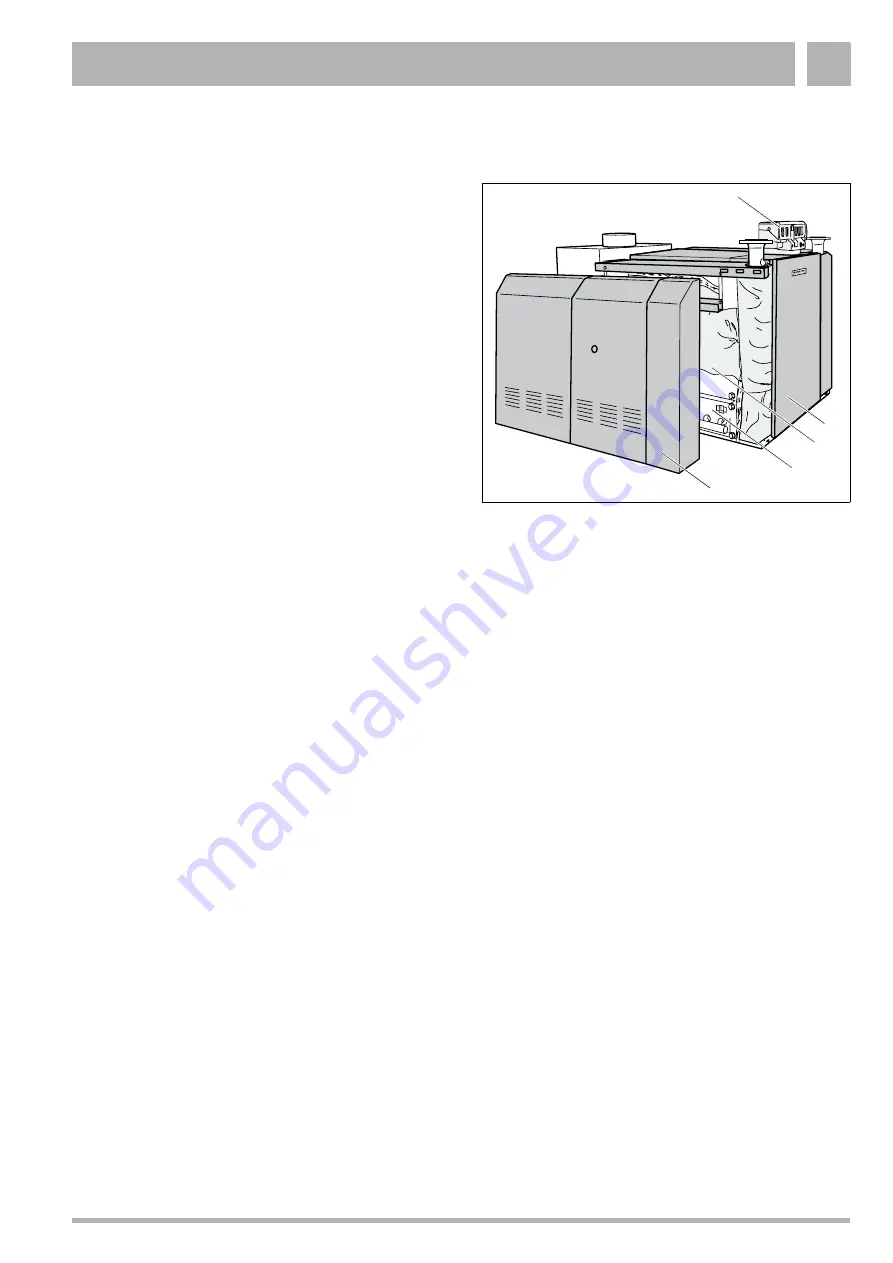
Product description
3
11
We reserve the right to make any changes due to technical modifications.
Commissioning and maintenance instructions Logano GE434 Gas-fired special boiler • Issue 02/2003
Buderus Heiztechnik GmbH • http://www.heiztechnik.buderus.de
3
Product description
The Logano GE434 (Fig. 1) boiler comprises a r.h. and
a l.h. boiler block, each of which is equipped with a
separate gas burner.
The main components of this boiler are:
–
Boiler blocks (Fig. 1,
Item 5
) and gas burner (Fig. 1,
).
The boiler blocks transfer the heat generated by the
burners to the heating water.
–
Boiler casing (Fig. 1,
Item 2
) and thermal insulation
Item 5
).
The boiler casing and thermal insulation prevent
energy loss.
–
Control device (Fig. 1,
Item 3
), auxiliary control
device and two burner control units (one burner
control unit for each burner).
The control device and the burner control unit
monitor and control all electrical boiler components.
Fig. 1
Logano GE434
Item 1:
R.h. gas burner
Item 2:
Boiler casing
Item 3:
Control panel
Item 4:
Boiler front panel
Item 5:
R.h. boiler block with thermal insulation
3
4
1
2
5