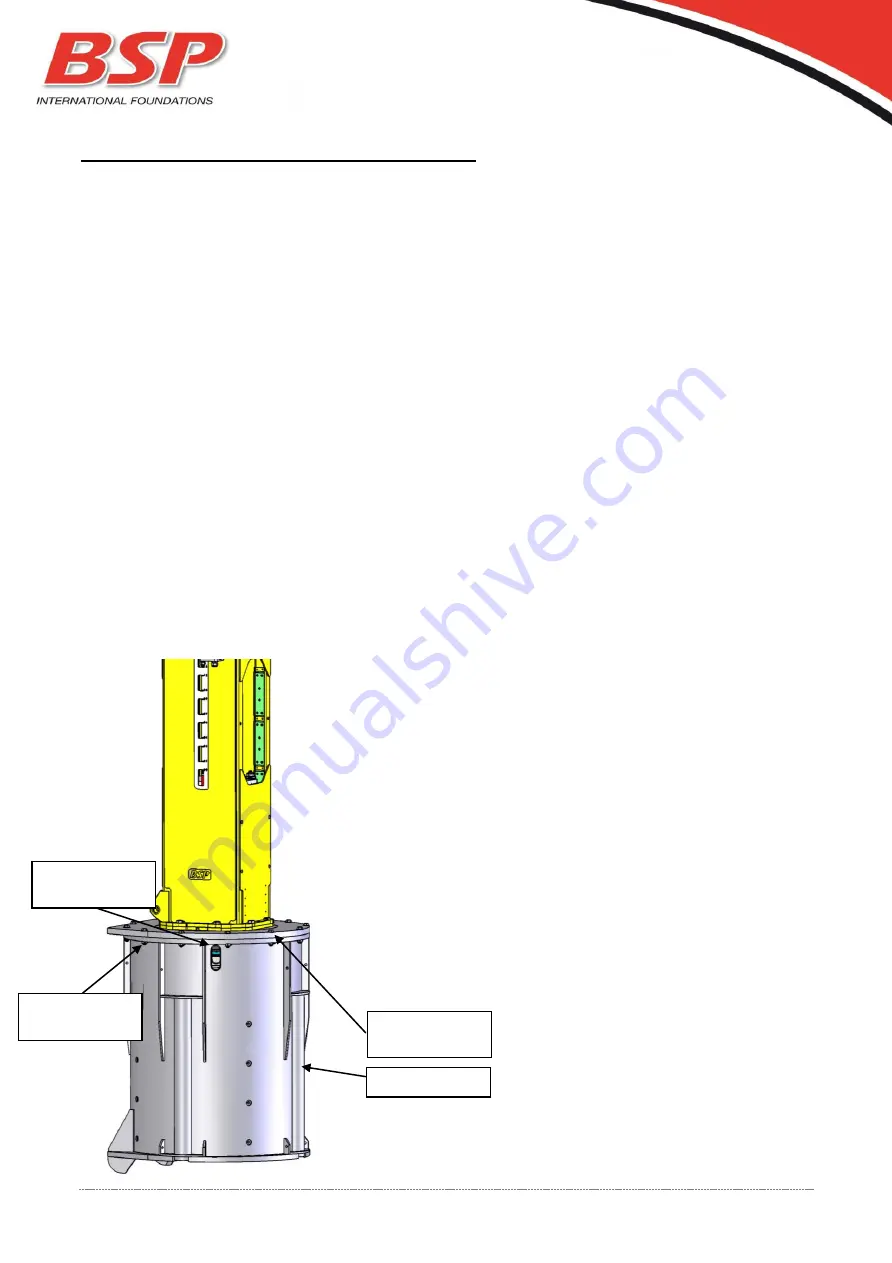
4421 1999 REV -
Page 28
4.6 Dolly Selection & Replacement
Selection of Cushion Material
BSP recommends the use of a Cast Nylon material which has been specifically processed suitable for
piling use.
To protect the pile from damage during driving the combination of Elastic Modulus and assembly thick-
ness should not result in a stiffness of greater than 3.4 MN / mm.
The use of dolly systems of greater stiffness will result in damage to the drive cap and drop
weight
a) Circumstances indicating dolly replacement is required is typically
Reduced driving performance
Fragments of dolly material discharged from hammer
Evidence of extrusion of melted material
Dolly replacement will be more frequent in cases of prolonged periods of driving
Depending on hammer configuration dolly condition can be visually assessed by
Inspecting condition by dropping the drive cap / helmet out of the drive cap retainer for simple
leader hammers
For hammers with non revolving type rope suspended drive caps lifting the hammer off pile so
that the dolly impact surface is exposed
b)
Dolly replacement procedure
For hammers with enclosed drive cap retainer.
Dolly maintenance is best carried out with the hammer vertical,
supported by the crane.
Remove M36 bolts connecting the cage bottom adapter to the
pile sleeve
Lift hammer off pile sleeve and lower off to lay on ground
Remove worn dolly from drive cap, it may be necessary to lift
drive cap off pile sleeve and tip over. CAUTION beware of dolly
disc trapping limbs
Clean out dolly recess
T
hese hammers must be fitted with the cast nylon dolley
4421 0583 to reduce risk of the dolley assembly becoming
displaced from the drive cap whenever the hammer is
lowered horizontally to the ground
Pile Sleeve
12 x M36
Fixing Bolts
Dolley Viewing
Aperture
Cage Bottom
Adapter