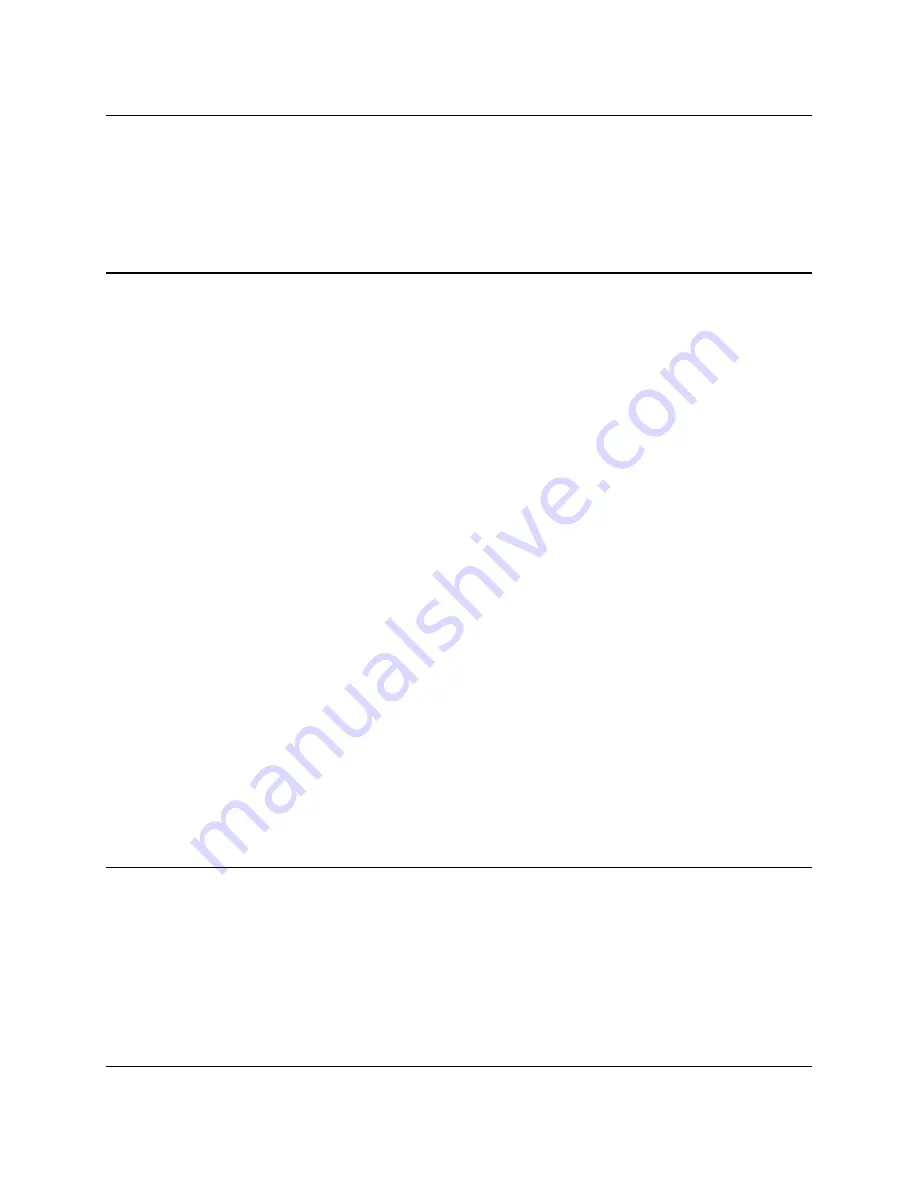
Form 2055
15
Revision Date 5/1/2015
3 . 6 . 3 M O N T H L Y
Make visual inspection of all wiring and components.
Check float low water cutoff as described above.
3 . 6 . 4 A N N U A L L Y
Check operating control, high limit and other electrical components for proper operating
procedures as specified in manufacturer’s instructions.
The elements in the boiler should be removed at least yearly for proper visual inspection. If
elements need to be replaced, they should be replaced or the element bundle sent to the
factory for service at this time.
The boiler pressure vessel and piping should be checked annually.
3.7 FLOAT-ACTUATED WATER LEVEL CONTROLS
Inspect float type water level controls for proper operation. Visually inspect sight glasses for
evidence of scale forming residues. Refer to section 3.8 for gauge glass maintenance.
On closed steam heating systems, the float low water cutoff should be blown down by means of
opening a blowdown valve on the lower connection of the cutoff once per day.
On humidification or process systems, the blowdown schedule should be based on
recommendation from a water treatment and maintenance program specifically designed for the
boiler.
At the annual inspection, all float type level controls should be disassembled, cleaned and
inspected thoroughly. When re0installed these controls must be give an operational test.
3.8 WATER GAUGE GLASSES
3 . 8 . 1 I N S T A L L A T I O N
Check with the maintenance supervisor and engineer for the proper glass to be used. Compare
the box and the glass label or marking to ascertain that the gauge glass ratings or temperature
and pressure suitable for use on the boiler. Use new gaskets when replacing glass. The gaskets
used should be the same type as those originally supplied with the boiler. Make certain that the
gauge glass valves are properly aligned.
All bolts and nuts must be free running and well lubricated, preferably with a graphite type
lubricant. Washers under nuts and bolt heads are desirable. DO NOT tighten while equipment is
in operation.