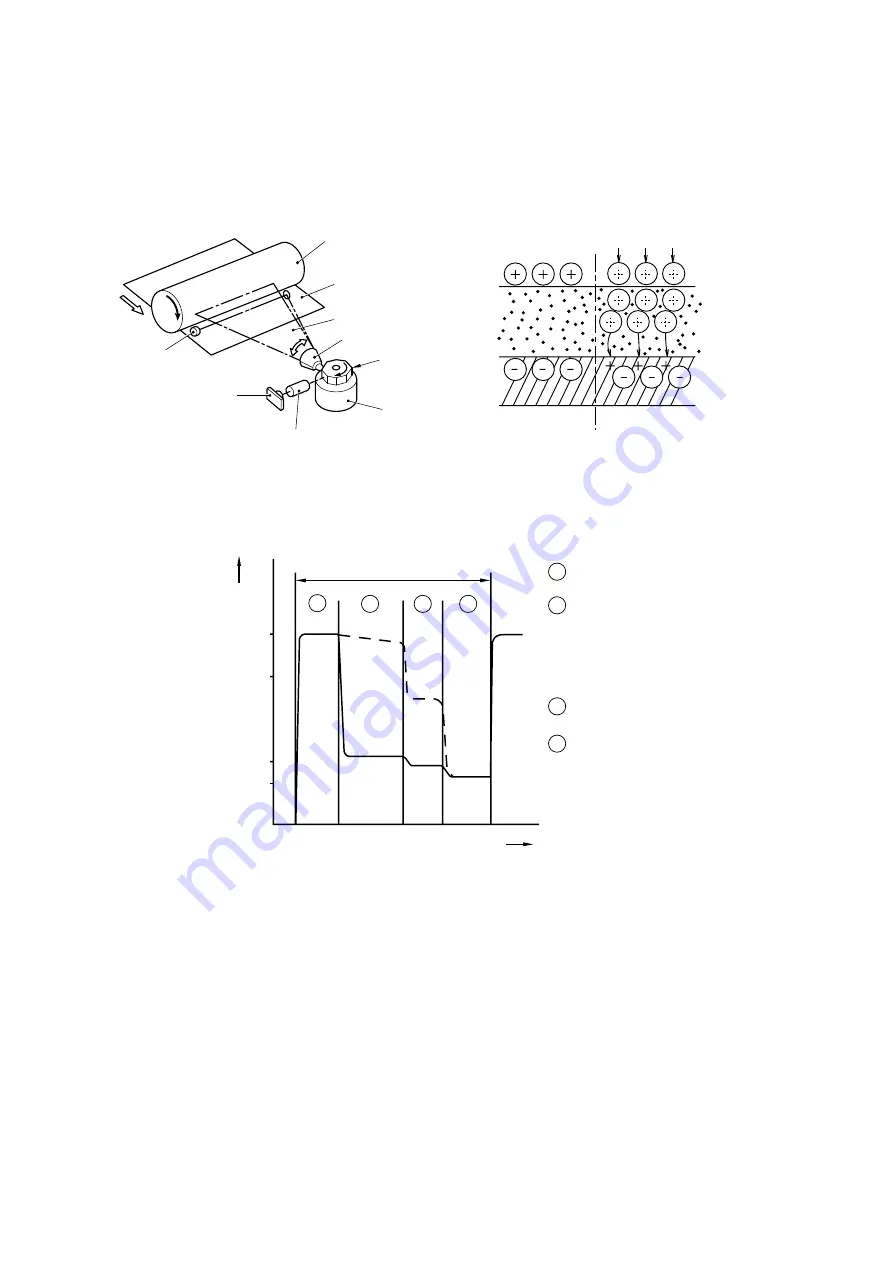
CHAPTER II -21
2.5.2
Exposure Stage
After the drum is positively charged, it is exposed to the light emitted from the laser unit.
Fig. 2.26
The area exposed to the laser beam is the image to be printed. The surface potential of the
exposed area is
reduced forming the electrostatic image to be printed.
1 Cycle of drum
Surface Potential (V)
+1000
+700
+400
+300
1
2
3
4
(a)
(b)
Time
1
2
3
4
Primary charging
Laser beam exposure and developing
(a) Unexposed area
( Non image area )
(b) Exposed area
( Image area )
Transfer the image to paper
Erase the residual potential
Drum
Sleeve
Fig. 2.27
Drum
Paper
Laser beam
f lens
Polygon mirror
Motor
Lens
Laser diode
Laser detector
Laser Beam
Summary of Contents for HL HL-1060
Page 1: ...SERVICE MANUAL MODEL HL 1060 R LASER PRINTER ...
Page 24: ...CHAPTER II 8 1 3 5 DRAM Four 4Mbit DRAM x 8bit are used as the printer memory Fig 2 7 ...
Page 28: ...CHAPTER II 12 1 3 11 Engine I O Fig 2 13 shows the engine interface circuit Fig 2 13 ...
Page 96: ...Appendix 3 Main PCB Circuit Diagram 1 4 CODE UK3400000 B48K246CIR NAME V 3 ...
Page 97: ...Appendix 4 Main PCB Circuit Diagram 2 4 CODE UK3400000 B48K246CIR NAME V 4 ...
Page 98: ...Appendix 5 Main PCB Circuit Diagram 3 4 CODE UK3400000 B48K246CIR NAME V 5 ...
Page 99: ...Appendix 6 Main PCB Circuit Diagram 4 4 CODE UK3400000 B48K246CIR NAME V 6 ...
Page 100: ...Appendix 7 Driver PCB Circuit Diagram CODE UK3634000 B48K280CIR NAME V 7 ...
Page 105: ...Appendix 12 SR PCB Circuit Diagram CODE UK3653000 B48K284CIR NAME V 12 ...