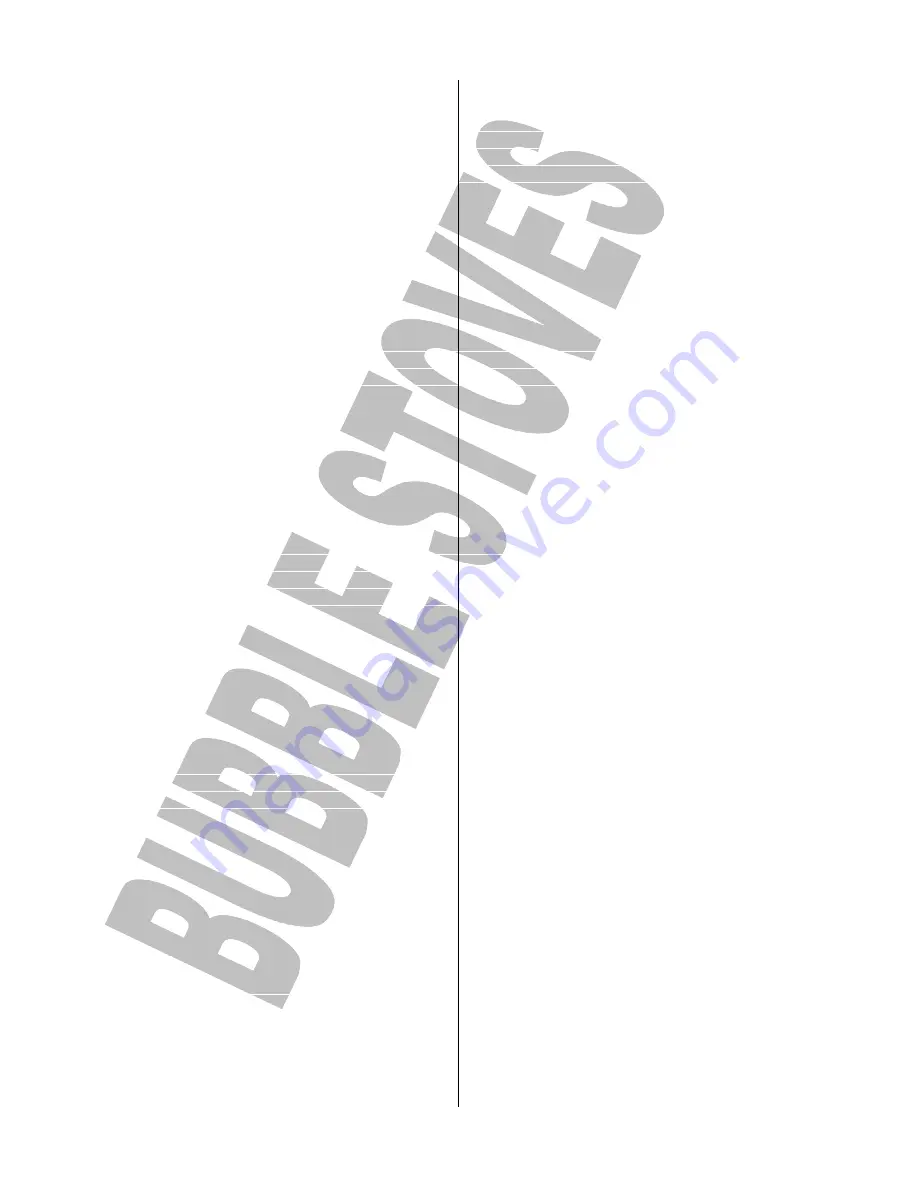
12
other devices that can be used to interfere with the
free flow of water.
PUMPED SYSTEMS
Always come off the stove with 28mm copper for a
minimum run of 350 mm before dropping on to 22mm
hep 2o
To ensure suitable flow of water through the
primaries a suitable injector tee should be used.
Great care should be taken with the positioning of the
circulating pump and the feed and expansion tank to
make sure that the water flows where it should and
that over pumping does not occur.
The heating circuit must be piped in 22mm copper or
hep 2o with 15mm stabs to radiators.
Where additional radiators are fitted as heat leaks,
the pipe work must be kept as short as possible, rise
on feed and fall on return.
SAFETY VALVE.
A 1" safety valve must be fitted as close to the boiler
as possible (within 300mm) and the outlet from it must
be directed to a safe location so as not to present any
danger should the valve blow-off and exit steam or
boiling water.
Note
Safe location could be through the side of the boat,
with a deflector to stop any horizontal emission.
WATER TREATMENT.
To reduce the build up of lime scale in the primary
circuit pipe work the temperature of the water should
not be allowed to exceed 65 Deg C and a suitable
water treatment should be added.
If the boat is to be left unattended the water, in the
heating system should also have suitable antifreeze
added or be drained down.
DRAIN DOWN.
A drain down valve should be fitted at the lowest point
of the circuit.
CIRCULATING PUMP.
On pumped systems make sure that the circulating
pump is fitted in such a way as to make it easily
replaceable, this means lock shielded valves at either
side and easy access.
7
7
.
.
C
C
O
O
M
M
M
M
I
I
S
S
S
S
I
I
O
O
N
N
I
I
N
N
G
G
.
.
If the stove has been fitted to an existing heating
system, make sure that the system is adequately
designed and complies with the details specified in
this manual.
If the heating circuit does not comply, it must be
modified, before attempting to light the stove.
Commissioning takes the following form:
PRE FIRING CHECKS.
LIGHTING.
POST FIRING CHECKS AND ADJUSTMENTS.
PRE FIRING CHECKS.
Fuel supply tank- check for leaks-stability-height-
position-vent.
Fuel- check for correct grade.
Filter- is it fitted-check for function and leaks.
Oil line- check for function, positioning, material
suitability and leaks.
Fire valve check for function and leaks.
Through Bulkhead Sleeving - Check that it is fitted
and sealed.
Isolation valve-check for function, convenience of
positioning and leaks.
Flush at least 5 litres of oil through the line to check
for contamination and to clear the oil line of
installation debris and trapped air.
Make sure that the oil feed supply pipe is level and has
no potential for air locking. (Kinks, wavy runs, and
sudden changes in level or slope).
Electrical- check for correct fusing, location and
specification of any isolation devices.
Ventilation make sure that adequate ventilation is
provided in line with boat safety scheme.
Water systems should be pre-checked for leaks and
tests must be made to make sure that water will flow
freely through the boiler and that the boiler and pump
is vented and free from trapped air.
Make sure that the heat leak circuit is adequate and
unvalved.
Chimney system should be checked to make sure that
it complies with the relative standards, regulations and
all other instructions given.