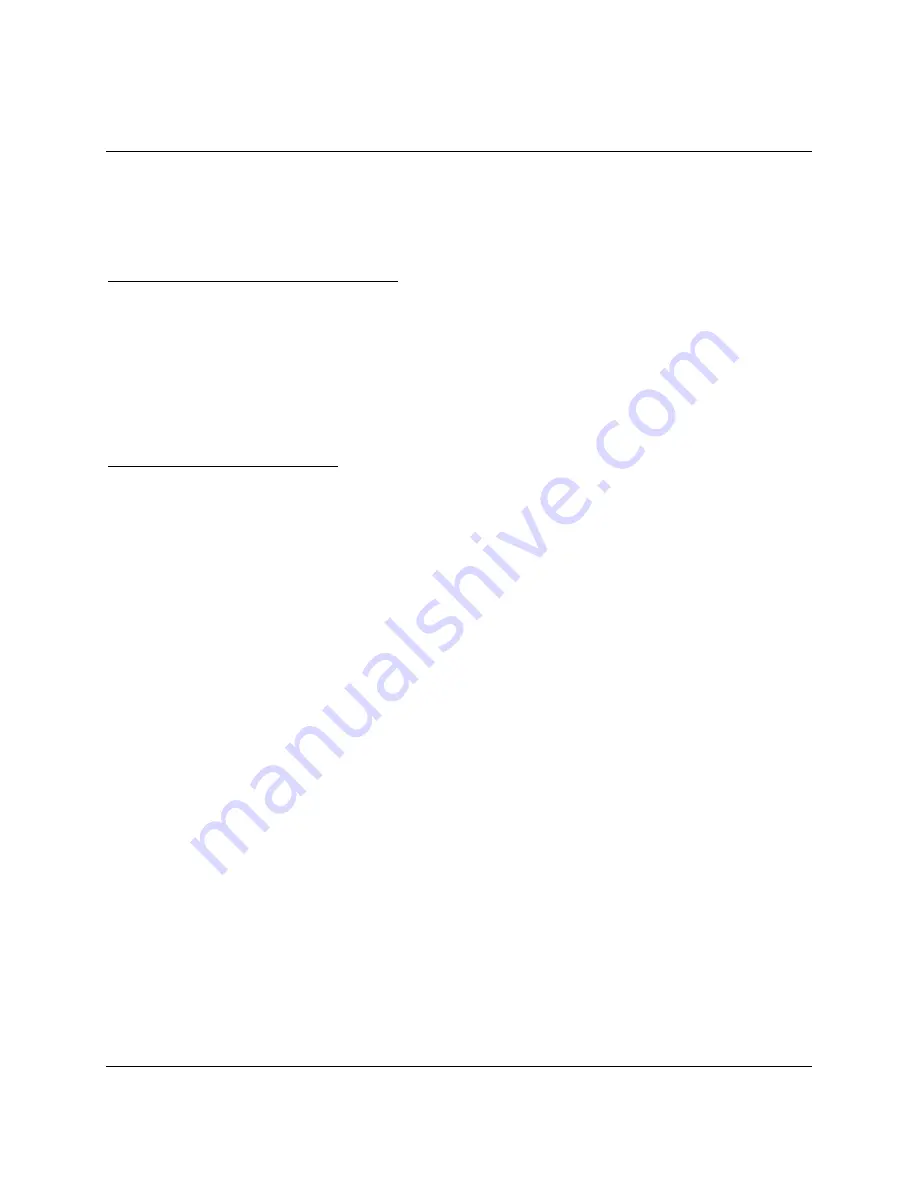
Form 2055
18
Revision Date 5/1/2015
3 . 9 . 7 W E T L A Y - U P O F S T E A M B O I L E R S -
S H O R T T E R M
In the wet lay-up procedure, the boiler is to be filled with chemically treated water and sealed to
prevent air in-leakage. Nitrogen gas under slight pressure can also be used to displace air and
protect the boiler surfaces from corrosion. The following steps should be taken for wet lay-up of a
boiler:
1a.
Procedure for Operational Boiler:
At least thirty minutes before the boiler comes off line, add the following chemicals:
Sodium Sulfite – 0.5 lbs per 100 gallons water
Polymeric Sludge Dispersant – 0.1 lbs per 100 gallons water
Caustic Soda – 0.3 lbs per 100 gallons water
1b.
Procedure for idle boiler:
if the boiler has never been on line or has been out of service for cleaning, select the highest
quality water available to fill the boiler. Steam condensate, softened water, filtered fresh water,
and boiler feedwater are generally acceptable for lay-up. Raw city water is not recommended and
should not be used.
Prepare the chemical solution described in (1a) in a separate tank. Adhere to the safety
precautions described in Section 3.2 of this manual. Add the concentrated lay-up solution to the
boiler during the time it is being filled.
After the boiler is filled and the lay-up solution has been added, the boiler is to be operated for
thirty minutes at low fire to circulate and mix the chemicals.
After filling, the boiler must be closed or blanketed tightly. The power supply to the boiler must be
cut off. Vent all air from the top of the boiler to allow complete fill with the required solution.
Nitrogen gas at 5 psig may be introduced though a suitable opening to prevent air in-leakage
during the lay-up period. An alternative to the nitrogen gas (see safety precautions under dry lay-
up) is to install a 55 gallon drum or auxiliary vessel as shown in Figure 3.9A. This is to be fitted
with a cover and filled with properly treated water. This vessel or drum should be connected to an
available opening in the top of the vessel. Its purpose is to create a hydrostatic head and to allow
a ready visual check of water level loss or in-leakage during the lay-up period.
During lay-up, test the boiler weekly to assure the proper levels of sulfite and alkalinity. To do this,
take a sample of the boiler water from the surface blowdown line or other high point. The test
results should be:
Sodium Sulfite 200 ppm minimum
Phenolphthalein Alkalinity (as CaCO3) 400 ppm minimum