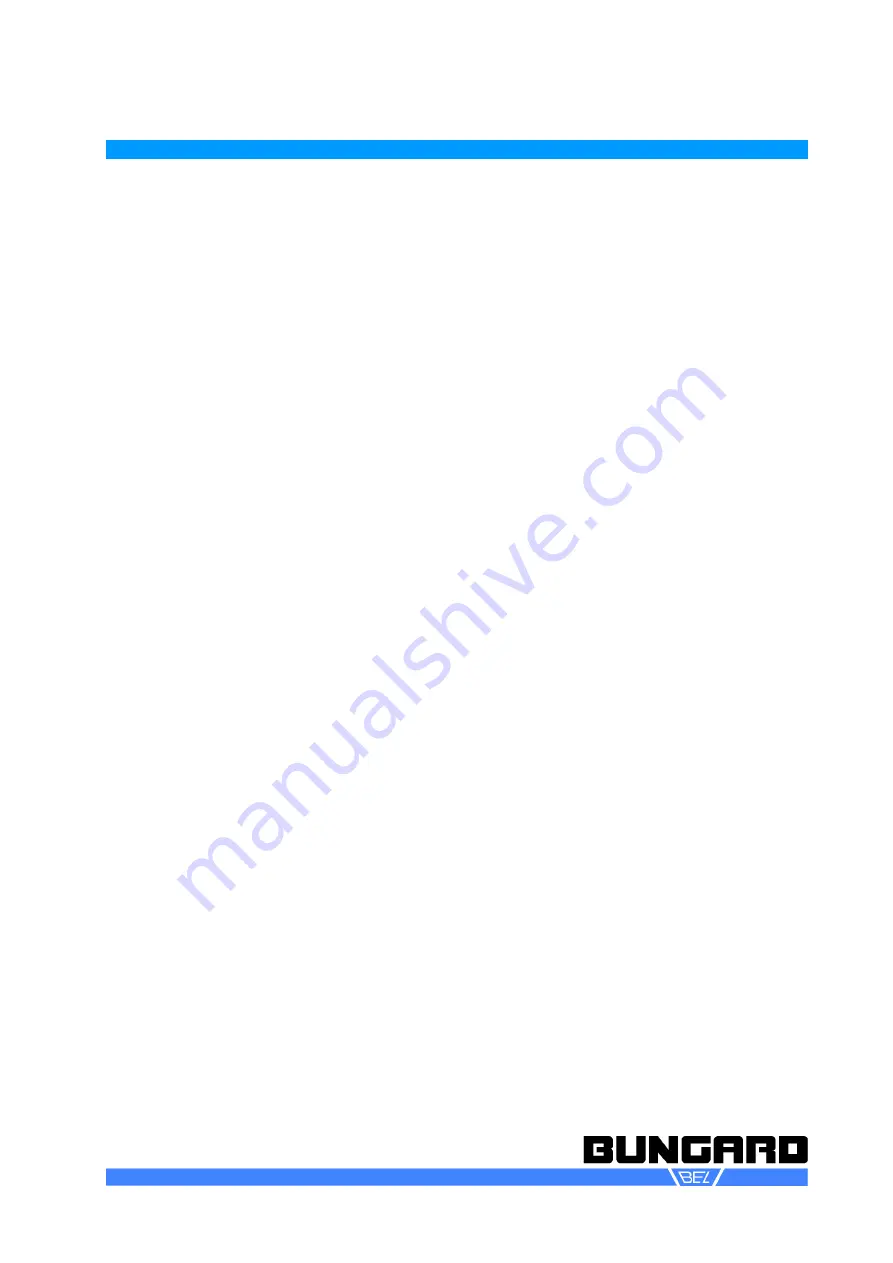
Manual-HotAir-3000-en
Page 8 / 15
The
temperature curve
In the SMT production process, the temperature curve must be adapted to different alloy composi-
tions of solder paste. This temperature curve is one of the most important parameters to ensure
product quality. A standard reflow process typically has five temperature zones. For this reason, you
can define 5 temperature zones in the HotAir3000 software to map the standard reflow process.
Each temperature plane with the appropriate temperature and time performs another function during
the soldering process. The requirement and function of each temperature section are explained be-
low.
Preheating (READY)
Here, the circuit board is heated from room temperature to 120-150°C to remove residual moisture
or residual gas and possibly reduce internal stress in the circuit board. It also achieves a smooth
transition to the next section. The duration is usually 1 - 5 minutes. The specific time and temperat-
ure depends on the size of the board and the number of components.
Heating up (HEAT)
Here, the preheated circuit board is further heated until the flux contained in the solder paste be-
comes liquid. The flux removes oxides of tin paste and component.
Usually the following temperatures are set in this section:
Lead alloy solder and precious metal alloy solder (Sn 42% -Bi58% lead-free or
Sn43% -Pb43% -Bi14% lead containing low-temperature solder)
150 – 180°C
Lead-containing medium temperature solder
180 – 220°C
Lead-free high-temperature solder
220 – 250°C
Soldering (WELD)
Here the reflow process is basically completed. Since the highest temperature is used here, temper-
ature-sensitive components can easily be damaged. The physical and chemical changes within the
solder paste are the biggest here and the molten solder can easily oxidise by air in combination with
high temperature. The settings of this stage are based primarily on the data of tin pastes.
Solder pastes are usually classified into low temperature solder pastes (150-180°C), medium tem -
perature solder pastes (190-220°C) and high temperature solder pastes (230-260°C).
The lead-free solder used today is a high-temperature solder.
Lead-free low-temperature solder paste usually contains precious metals. Leaded low temperature
solder paste is rarely used and then for special applications. Lead solder has excellent electrical,
physical and mechanical properties, e.g. Temperature change and oxidation resistance.
In this phase, the solder should be liquid so that the components will float and automatically center
and align with the surface tension of the liquid solder. In addition, 2 intermetallic phases are formed
between the circuit board and component, in which the tin mixes with the copper of the circuit board
and the metal of the component and forms the ideal brazing structure.
The soldering time is usually about 10-30 s. Larger boards and circuit boards with components that
form large soldering shadows require a longer soldering time.
Generally, the soldering time should be kept as long as necessary and as short as possible so as
not to expose the components to unnecessary thermal stress, which can lead to component mal -
function.
Bungard Elektronik GmbH & Co. KG, Rilkestraße 1, 51570 Windeck – Germany
Tel.: +49 (0) 2292/9 28 28 - 0, Fax: +49 (0) 2292/9 28 28 - 29, E-mail: [email protected]