds the indication must be:
a) 120 volts ac for two wire 120 volt models.
b) 120 volts ac for three wire 120/208 volt or 120/
240 volt models.
c) 240 volts ac for two wire 240 volt models.
7.
Disconnect the dispenser from the power source.
If voltage is present as described the hopper delay
board is operating properly.
If voltage is not present as described, replace the hop-
per delay board.
Removal and Replacement:
1.
Disconnect the eight pin plug from the hopper
delay board.
2.
Remove the two #8-32 keps nuts securing the
hopper delay board to the component bracket.
3.
Remove hopper delay board and discard.
4.
Install new delay board on the component bracket
using two #8-32 keps nuts.
5.
Reconnect the eight pin connector to the hopper
delay board.
FIG.13 WHIPPER MOTOR TERMINALS
P1451.40
LEFT
FMD-2 & 3
CENTER
FMD-3 ONLY
RIGHT
FMD- 2 & 3
BLK to Main Harness RED
BLK to Main Harness WHI
BLK to Main Harness ORA
BLK to Main Harness WHI
BLK to Main
Harness WHI/VIO
BLK to Main
Harness WHI
FROTHER AND WHIPPER MOTOR (cont.)
28364 011598