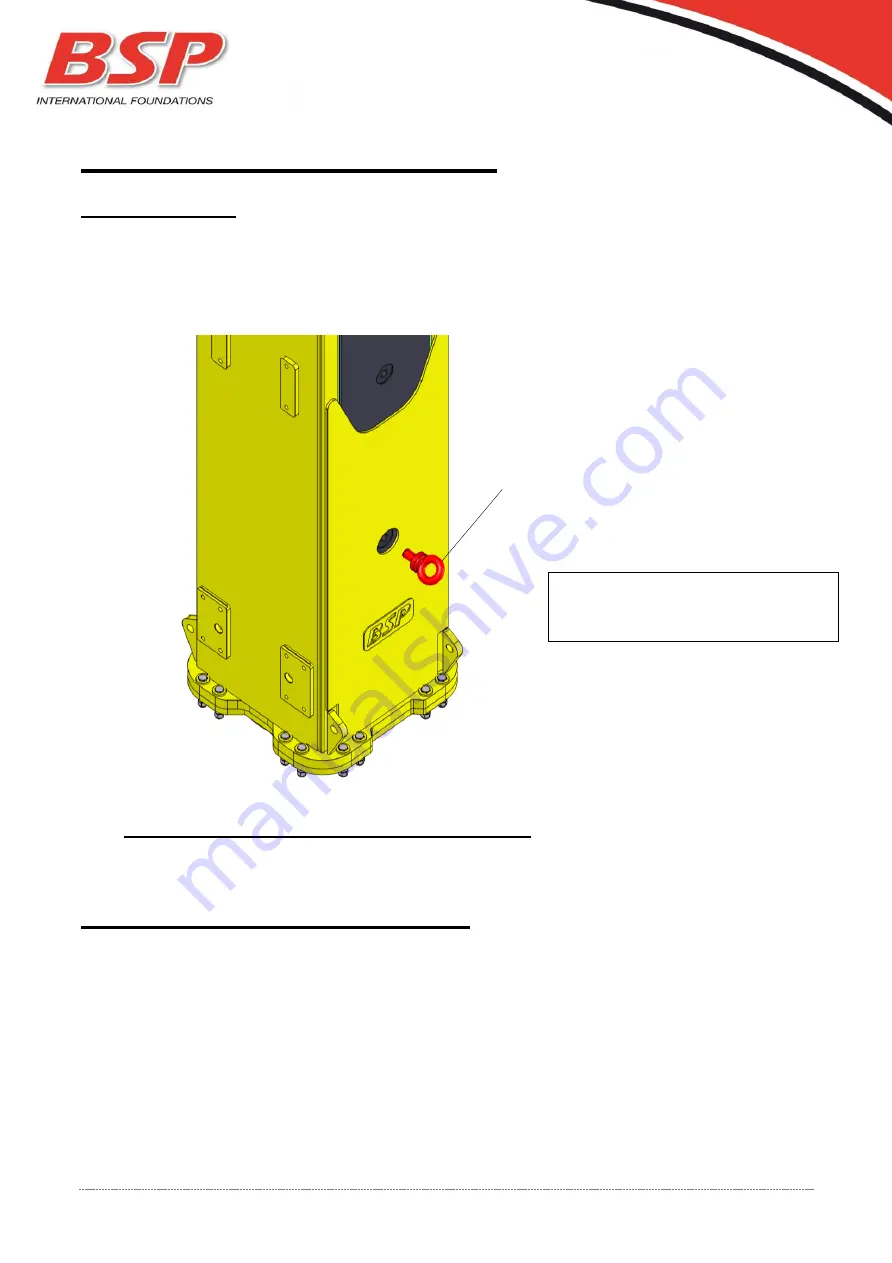
4421 1999 REV -
Page 24
REGULAR MAINTENANCE
4.1 Transport
Whenever the hammer is configured for transport from site to site, the ram must be secured to the
cage to prevent unintentional movement. An eyebolt must be screwed into the ram through a hole
in the side of the cage.
Provision is made for this on either side of the hammer to suit the mounting configuration.
Eyebolt
The eyebolt must be removed before the hammer is used
4.2 Initial Set-up for NEW hammer
a)
Connect hammer hose catenary and visually inspect.
b)
Install control panel in cab.
c)
Purge hoses (refer to next section)
d)
Visually inspect hammer.
e)
Check accumulator pre-charge.
f)
Remove travel stop eyebolt.
g)
Pressurise systems and fill hoses.
h)
Check hydraulic oil level and top up if necessary.
i)
The hammer is now ready for use.
Failure to fit the eyebolt prior to
transport, may result in damage to
the hammer and persons