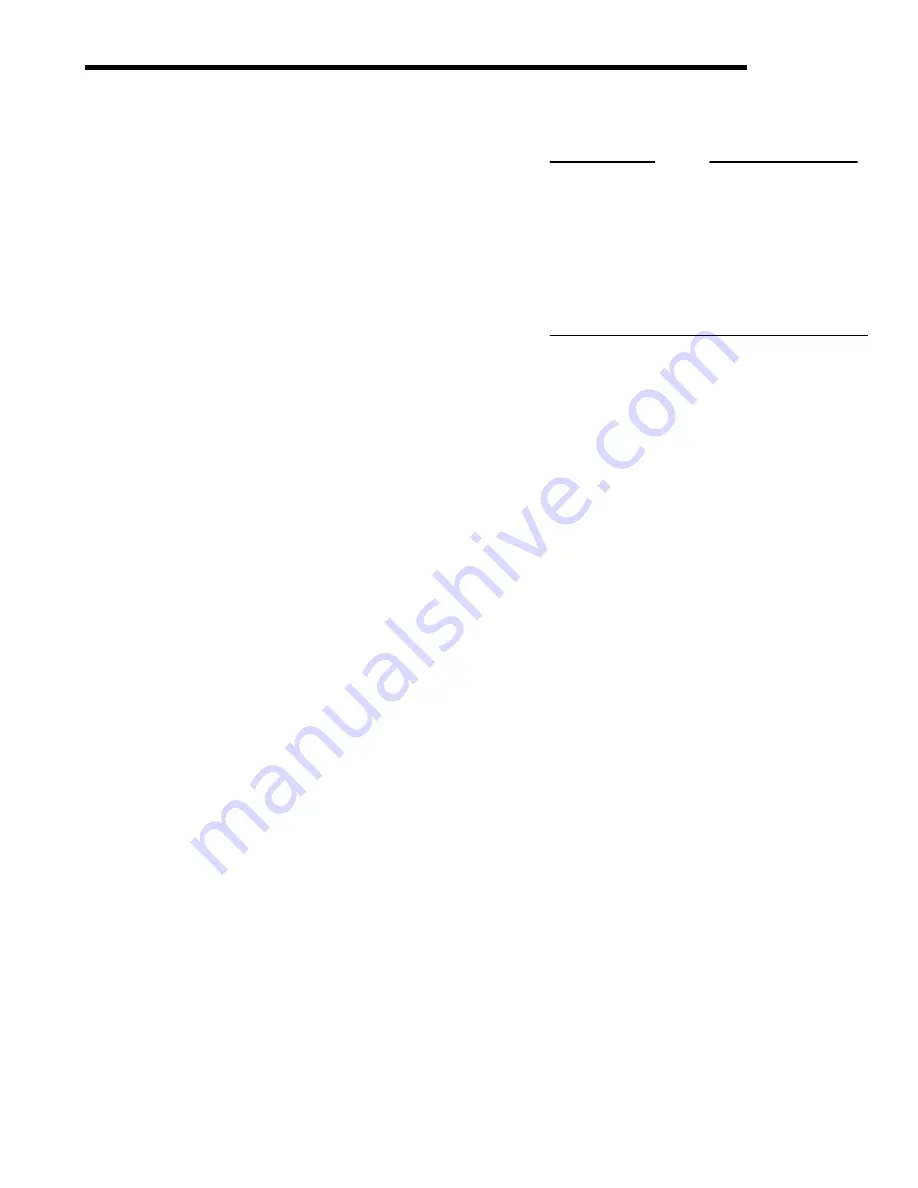
Transporting and Storage Safety
A disabled harvester is best transported on a flatbed
carrier. Use chains to secure the harvester to the carrier.
Never tow a harvester at a speed greater than 16 km/h
(10 mph). An operator must steer and brake the
harvester under tow.
Stop the engine and allow to cool before storing.
Drain the fuel tank outdoors only.
Shut off fuel while storing or transporting.
Store fuel in an approved container in a cool, dry place.
Keep the machine and fuel containers in a locked
storage place to prevent tampering and to keep children
from playing with them.
Do not store the machine or fuel container near heating
appliances with an open flame such as a water heater or
an appliance with a pilot light.
Service Harvester Safely
Do not service the harvester while it is in motion or while
the engine is running.
When servicing front-wheel-drive equipped harvester,
with rear wheels supported off the ground, and rotating
the wheels by engine power, always support the front
wheels in a similar manner. Engaging front-wheel drive
will pull the rear wheels off their support if front wheels
are not raised.
Tighten wheel hardware to correct torque as specified in
wheels, tires and treads section.
Torque at intervals shown in break-in period and
lubrication and maintenance sections, to ensure that the
wheel hardware does not loosen.
Reinstall shields removed during service.
SAFETY
NOTE
Refer to pages 2-09 and 2-10 for:
•
Tire service.
•
Handling chemical products.
•
Disposal of waste products.
•
Removal of paint before welding.
•
Avoidance of heating pressurized fluid lines.
2-08
Summary of Contents for 1570
Page 2: ......
Page 4: ......
Page 5: ...1570 1576 SOD HARVESTERS SECTION 1 INTRODUCTION Descriptions 1 01 Specifications 1 02 ...
Page 8: ......
Page 9: ...1570 1576 SOD HARVESTERS SECTION 2 SAFETY General Safety 2 01 2 10 Safety Decals 2 11 2 12 ...
Page 20: ......
Page 21: ......
Page 22: ......
Page 36: ......
Page 57: ...Cylinder Lock Lubrication SERVICE Auto Steer Lubrication 5 02 Cutter Head Lubrication Points ...
Page 58: ...SERVICE 5 03 ...