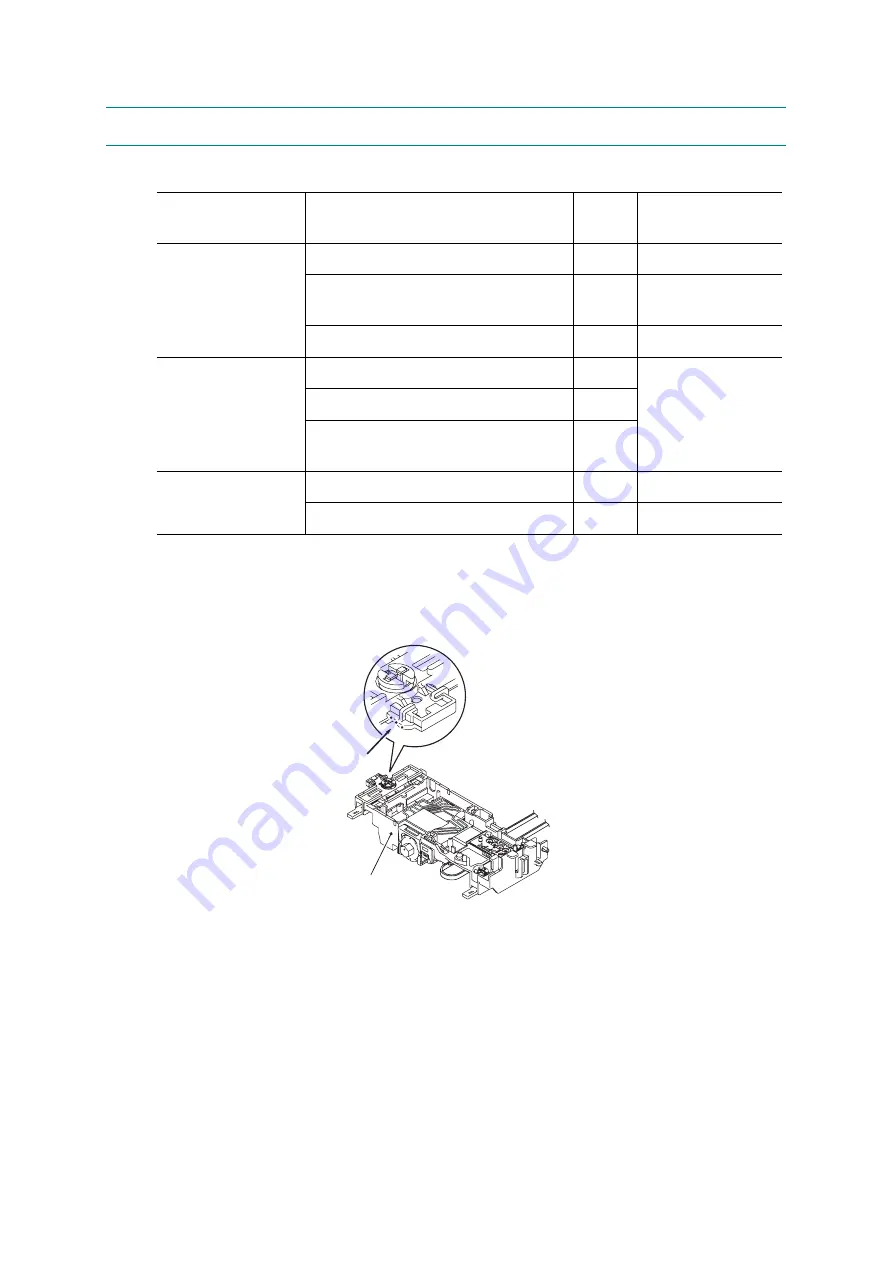
6-106
Confidential
6.2
LUBRICATION
Apply the specified lubricants to the lubrication points as shown below.
Head/carriage unit
Apply a 1 mm diameter ball of grease (Permalub BAN-5) to the lubrication points below.
Lubricant type
(Manufacturer)
Lubrication points
No. of
points
Lubricant amount
per point
Permalub BAN-5
(Nippon Koyu)
Head/carriage unit
3
1 mm diameter ball
Motor plate and CR guide rail (bottom
edges)
4
1 mm diameter ball
Switching lever guide
1
3 mm diameter ball
FLOIL BG1319
(Kanto Kasei)
CR guide rail (upper face)
11
2 mm diameter ball
CR support chassis (upper face)
11
CR support chassis (front and rear
sides of upright rear edge)
28
Molykote EM-30LP
(Dow Corning)
Paper pull-in idle gear
1
3 mm diameter ball
Paper pull-in roller L
2
1 mm diameter ball
Head/carriage unit
(6_84)
Apply grease here.
Summary of Contents for DCP-6690CW
Page 7: ...v Confidential SAFETY PRECAUTIONS Symbols used in the documentation ...
Page 8: ...vi Confidential ...
Page 9: ...vii Confidential ...
Page 10: ...viii Confidential ...
Page 11: ...ix Confidential ...
Page 12: ...x Confidential ...
Page 13: ...xi Confidential ...
Page 14: ...Confidential CHAPTER 1 PARTS NAMES AND FUNCTIONS ...
Page 18: ...1 3 Confidential 1 2 CONTROL PANEL DCP6690CW 5 6 4 1 2 3 ...
Page 19: ...1 4 Confidential ...
Page 20: ...1 5 Confidential MFC6490CW 10 9 7 8 6 1 2 3 4 5 ...
Page 21: ...1 6 Confidential ...
Page 22: ...1 7 Confidential ...
Page 23: ...1 8 Confidential MFC6890CDW 8 7 6 1 2 3 4 5 ...
Page 24: ...1 9 Confidential ...
Page 25: ...1 10 Confidential ...
Page 28: ...Confidential CHAPTER 2 SPECIFICATIONS ...
Page 35: ...2 6 Confidential 2 2 SPECIFICATIONS LIST DCP6690CW MFC6490CW 1 8 ...
Page 36: ...2 7 Confidential 2 8 ...
Page 37: ...2 8 Confidential 3 8 ...
Page 38: ...2 9 Confidential 4 8 ...
Page 39: ...2 10 Confidential 5 8 ...
Page 40: ...2 11 Confidential 6 8 ...
Page 41: ...2 12 Confidential 7 8 ...
Page 42: ...2 13 Confidential 8 8 ...
Page 43: ...2 14 Confidential MFC6890CDW 1 10 ...
Page 44: ...2 15 Confidential 2 10 ...
Page 45: ...2 16 Confidential 3 10 ...
Page 46: ...2 17 Confidential 4 10 ...
Page 47: ...2 18 Confidential 5 10 ...
Page 48: ...2 19 Confidential 6 10 ...
Page 49: ...2 20 Confidential 7 10 ...
Page 50: ...2 21 Confidential 8 10 ...
Page 51: ...2 22 Confidential 9 10 ...
Page 52: ...2 23 Confidential 10 10 ...
Page 53: ...Confidential CHAPTER 3 THEORY OF OPERATION ...
Page 110: ...Confidential CHAPTER 4 ERROR INDICATION AND TROUBLESHOOTING ...
Page 114: ...4 2 Confidential 1 Error messages appearing on the LCD ...
Page 115: ...4 3 Confidential For MFC only ...
Page 116: ...4 4 Confidential For MFC only ...
Page 117: ...4 5 Confidential For MFC only ...
Page 118: ...4 6 Confidential ...
Page 119: ...4 7 Confidential ...
Page 172: ...Confidential CHAPTER 5 HANDLING DATA HELD IN THE MACHINE PRIOR TO REPAIR ...
Page 179: ...Confidential CHAPTER 6 DISASSEMBLY REASSEMBLY AND LUBRICATION ...
Page 292: ...Confidential CHAPTER 7 ADJUSTMENTS AND UPDATING OF SETTINGS REQUIRED AFTER PARTS REPLACEMENT ...
Page 299: ...7 5 Confidential 8 Alert warning message of WHQL appears Click Continue Anyway to proceed ...
Page 308: ...7 14 Confidential Head Positioning Test Pattern ...
Page 314: ...7 20 Confidential Paper Feeding Check Pattern for the Paper Ejection Roller ...
Page 315: ...7 21 Confidential Paper Feeding Check Pattern for the Paper Feed Roller Paper Tray 2 ...
Page 317: ...7 23 Confidential Vertical Alignment Check Patterns 2 2 ...
Page 321: ...7 27 Confidential Left and Right Margin Check Pattern ...
Page 322: ...7 28 Confidential Bottom Margin Check Pattern ...
Page 333: ...7 39 Confidential ADF Copy Chart A B C D ...
Page 337: ...Confidential CHAPTER 8 CLEANING ...
Page 341: ...8 3 Confidential Maintenance unit Head caps Head wiper cleaning_BHM9_E Rubycel stick ...
Page 344: ...Confidential CHAPTER 9 MAINTENANCE MODE ...
Page 353: ...9 7 Confidential Scanning Compensation Data List ...
Page 356: ...9 10 Confidential Test Pattern ...
Page 361: ...9 15 Confidential Configuration List ...
Page 379: ...9 33 Confidential Paper Feeding Check Pattern for the Paper Ejection Roller ...
Page 380: ...9 34 Confidential Paper Feeding Check Pattern for the Paper Feed Roller Paper Tray 2 ...
Page 384: ...9 38 Confidential Vertical Alignment Check Patterns 1 2 ...
Page 385: ...9 39 Confidential Vertical Alignment Check Patterns 2 2 ...
Page 389: ...9 43 Confidential Left and Right Margin Check Pattern ...
Page 390: ...9 44 Confidential Bottom Margin Check Pattern ...
Page 421: ...App 2 3 Confidential 8 Alert warning message of WHQL appears Click Continue Anyway to proceed ...
Page 502: ...App 6 4 Confidential B Power supply PCB 100 V series ...
Page 503: ...App 6 5 Confidential B Power supply PCB 200 V series ...