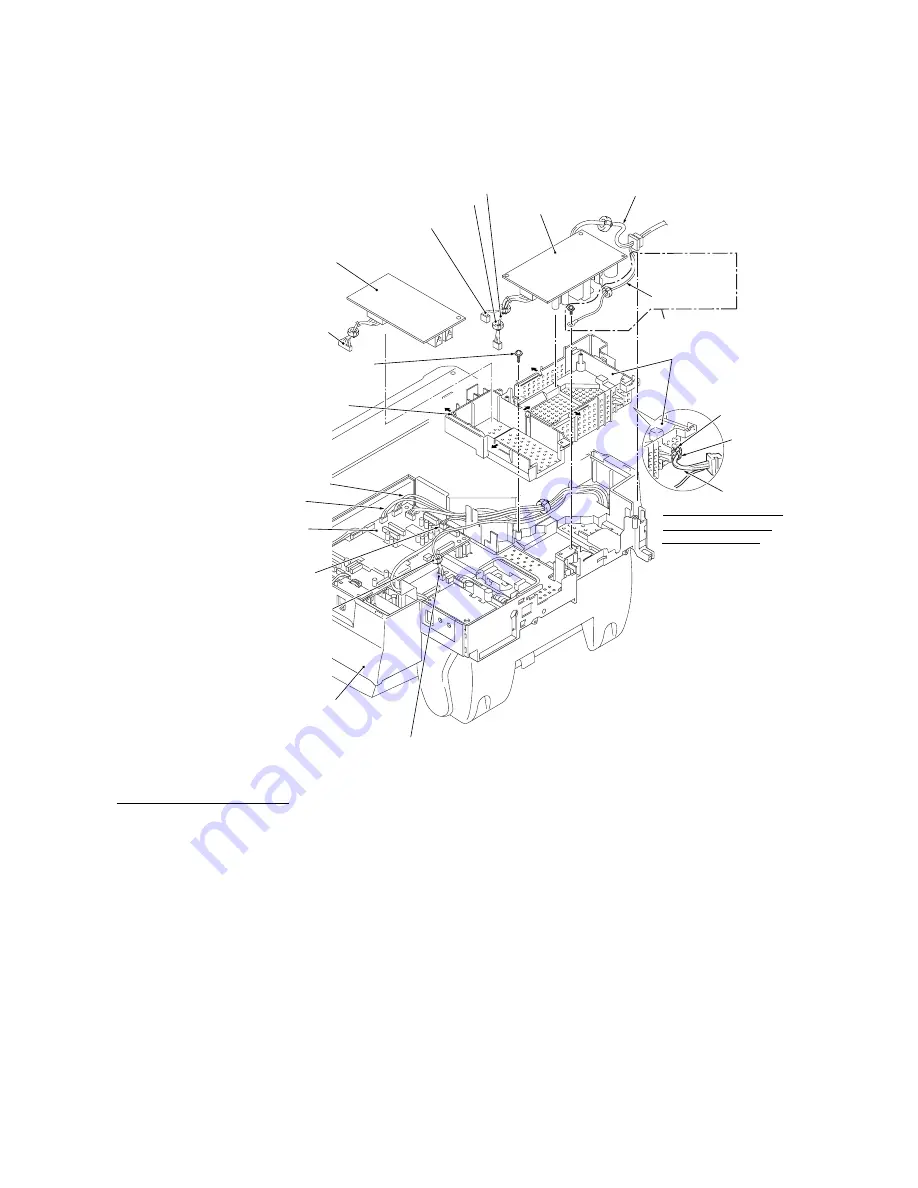
6-18
NCU PCB
NCU-main harness
Latches
Lower cover
Power cord
Cord binder
Securing
the
power
cord
to
the
enclosure
cover
with
the
cord
binder
Enclosure cover
Grounding wire
Taptite, cup B M3x10
Power cord
Power supply PCB
Power supply harness (power-main), black
Power supply harness (power-driver), red
Hole in the
enclosure cover
For the US version only
(Speaker harness)
(CIS travel motor harness)
(Panel-main harness)
(Sensor harness
(ASF-main))
Main PCB
This core is provided for European model only
This core is provided
for European model
only
Reassembling Notes
• When setting the power supply PCB into the enclosure cover, secure the power cord to the
enclosure cover with a cord binder by passing the binder through holes provided in the enclosure
cover.
• For the routing of the NCU-main harness and power supply harness (power-main), refer to
"Routing A" in Section 6.1.15 "Routing of the Harnesses and Flat Cables."
Summary of Contents for MFC-4820C
Page 1: ...FACSIMILE EQUIPMENT SERVICE MANUAL MODEL MFC4820C MFC4420C ...
Page 6: ...CHAPTER 1 PARTS NAMES FUNCTIONS ...
Page 13: ...CHAPTER 2 SPECIFICATIONS ...
Page 19: ...2 5 2 1 4 Environmental Conditions ...
Page 26: ...CHAPTER 3 SETTING UP OF THE MACHINE ...
Page 29: ...3 2 3 2 UNPACKING THE MACHINE The equipment consists of the following major components ...
Page 40: ...CHAPTER 4 THEORY OF OPERATION ...
Page 76: ...CHAPTER 5 ROUTINE MAINTENANCE ...
Page 84: ...CHAPTER 6 DISASSEMBLY REASSEMBLY ...
Page 114: ...6 29 6 1 11 Speaker 1 Pull the speaker and its spring out of the lower cover ...
Page 136: ...CHAPTER 7 MAINTENANCE MODE ...
Page 145: ...7 8 Scanning Compensation Data List ...
Page 160: ...7 23 1st sheet 2nd sheet Vertical Alignment Check Patterns and Head Skew Check Pattern ...
Page 162: ...7 25 Margin Check Patterns ...
Page 170: ...CHAPTER 8 ERROR INDICATION AND TROUBLESHOOTING ...
Page 197: ...MFC4820C MFC4420C Appendix 1 Serial No Descriptions ...
Page 205: ...App 2 4 Click Finish to return to Windows ...
Page 209: ...MFC4820C MFC4420C Appendix 3 EEPROM Customizing Codes ...
Page 212: ...MFC4820C MFC4420C Appendix 4 Firmware Switches WSW ...
Page 252: ...App 4 40 WSW48 to WSW50 Selector No Function Setting and Specifications 1 8 Not used ...
Page 253: ...MFC4820C MFC4420C Appendix 5 Re Packing Instructions ...
Page 255: ...App 5 2 2 Place the machine in the original box with the original packaging material ...
Page 256: ...MFC4820C MFC4420C Appendix 6 Wiring Diagram ...
Page 259: ...A Main PCB 1 5 ...
Page 260: ...A Main PCB 2 5 ...
Page 261: ...A Main PCB 3 5 ...
Page 262: ...A Main PCB 4 5 ...
Page 263: ...A Main PCB 5 5 ...
Page 264: ...B Driver PCB ...
Page 265: ...C NCU PCB ...
Page 266: ...D Control Panel PCB ...
Page 267: ...E Power Supply PCB ...