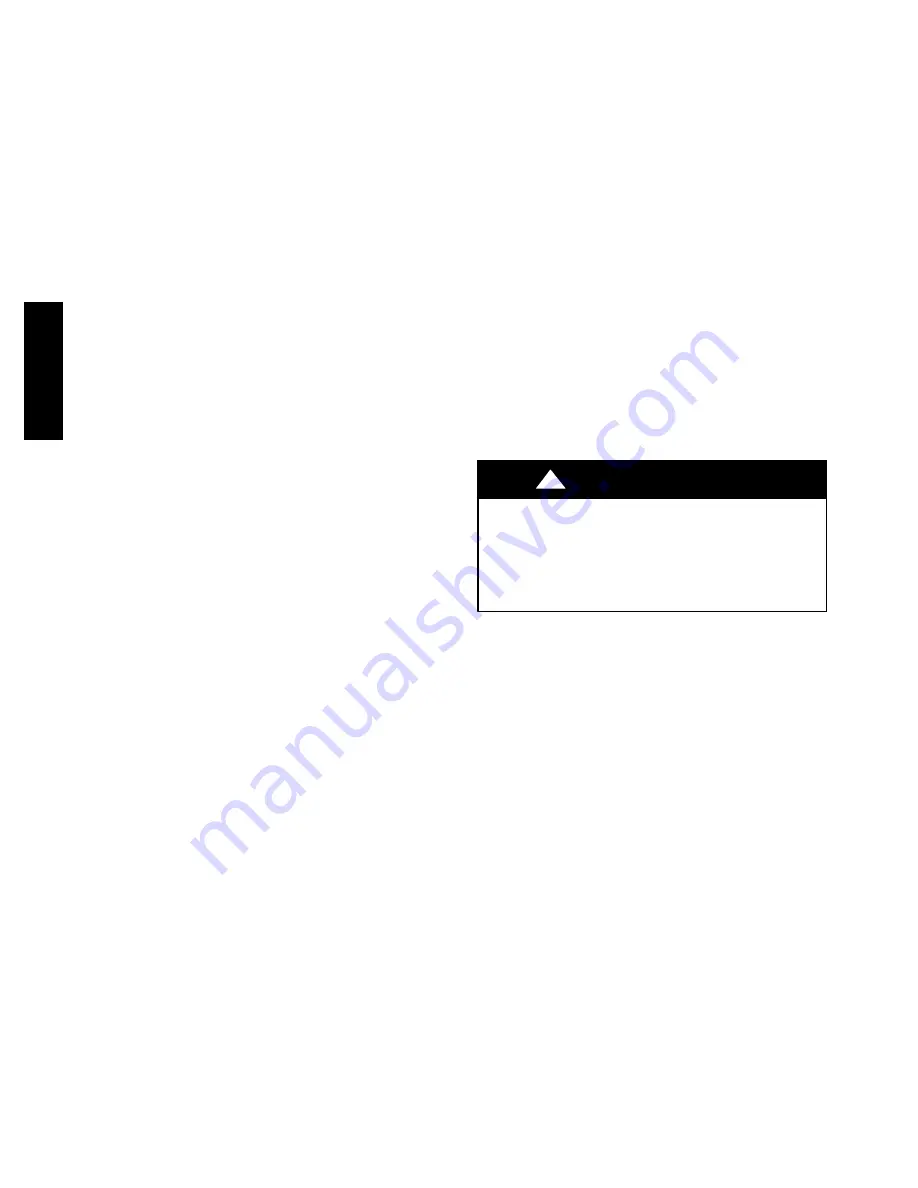
16
d. Make sure that air filter(s) is in place.
e. Make sure that condensate drain trap is filled with water
to ensure proper drainage.
f. Make sure that all tools and miscellaneous loose parts
have been removed.
5. Compressors are internally spring mounted. Do not loosen
or remove compressor holddown bolts.
6. Each unit system has two Schrader--type ports, one
low--side Schrader fitting located on the suction line, and
one high--side Schrader fitting located on the compressor
discharge line. Be sure that caps on the ports are tight.
START--UP
Unit Start--Up and Troubleshooting
NOTE: Always check high-- and low--voltage supply to the unit
components. Check the integrity of the plug receptacle connections
and unit wiring harness prior to assuming a component failure.
A. LED Description
LEDs built into Evolution control boards provide installer or
service person information concerning operation and/or fault
condition of the unit controls and ECM motor. This information is
also available at the system UI in text with basic troubleshooting
instructions. Careful use of information displayed will reduce the
need for extensive manual troubleshooting.
Both the furnace and heat pump (HP)/air conditioner (AC) boards
have an amber LED and a green LED. On the HP/AC board, these
are located near the System Communications connector (ABCD)
(lower right corner of the HP/AC board as installed in the unit).
On the furnace board, these are located at the upper right side,
adjacent to the fuse, above the terminal block. The amber LED is
the System Status LED, labeled STATUS. The green LED, labeled
COMM, is used as an indicator of system communications status
(See Fig. 16 and 19).
Status Codes will be displayed on the STATUS LED using the
following protocol:
1. The number of short flashes indicates first digit of code.
2. The number of long flashes indicates second digit of code.
3. A short flash is 0.25 seconds on. A long flash is 1 second
on.
4. The time between flashes is 0.25 seconds.
5. The time between last short flash and first long flash is 1
second.
6. The LEDs will be off for 2.5 seconds before repeating code.
7. If multiple status codes are active concurrently, the highest
priority status code is displayed.
B. Control
Start--Up
and
System
Communications
Troubleshooting
On power up, green COMM LEDs will be turned off until
successful system communications are established (this should
happen within 10 seconds). Once communications with UI are
successful, both COMM LEDs will be lit and held on. At the same
time, amber STATUS LEDs will be lit and held continuously on
until a request for operating mode is received. The STATUS LED
will be on any time unit is in idle mode.
If, at any time, communications are not successful for a period
exceeding 2 minutes, the Evolution control will only allow
emergency heating or cooling operation using a common
thermostat and the terminal strip connections on the two control
boards (See Non--Communicating Emergency Cooling/Heating
Mode) and will display Status Code 16, System Communication
Fault, on amber STATUS LED. No further troubleshooting
information will be available at UI until communications are
re--established.
If either COMM LED does not light within proper time period and
status codes are not displayed;
1. Check system transformer high-- and low--voltage to be sure
the system is powered.
2. Check ABCD connection on both boards.
3. Check fuse on furnace board to be sure it is not blown. If
fuse is open, check system wiring before replacing it to be
sure a short does not cause a failure of replacement fuse.
If COMM LED does not light within proper time period and status
code is displayed:
1. Check system wiring to be sure UI is powered and
connections are made A to A, B to B, etc. and wiring is not
shorted.
Mis--wiring
or
shorting
of
the
ABCD
communications wiring
will not allow successful
communications.
NOTE
: Shorting or mis--wiring low--voltage system wiring will
not cause damage to unit control or UI but may cause low voltage
fuse to open.
C. Indoor Fan Motor Troubleshooting
The indoor fan is driven by an ECM motor consisting of two
parts: the control module and the motor winding section. Do not
assume motor or module is defective if it will not start. Use the
designed--in LED information aids and follow troubleshooting
steps described below before replacing motor control module or
entire motor. Motor control module is available as a replacement
part.
VERIFY MOTOR WINDING SECTION
ELECTRICAL SHOCK HAZARD
Failure to follow this warning could result in personal
injury or death.
After disconnecting power from the ECM motor, wait at
least 5 minutes before removing the control section. Internal
capacitors require time to discharge.
!
WARNING
Before proceeding to replace a motor control module:
1. Check motor winding section to be sure it is functional.
2. Remove motor control module section and unplug winding
plug. Motor shaft should turn freely, resistance between any
two motor leads should be similar and resistance between
any motor lead and unpainted motor end should exceed
100,000 ohms.
3. Failing any of these tests, entire ECM motor must be
replaced.
4. Passing all of the tests, motor control module alone can be
replaced.
MOTOR TURNS SLOWLY
1. Low static pressure loading of blower while access panel is
removed will cause blower to run slowly. Particularly at low
airflow requests. This is normal, do not assume a fault
exists.
2. Recheck airflow and system static pressure using UI service
screens with access panel in place.
NOTE
: Blower motor faults will not cause a lockout of blower
operation. The fan coil control will attempt to run the blower motor
as long as UI maintains a demand for airflow. The control will not
operate electric heaters while a fault condition exists. The control
communicates with the motor at least once every five seconds,
even when the motor is idle. If, during operation, the control does
not communicate with the motor for more than 25 seconds, the
motor will shut itself down and wait for communications to be
reestablished.
D. Furnace Control Troubleshooting
Furnace control faults indicated by flashing codes on the amber
system STATUS LED can be resolved using troubleshooting
677D
--
--
A