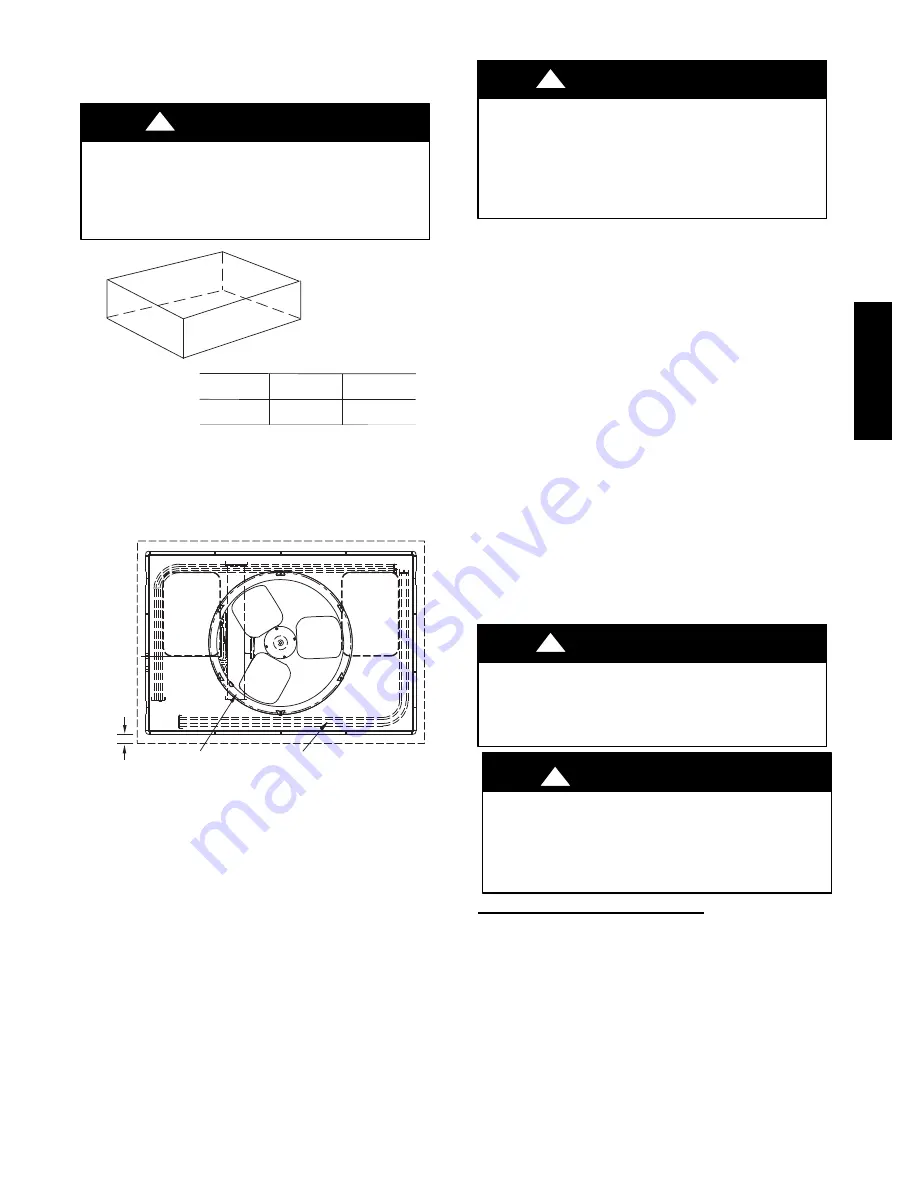
3
spacer blocks (for easy alignment to existing curb) and
gaskets for the perimeter seal and duct openings. This kit is
used when existing curb is modified by removing outer
horizontal flange.
CAUTION
!
UNIT/STRUCTURAL DAMAGE HAZARD
Failure to follow this caution may result in property damage.
Ensure there is sufficient clearance for saw blade when cutting
the outer horizontal flange of the roof curb so there is no
damage to the roof or flashing.
A
B
C
MAXIMUM ALLOWABLE
DIFFERENCE in. (mm)
A-C
1/4
1/4
1/4
(6.35)
(6.35)
(6.35)
A-B
B-C
A07925
Fig. 2 -- Unit Leveling Tolerances
SLAB MOUNT
Place the unit on a solid, level pad that is at least 2 in. (51 mm)
above grade. The pad should extend approximately 2 in. beyond
the casing on all 4 sides of the unit (See Fig. 3). Do not secure the
unit to the pad
except
when required by local codes.
OPTIONAL
RETURN
AIR
OPENING
OPTIONAL
SUPPLY
AIR
OPENING
EVAP. COIL
COND. COIL
2˝
(50.8mm)
A07926
Fig. 3 -- Slab Mounting Detail
Provide Clearances
The required minimum service clearances are shown in Fig. 5 and
6. Adequate ventilation and outdoor air must be provided. The
outdoor fan draws air through the outdoor coil and discharges it
through the top fan grille. Be sure that the fan discharge does not
recirculate to the outdoor coil. Do not locate the unit in either a
corner or under an overhead obstruction. The minimum clearance
under a partial overhang (such as a normal house overhang) is 48
in. above the unit top. The maximum horizontal extension of a
partial overhang must not exceed 48 in. (1219 mm).
IMPORTANT
: Do not restrict outdoor airflow. An air restriction
at either the outdoor--air inlet or the fan discharge may be
detrimental to compressor life.
Do not place the unit where water, ice, or snow from an overhang
or roof will damage or flood the unit. Do not install the unit on
carpeting or other combustible materials. Slab--mounted units
should be at least 2 in. (51 mm) above the highest expected water
and runoff levels. Do not use unit if it has been under water.
Rig and Place Unit
PERSONAL INJURY OR PROPERTY DAMAGE
HAZARD
Failure to follow this warning could result in personal
injury, death or property damage.
When installing the unit on a rooftop, be sure the roof will
support the additional weight.
!
WARNING
Rigging and handling of this equipment can be hazardous for
many reasons due to the installation location (roofs, elevated
structures, etc.).
Only trained, qualified crane operators and ground support staff
should handle and install this equipment.
When working with this equipment, observe precautions in the
literature, on tags, stickers, and labels attached to the equipment,
and any other safety precautions that might apply.
Training for operators of the lifting equipment should include, but
not be limited to, the following:
1. Application of the lifter to the load, and adjustment of the
lifts to adapt to various sizes or kinds of loads.
2. Instruction in any special operation or precaution.
3. Condition of the load as it relates to operation of the lifting
kit, such as balance, temperature, etc.
Follow all applicable safety codes. Wear safety shoes and work
gloves.
INSPECTION
Prior to initial use, and at monthly intervals, all rigging shackles,
clevis pins, and straps should be visually inspected for any damage,
evidence of wear, structural deformation, or cracks. Particular
attention should be paid to excessive wear at hoist hooking points
and load support areas. Materials showing any kind of wear in
these areas must not be used and should be discarded.
UNIT FALLING HAZARD
Failure to follow this warning could result in personal
injury or death.
Never stand beneath rigged units or lift over people.
!
WARNING
PROPERTY DAMAGE HAZARD
Failure to follow this warning could result in personal
injury/death or property damage.
When straps are taut, the clevis should be a minimum of 36
in. (914 mm) above the unit top cover.
!
WARNING
Rigging/Lifting of Unit (See Fig. 7)
Lifting holes are provided in base rails as shown in Fig. 5 and 6.
1. Leave top shipping skid on the unit for use as a spreader bar
to prevent the rigging straps from damaging the unit. If the
skid is not available, use a spreader bar of sufficient length
to protect the unit from damage.
2. Attach shackles, clevis pins, and straps to the base rails of
the unit. Be sure materials are rated to hold the weight of the
unit (See Fig. 7).
3. Attach a clevis of sufficient strength in the middle of the
straps. Adjust the clevis location to ensure unit is lifted level
with the ground.
After the unit is placed on the roof curb or mounting pad, remove
the top skid.
677D
--
--
A