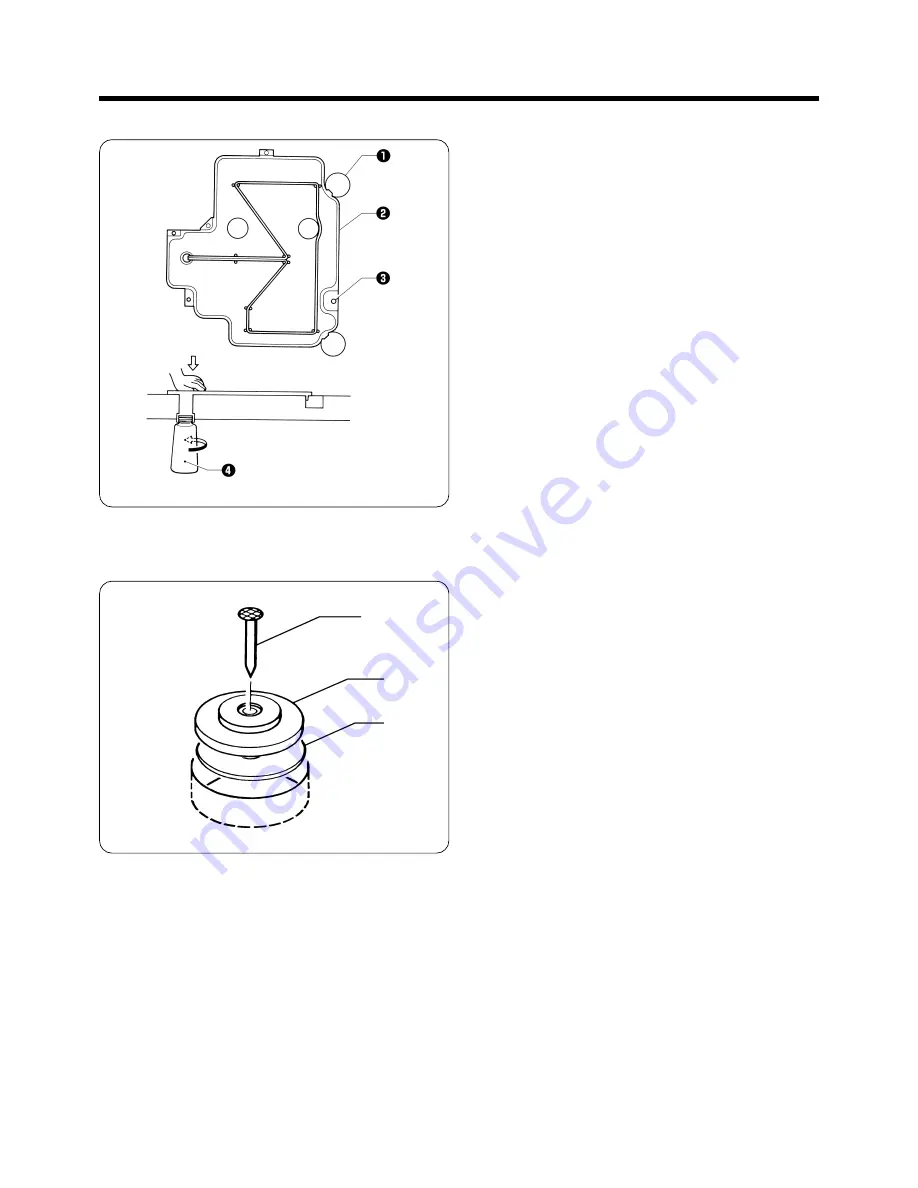
10
3. Installation
LK3-B448E MARKII/BA-16
1. Place the washers
q
and cushions
w
into the two
holes in the work table.
* Adjust the height of the machine head to the button
feeder by the number of the washers
q
.
2. After the height is decided, secure them with the nails
e
.
1. Insert the tabs of the oil pan
w
into the holes for the
cushions
q
, and then secure it in place with the five
nails
e
so that the oil pan
w
is not at an angle.
2. While pushing the oil pan
w
down from above, screw
in the oil container
r
.
3-5. Installing the oil pan
3-6. Installing the cushions
e
w
q