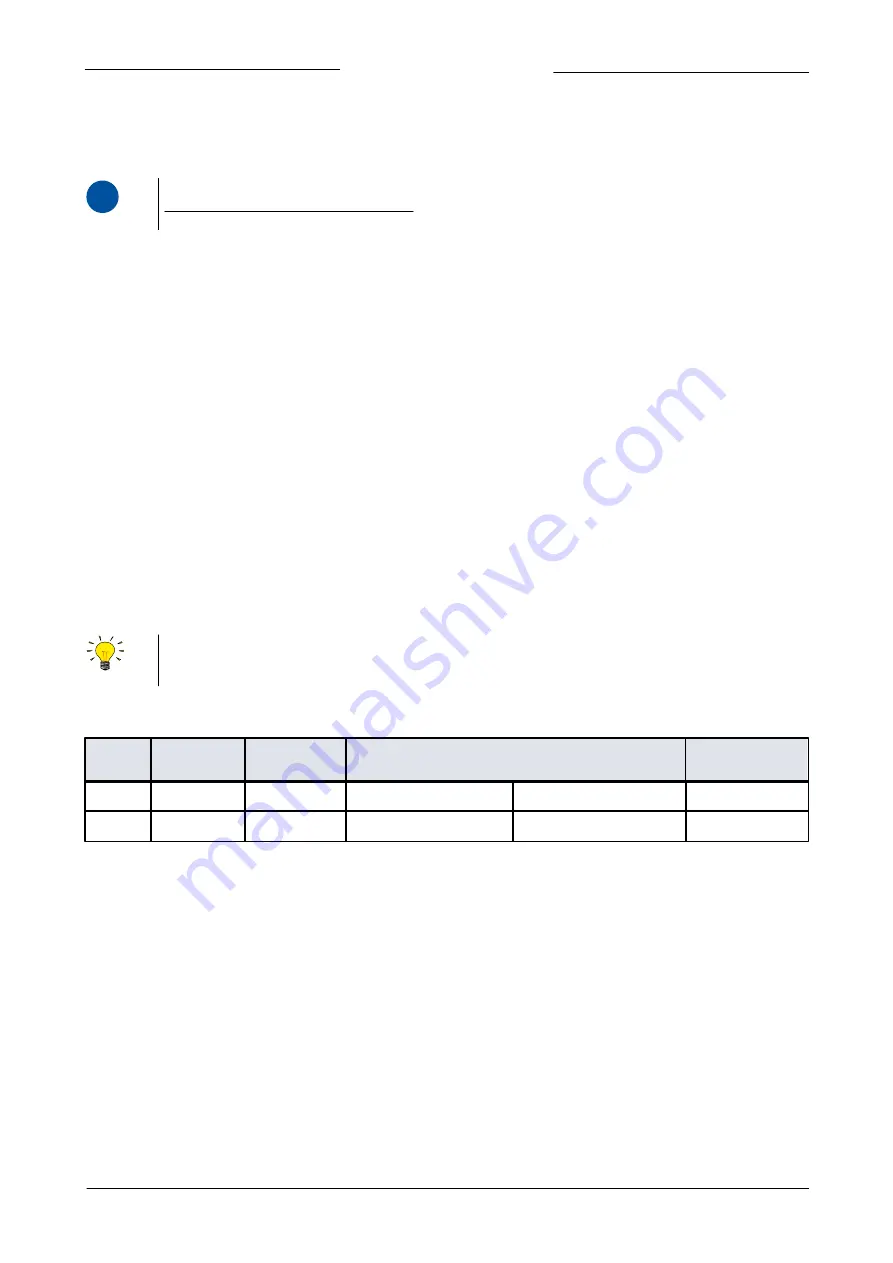
Bronkhorst®
Vapor Delivery Module
9.17.079
8
3
Technical specification
3.1
Physical dimensions
i
www
For overall dimensions please consult supplied dimensional drawing 7.05.901. This documents is available on:
http://www.bronkhorst.com/en/downloads
or can be obtained by contacting our local sales & service
representatives
3.2
Environmental conditions
• Ambient temperature
: 5°C - 40°C.
• Relative humidity
: Maximum relative humidity 80%, for temperatures up to 31°C decreasing linearly
to 50% relative humidity at 40°C.
• Height altitude
: Up to 2000 [m].
3.3
Ingress protection class
IP20, according IEC standard 60529.
3.4
Fluidic connections
3.4.1
General
The Vapor Delivery Module gas and liquid supply are equipped with compression type or face-seal-fittings. Normally these fittings
are BSP parallel threads types which have to be used in combination with elastomeric O-rings to seal to the Vapor Delivery Module.
Occasionally fittings are orbital welded to the VDM-Series.
For leak tight installation of compression type fittings be sure that the tube is inserted to the shoulder in the fitting body and that
no dirt or dust is present on tube, ferrules or fittings.
For exact information on the fitting, please contact Swagelok for further instructions or documentation.
Always check your system for leaks, before applying fluid pressure. Especially if toxic, explosive or other dangerous
fluids are used.
3.4.2
Flow ranges of used components
Model
Heater
model
Thermal
power
Max. capacity
1
Max temp.
SW-10n
W-100A
10 [W]
1...30 [g/h] liquid
0.1...4 [l
n
/min] gas
200°C
SW-20n
W-200A
100 [W]
10...120 [g/h] liquid
0.2...10 [l
n
/min] gas
200°C
1
Depends on liquid and process pressure; table based on water at 1 atmosphere.
For other liquids or pressure conditions please consult the manufacturer or your local sales representative.