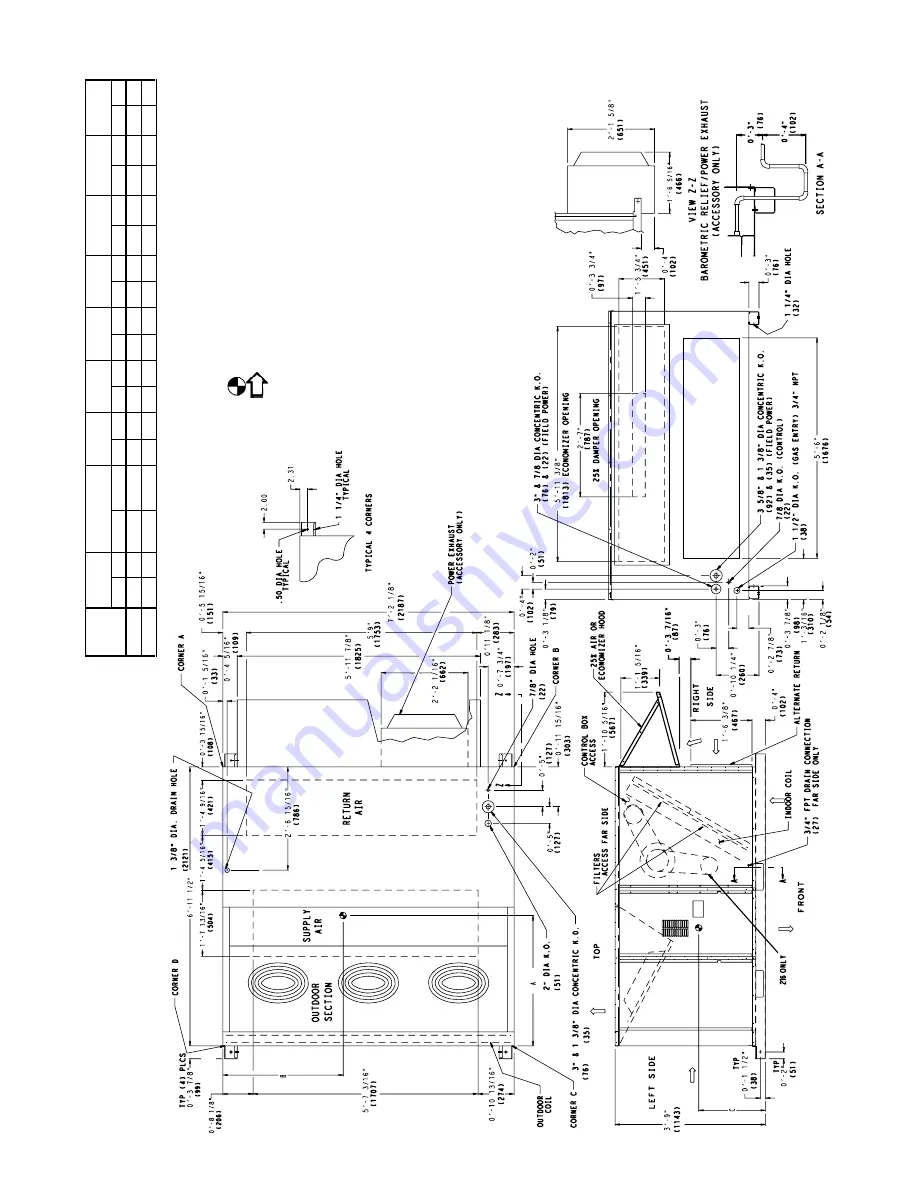
—
5
—
NO
T
E
S:
1.
R
e
fe
r t
o
p
ri
n
t
fo
r ro
of
curb
acc
e
sso
ry
di
m
e
n
s
ions.
2
.
Dim
e
n
sio
n
s in
(
) a
re
in
m
illim
e
te
rs
.
3.
C
e
n
ter
of
Gra
v
it
y.
4.
D
ir
e
ct
ion o
f a
irfl
o
w
.
5.
Ductwor
k
to
be
atta
che
d
to
acce
ssor
y
ro
of c
u
rb
on
ly
.
6.
Mi
ni
mu
m c
le
a
ran
c
e:
•R
e
a
r:
7
′
-0
″
(2
134
) f
o
r
co
il re
mov
a
l.
T
h
is
di
me
nsi
o
n
ca
n be re
duce
d
to
4
′
-0
″
(12
1
9
) i
f c
ond
it
ions
pe
rm
it co
il re
mov
a
l fro
m
t
he
top
.
•4
′
-0
″
(
1
2
19)
to
co
mb
u
s
ti
b
le sur
fa
c
es
,
al
l f
o
ur si
de
s
(i
n
c
lu
d
e
s betw
e
e
n
un
its)
.
•
L
eft
si
de
: 4
′
-0
″
(12
1
9
) f
o
r
pro
per
co
nde
nse
r co
il ai
rf
lo
w
.
•
F
ro
n
t: 4
′
-0
″
(
1
219
) f
o
r con
tr
o
l
bo
x ac
cess
.
•
R
ig
ht s
ide:
4
′
-0
″
(
121
9)
fo
r pr
ope
r o
pera
ti
on
of d
a
mp
er
and
pow
e
r
e
x
hau
st i
f
so e
qui
p
p
e
d
.
•T
o
p
: 6
′
-0
″
(1
829
) t
o
as
sur
e
pr
op
er
cond
en
ser
f
a
n op
erat
ion.
•
B
o
ttom
: 1
4
″
(
356
) t
o
co
mb
u
s
ti
b
le
sur
fac
es (
w
hen
no
t u
s
ing
curb
).
•
C
o
n
tr
ol
b
o
x
si
de:
3
′
-0
″
(91
4
)
to u
ngro
u
n
ded
sur
fa
c
es
, non
-co
m
b
u
sti
b
le
.
•
C
o
n
tr
ol
bo
x
s
id
e
: 3
′
-6
″
(
1
0
6
7
) t
o
b
loc
k
or
c
o
nc
re
te
w
a
lls
, o
r
ot
h
e
r
gro
und
ed sur
face
s
.
•
L
oca
l cod
e
s o
r ju
ri
sdict
ion m
a
y pr
e
v
ail.
7.
W
ith t
he
e
xce
pti
o
n o
f cl
e
a
ran
c
e f
o
r the
co
nde
nse
r co
il an
d th
e d
a
m
p
e
r/
p
o
w
er
e
x
h
a
u
s
t a
s
st
a
ted
i
n
N
o
te
#6
, a r
e
m
o
v
a
b
le
fe
nc
e
or
ba
rri
c
a
de
re
q
u
ire
s
no
cl
ea
ra
nc
e
.
8.
D
im
en
si
on
s a
re
fro
m
o
u
tsi
d
e
of c
o
rn
e
r p
o
st.
A
llo
w
0
′
-
5
/
16
″
(
8
) on eac
h
si
d
e
fo
r t
op c
o
v
e
r dr
ip
ed
ge.
Fig
. 4
— B
ase
U
n
it
D
imen
s
ion
s
; 5
79F
180
,21
6
UNIT
ST
D U
N
IT
WE
IG
HT
E
C
ONOM
I$E
R
IV
WEI
G
HT
CO
RNER
A
CORNER
B
CORNER
C
CO
RNER
D
DIM A
D
IM
B
D
IM
C
lb
kg
lb
kg
lb
k
g
lb
kg
lb
kg
lb
k
g
ft-
in
.
m
m
ft
-in
.
m
m
ft-i
n
.
m
m
579
F1
80
16
50
7
4
8
9
0
4
1
4
2
3
19
2
386
1
7
5
4
03
1
8
3
4
3
8
19
9
3
-5
104
1
3
-5
10
41
1-
10
55
9
579
F2
16
18
00
8
1
6
9
0
4
1
4
3
2
19
6
410
1
8
6
4
61
2
0
9
4
7
2
21
4
3
-3
99
1
3
-7
10
92
1-
8
5
0
8