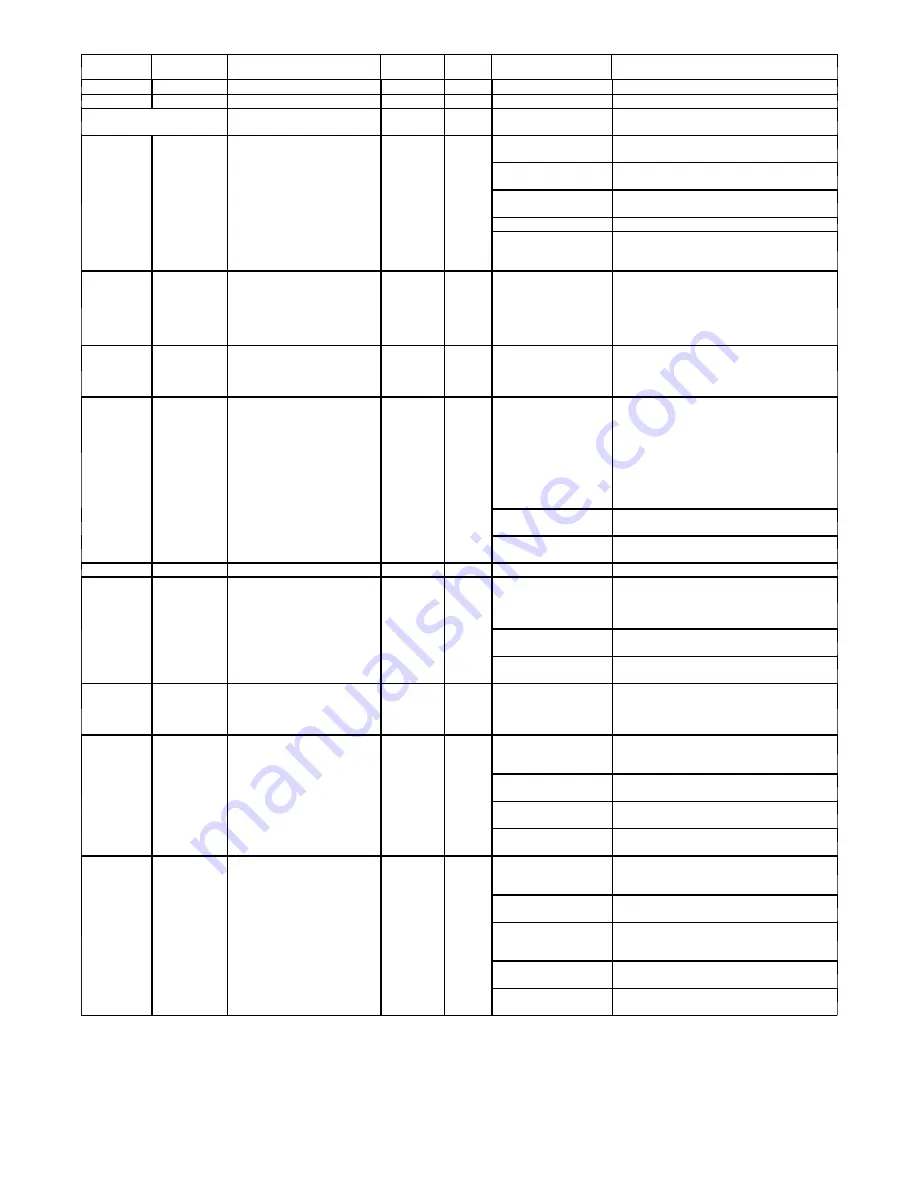
18
Table 6—Fault Code Actions
Flash
Code
Type
Amber LED Description
Reset
Time
Mode
Possible Causes
Actions
ON, no flash
Standby
1, pause
Variable Capacity
1 (2 sec ON), longer pause
(1 second OFF)
Variable Capacity
(Range Cutback)
25
System Mal-
function
INVALID MODEL
PLUG/INVERTER SIZE
NA
Both
Wrong Model Plug In-
stalled
Verify correct model plug installed
Damaged Model Plug
Check model plug for corrosion or breakage;
replace if necessary
Missing model plug on
service board
Re-install original model plug
Damaged AOC control
Replace AOC control
Incorrect Model Plug
with Inverter Size
Replace plug or inverter with correct size (If
model plug is for 2 Ton but Inverter is 3 Ton,
fault code 25 will be shown)
31
Local
HIGH PRESSURE SWITCH
OPEN
(stage/speed down for each
occurrence, elevates to fault
code 84 when it occurs while
running on the lowest stage)
6 Minutes
(then re-
duced
stage oper-
ation)
Both
High Pressure Event
System will self-mitigate by reducing the stage,
persistent conditions will lead to lockout (refer
to Error Code 84). 2 hours of accumulated
operation without further fault will reset fault
reduced stage operation.
32
Local
LOW PRESSURE TRIP
(elevates to fault code 83 after
3 occurrences)
6 Minutes
Both
Low Pressure Event
System will self-mitigate, persistent conditions
will lead to lockout (refer to Error Code 83) 2
hours of accumulated operation without further
fault will reset fault counter
33
Local
LOST INVERTER COMMUNI-
CATIONS
(Occurs aftr 2 minutes of no
communications between AOC
and MOC)
(Elevates to fault code 48 after
3 consecutive failures within 20
minute or 20 minutes continu-
ous loss of connection)
NA
Both
Loose or disconnected
harness (Hardness be-
tween AOC (PL20) and
MOC)
Verify good harness connection
Radio or Electrical noise
System will try to self-mitigate with repeated
start attempts
Possible damage to in-
verter
change out the Inverter drive
46
Local
BROWNOUT EVENT
6 Minutes
Both
low line voltages
if persistent contact power provider
48
System
Malfunction
LOST INVERTER COMMUNI-
CATIONS
(Elevated from fault code 33 af-
ter 3 occurrences)
NA
Both
Loose or disconnected
harness (Hardness be-
tween AOC (PL20) and
MOC)
Verify good harness connection
Radio or Electrical noise
System will try to self-mitigate with repeated
start attempts
Possible damage to in-
verter
change out the Inverter drive
49
Local
COMPRESSOR OVER CUR-
RENT FAULT
(Elevates to fault code 95 after
5 occurrences)
6 Minutes
Both
Refer to fault code 95
Refer to fault code 95
53
Fault
OUTDOOR AIR TEMP
SENSOR FAULT
NA
Both
Sensor Harness not
connected to AOC con-
trol
Ensure plug is connected to AOC control
Broken or loose har-
ness wire
Check harness for continuity; see resistance
chart to check resistance at given temperature
Broken or Damaged
Sensor
Check harness for continuity; see resistance
chart to check resistance at given temperature
Hardware damage to
AOC control
Replace AOC control
54
Fault
SUCTION TEMP SENSOR
FAULT
NA
Both
Sensor Harness not
connected to AOC
control
Ensure plug is connected to AOC control
Broken or loose
harness wire
Check harness for continuity; see resistance
chart to check resistance at given temperature
Suction Thermistor not
properly attached or in
wrong location
Ensure Sensor is properly attached to the ac-
cumulator entry-tube
Broken or Damaged
Sensor
Check harness for continuity; see resistance
chart to check resistance at given temperature
Hardware damage to
AOC control
Replace AOC control
Summary of Contents for 189BNV EVOLUTION
Page 17: ...17 Fig 38 Fault Code Label ...