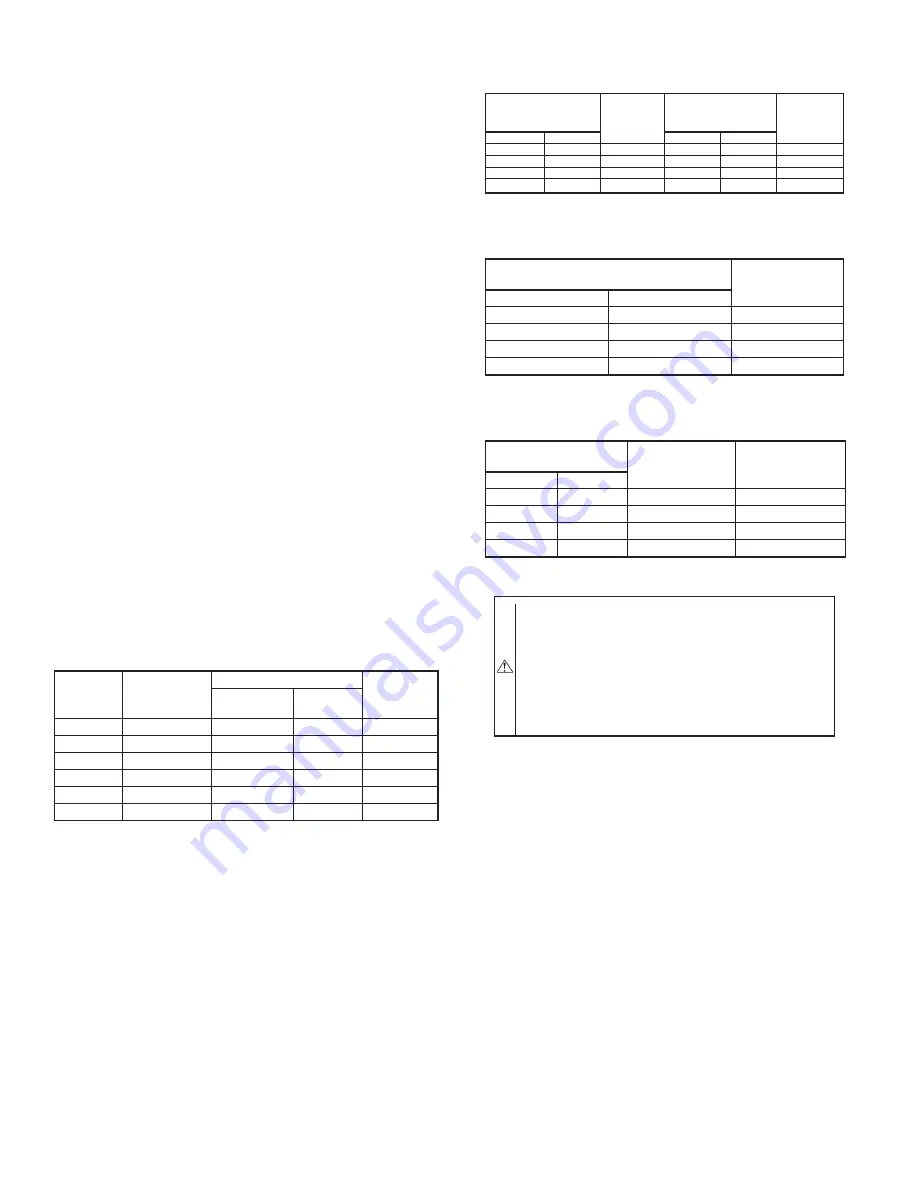
b. A lack of flue draft (chimney effect) or some other
blockage, such as soot, in secondary section of heat
exchanger.
c. Use of an oversized nozzle input.
d. Pump pressure over the values listed in Table 10.
5. The CO
2
and stack temperature instruments enable you to
obtain data required to determine thermal efficiency of
furnace.
6. An oil filter should be installed as close to burner as
possible with ALL oil burners and is essential on lower
firing rate burners. We recommend the use of a low
pressure drop oil filter such as the General Filter, Inc. model
#1A-25A or equivalent.
7. The oil pressure regulator is factory set to give oil pressure
of 135 psig for the model having 105,000 BTUH input and
135 psig for the model having 119,000 BTUH input. The
firing rate noted on nameplate may be obtained using the
nozzles and pump pressures indicated in Table 10. The
proper oil burner turbulator setting for all the firing rates is
0 (zero).
8. On a new installation, air entrapped in oil line leading from
tank to nozzle must be thoroughly purged in order to
prevent excessive after drip. The oil pump is provided with
a special fitting which allows purging of any air between
tank and oil pump. The proper procedure for performing
this operation is as follows:
a. Place a piece of clear plastic 1/4-in. diameter tubing over
purge fitting on oil pump.
b. Start oil burner, then open purge fitting and allow burner
to run until purge tube is completely free of air bubbles.
c. Tighten purge fitting. Allow oil to run to nozzle and fire
burner.
d. If purging takes longer than 15 sec and no flame has
been established, burner stops. Push reset button on front
of primary control to restart burner.
e. For detailed information on operation of primary control,
refer to instructions included with furnace.
After all the setup procedures mentioned above have been com-
pleted, the burner should be allowed to operate and an inspection
mirror should be used to observe the flame pattern at tip of nozzle.
Any irregularities such as burning to 1 side or pulsating flame
patterns should be corrected by changing nozzle.
III.
FAN ADJUSTMENT CHECK
This furnace is equipped with a variable speed motor to deliver a
constant airflow. Adjust DIP switches on the electronic board
ACCORDING TO OIL INPUT SELECTED AND A/C SIZE. (See
Tables 11A, 11B, and 11C or Tables 12A, 12B, and 12C.)
WARNING:
FIRE HAZARD AND UNIT
RELIABILITY
Failure to follow this warning could result in property
damage, personal injury or death.
When operating furnace in heating mode, static pressure
and temperature rise (supply-air temperature minus
return-air temperature) must be within those limits speci-
fied on rating label.
IV.
LIMIT CONTROL CHECK
After furnace has been in operation for at least 15 minutes, restrict
return-air supply by blocking filters or closing return registers and
allow furnace to shut down on high limit. The burner should shut
off, and main blower should continue to run.
V.
FOR YEAR-ROUND AIR CONDITIONING
This furnace is designed for use in conjunction with cooling
equipment to provide year-round air conditioning. The blower has
been sized for both heating and cooling, however, fan motor speed
may need to be changed to obtain necessary cooling airflow.
VI.
HEATING
The blower speed is factory set to deliver required airflow at
normal duct static pressure for 0.75 GAL/HR (US) INPUT for the
368RAN 105 size (See Tables 11A, 11B, and 11C) and 0.85
GAL/HR (US) INPUT for the 368RAN 120 size. (See Tables 12A,
12B, and 12C.) The blower motor may be field adjusted to deliver
required airflow for other capacity.
VII.
COOLING
The blower speed may be field adjusted to deliver required airflow
for cooling application. (See Table 13 or 14.)
TABLE 10—BURNER INPUT AND NOZZLE SIZE
FURNACE
INPUT
(BTUH)
FIRING
RATE
GAL/HR (US)*
RIELLO OIL BURNER
PUMP
PRESSURE
(PSIG)
No. 40 Series
Model
Nozzle
70,000
0.50
F3
0.40 - 70A
160
91,000
0.65
F3
0.50 - 70W
170
105,000
0.75
F3
0.65 - 70W
135
119,000
0.85
F5
0.75 - 70B
130
140,000
1.00
F5
0.85 - 70W
140
154,000
1.10
F5
1.00 - 70W
125
*For rating purposes only
TABLE 11A— 368RAN 105 SIZE DIP SWITCH
ADJUSTMENT FOR OIL HEATING MODE
SW1-HEAT
DIP SWITCH
POSITION
INPUT
USGPH
SW4-DELAY
DIP SWITCH
POSITION
INPUT
USGPH
1
2
1
2
OFF
OFF
0.75
OFF
OFF
0.75
ON
OFF
0.65
ON
OFF
0.65
OFF
ON
0.5
OFF
ON
0.5
ON
ON
N/A
ON
ON
N/A
TABLE 11B— 368RAN 105 SIZE DIP SWITCH
ADJUSTMENT FOR HEAT PUMP AND COOLING MODE
SW2-COOL
DIP SWITCH POSITION
A/C SIZE
(TONS)
1
2
OFF
OFF
3.0
ON
OFF
2.5
OFF
ON
2.0
ON
ON
1.5
TABLE 11C— 368RAN 105 SIZE DIP SWITCH
CFM ADJUSTMENTS IN ALL MODES
SW2-ADJUST
DIP SWITCH POSITION
HEATING CFM %
INCREASE OR
DECREASE
COOLING CFM %
INCREASE OR
DECREASE
1
2
OFF
OFF
0
0
ON
OFF
+ 13
+ 10
OFF
ON
- 15
- 10
ON
ON
N/A
0
—10—