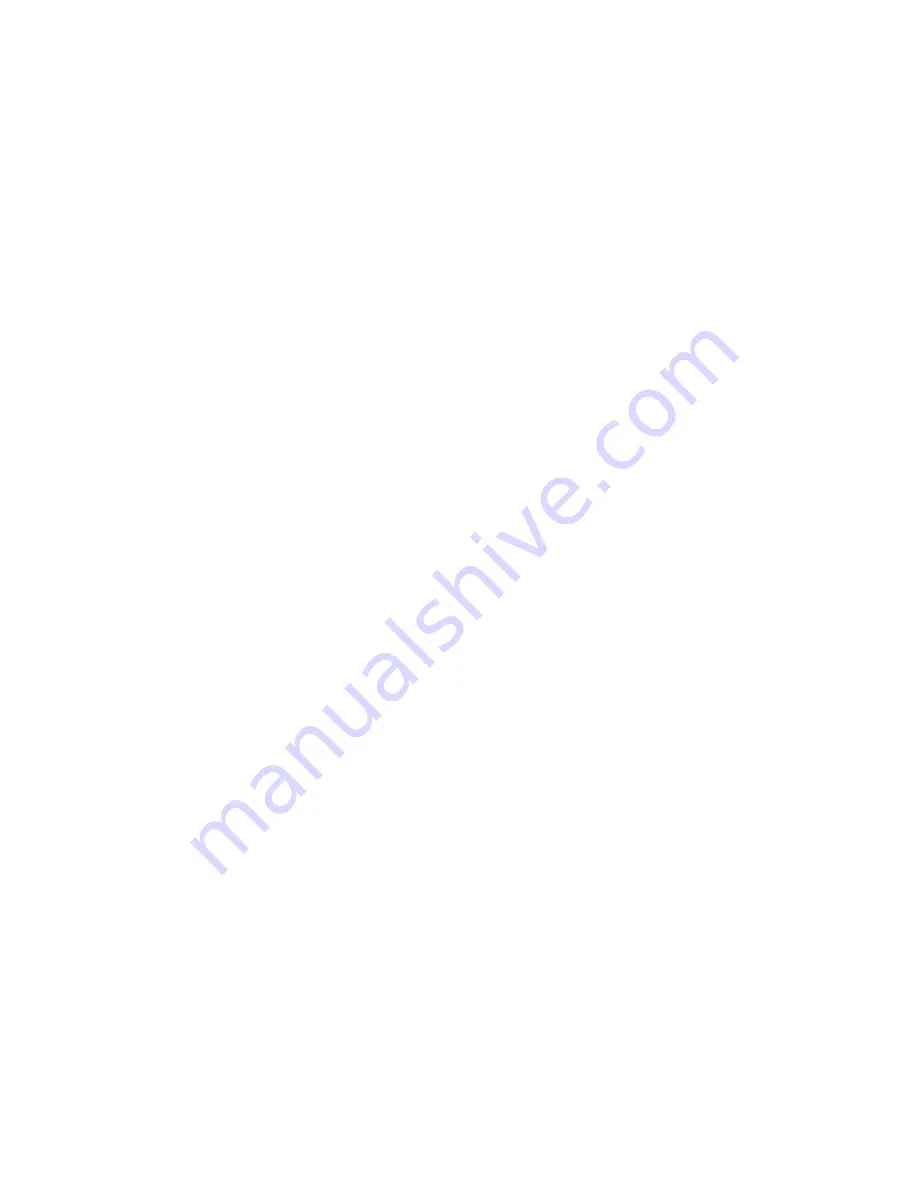
MASS-STREAM
TM
Instruction Manual D-6200
9.17.112A – Date of issue: 2017-03
Page 8 off 12
All instruments described in this manual carry the CE-mark. Therefore they have to
comply with the EMC requirements valid for these instruments. However compliance with
the EMC requirements is not possible without the use of proper cables and
connector/gland assemblies.
In case the instrument is connected to other devices (e.g. power supply) ensure that the
operating voltage complies with the supply voltage given on the name plate and that the
function of the shielding is not affected. M+W Instruments GmbH recommends using
standard cables following the CE-requirements and could supply them when needed.
1.3 Operation and Maintenance
When the power is switched on a warm-up period of at least 30 sec is required allowing
the instrument’s thermal stabilisation. Afterwards the instrument will work with an
accuracy of approximately 4% FS. It takes around 30 minutes until the optimal stability is
reached and the instrument will work with an accuracy of < 3% FS. This is supposed to be
performed with or without gas flow. To avoid creating gradients it is recommended that
gas and ambient temperature are kept at the same level
(max ΔT
approx. ± 2…3 °C).
Otherwise the accuracy of this thermal measurement could be affected in an
unpredictable manner.
Be sure that the specified pressures have been applied. Pressure surges, as may occur
during the system pressurisation, must be avoided. The control valve cannot be used as a
shut-off valve. When starting up, always bring the instrument gradually up to the level of
operating conditions.
There are no regular maintenance checks required for the instrument’s operation. It has to
be ensured that a possible mounted inline filter is checked and cleaned on a regular
basis. We recommend having the calibration checked every 24 months by the supplier or
an authorized service partner.