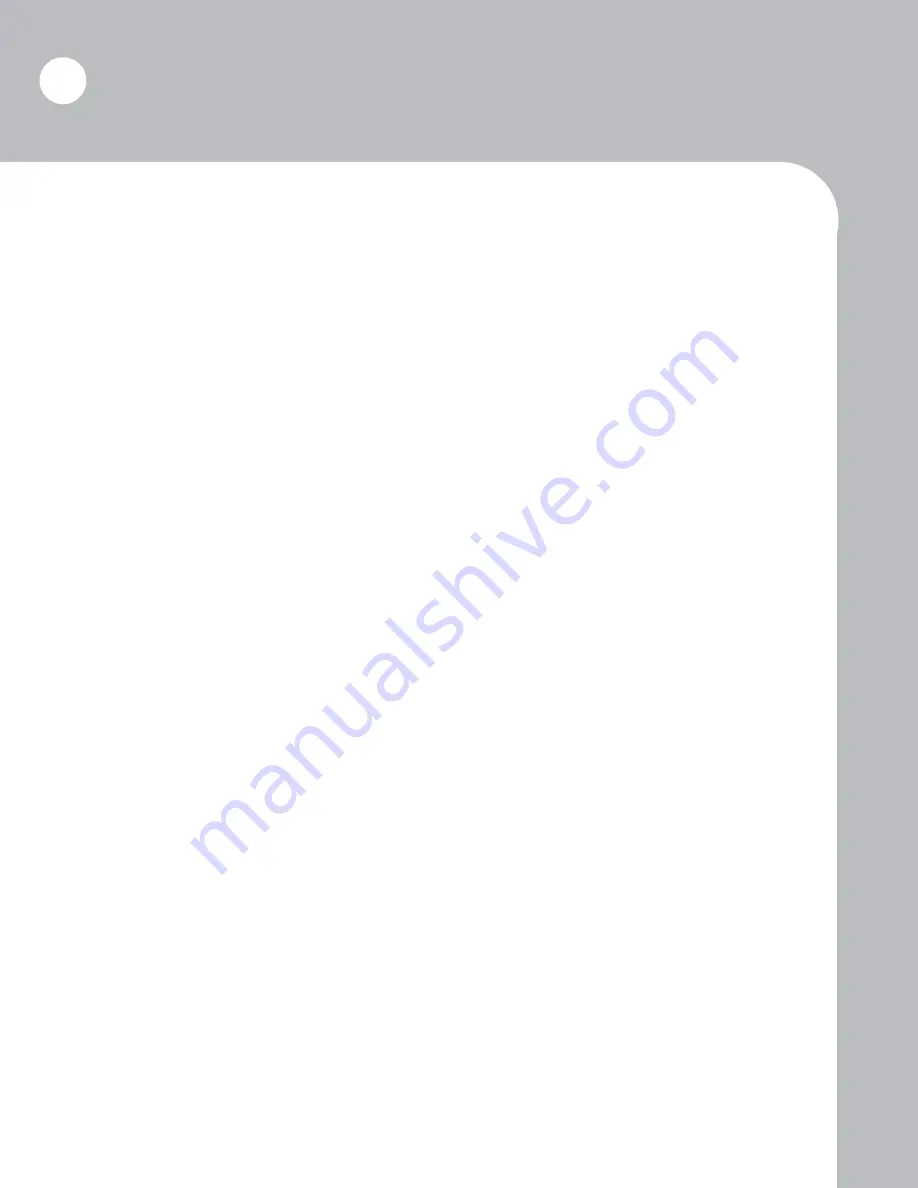
Warranty Statement
LIMITED WARRANTY
BROWN MANUFACTURING CORP. hereby warrants that Brown’s products will be free from defects in
material and workmanship under normal use according to the provisions and limitations herein set forth. All
parts, specifically EXCLUDING expendable ‘wear’ parts, that become unserviceable, due to defective material or
workmanship, within three months / 90 days from date of the original retail purchase, shall, at Brown’s option, be
repaired or replaced.
LIMITATIONS
The obligations of Brown for breach of warranty shall be limited to products manufactured by Brown; (1) that are
installed, operated, and maintained according to Brown’s instruction furnished and/or available to the purchaser
upon request; (2) that are installed according to all other applicable Federal, State, and local codes or regulations;
and (3) that the purchaser substantiates were defective in material and workmanship notwithstanding that they
were properly installed and correctly maintained as set forth and were not abused or misused. The obligation of
Brown shall be limited to replacing or repairing the detective product, at the option of Brown. Brown shall not
be responsible for any labor or cost of removal or repairing or reinstallation of its products and shall not be liable
for transportation costs to and from its plant in Ozark, Alabama. Use of parts for modification or repair of the
product or any component part thereof not authorized or manufactured by Brown specifically for such product
shall void this warranty. This warranty shall not apply to any damage to or defect in the Brown’s products that is
directly or indirectly caused by; (1) FORCE MAJEURE, act of GOD, or other accident not related to an inherent
product defect; or (2) abuse, misuse, or neglect of the such product, including any damage caused by improper
assembly, installation, adjustment, or faulty instruction of the purchaser.
OTHER THAN AS ExpRESSly
SET FORTH HEREINABOvE, BROWN MAkES NO OTHER WARRANTy, ExpRESS OR IMplIED,
WITH RESpECT TO ANy OF BROWN’S pRODUCTS, INClUDED BUT NOT lIMITED TO ANy
MERCHANTABIlITy OR FITNESS FOR A pARTICUlAR pURpOSE. IN NO EvENT SHAll BROWN
BE RESpONSIBlE FOR ANy INCIDENTAl OR CONSEqUENTIAl DAMAgES OF ANy NATURE
SUFFERED By pURCHASER OR ANy OTHER pERSON OR ENTITy CAUSED IN WHOlE OR IN
pART By ANy OF BROWN’S pRODUCTS
. Any person or entity to whom this warranty extends and who
claims breach of warranty against Brown must bring suit thereon within one year from the date of occurrence of
such breach of warranty or be forever barred from any and all legal or other remedies for such breach of warranty.
Brown is not responsible for and hereby disclaims any undertaking, representation, or warranty made by any
dealer, distributor, or other person that is inconsistent with or in any way more expensive than the provisions of
this limited warranty. This warranty grants specific legal rights and shall be read in conformity with applicable
state law. In some jurisdictions, the applicable law mandates warranty provisions that provide greater rights than
those provided for herein. In such case, this limited warranty shall be read to include such mandates provisions;
and any provision herein that is prohibited or unenforceable in any such jurisdiction shall, as to such jurisdiction,
be ineffective to the extent of such prohibition or unenforceable without invalidating the remaining provisions and
without affecting the validity or enforceability of such provisions in any other jurisdiction.
STATEMENT OF POLICY
In accordance with our established policy of constant improvement, we reserve the right to amend these
specifications at any time without notice.
WARRANTY BY MANUFACTURER
Dealer/distributor understands and agrees that the manufacturer extends only the following warranty to its
customers. In the event dealer/distributor extends any additional warranty such as enlarging the scope or period
of warranty or undertaking a warranty of fitness for any particular purpose or obligation not encompassed in
manufacturer’s warranty, dealer/distributor shall be solely responsible therefore and shall have no recourse against
manufacturer with respect thereto.
4
Summary of Contents for 2000 Series
Page 19: ...19 Assembly Standard Assembly continued B D E F G H A ...
Page 23: ...23 Notes ...
Page 33: ...33 Notes ...
Page 43: ...43 Maintenance Date Function Part s Involved Initials Maintenance Repair Log continued ...
Page 46: ...Deck Assembly All Models Replacement Parts 46 Cylinders shown for clarity ...
Page 48: ...Replacement Parts 48 145 HP Gearbox ...
Page 54: ...Replacement Parts 54 Tailwheel Assembly All Models ...
Page 58: ...58 ...
Page 59: ...59 Thank You for purchasing a Brown Tree Cutter ...
Page 60: ...Version 6 0 3 April 2012 Brown Tree Cutters From Serial Number C 0 0 0 1 ...