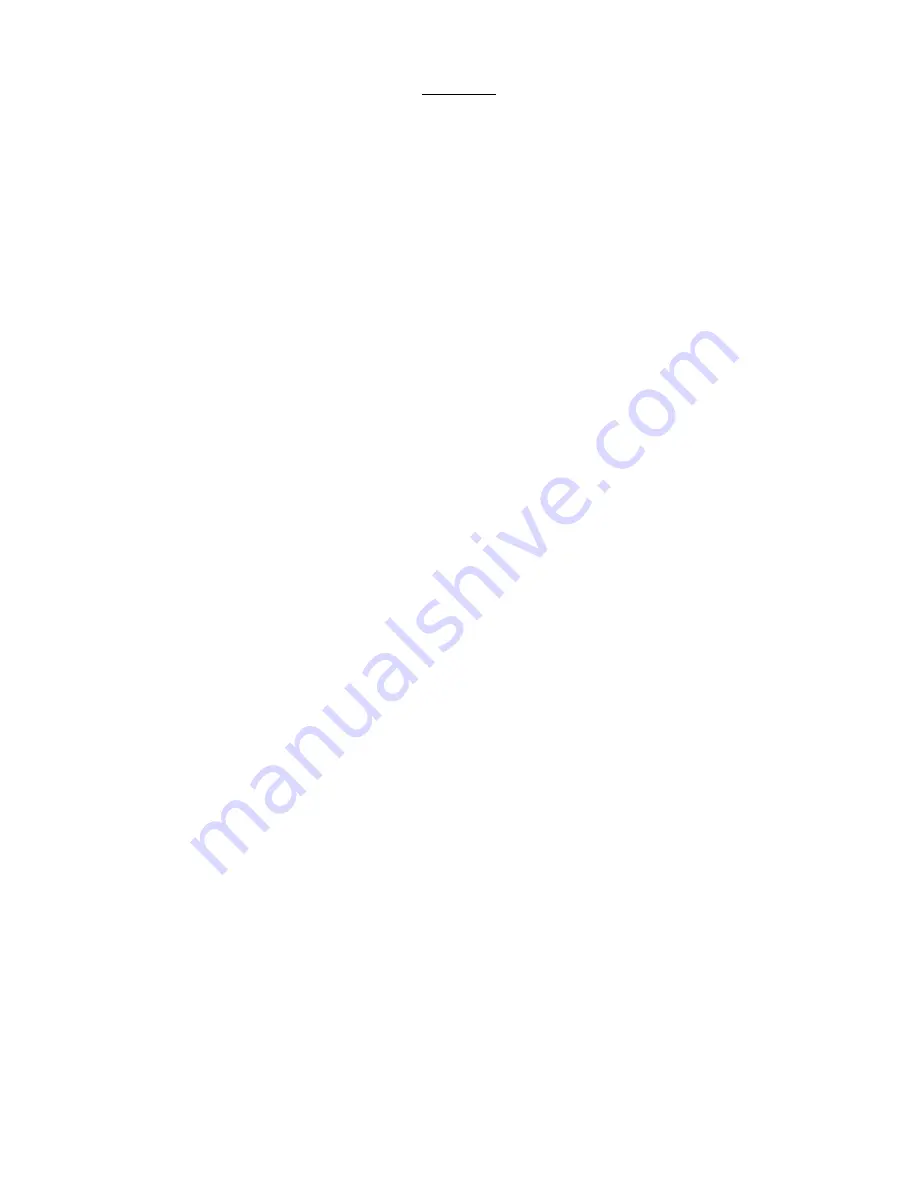
3-462
CAUTION
For a correct assembly, it is necessary to have a minimum pre-load of 5% of the cable
breaking force. The cable breaking force depends on the diameter and of the cable type,
and it must be indicated on the cable certificate.
6. Slowly rotate the hoist while applying tension on the cable in front of the boom. Wear
heavy leather gloves and wrap rags around the cable to wipe off any dirt from the cable.
Keep hands away from the sheaves and hoist drum while the cable is moving.
7. After two turns of the drum, stop the hoist and push the cable into the drum groove if it has
come out.
8. Slowly rotate the drum until the first layer of cable is on the drum. If any gaps between the
rope appear, back up the hoist and rewind. There must be no gaps in the first layer.
9. After the first layer is on the drum, the hoist may be turned a little faster until the remainder
of the cable is installed.
10. Leave about 40 feet (12 m) of cable on the ground to install the sheave block. The sheave
block must be used for cable preloading to ensure enough rope can be spooled off the
hoist drum. See the Operation Section for instructions on reeving and wedge socket at-
tachment.
11. Install the cable retainer pins and cotters in the tip sheave plates.
12. For the cable preloading, set the outriggers and attach a load of about 3000 pounds
(1300 kg). EXTEND the boom fully. Position the load at a 10-foot (3 m) load radius over
the side of the crane. HOIST UP and LOWER the load 3 times, and check winding of the
rope on the hoist.
13. Attach about 8000 pounds (3600 kg) and repeat. Be sure that the cable winds evenly.
14. Never lift more than the rated load on the Capacity Chart for the parts-of-line and type of
wire rope being used.
15. Lubricate the cable as recommended in the Wire Rope Lubrication section. Inspect, main-
tain, and replace the cable in accordance with ASME B30.5, Section 5-2.4.
Summary of Contents for IC-400-3B
Page 4: ...1 2 IC 400 B DIMENSIONS...
Page 5: ...1 3 IC 600 A TURNING DIMENSIONS...
Page 32: ...2 2M3 CAPACITY CHART...
Page 33: ...2 213 CAPACITY CHART METRIC...
Page 46: ......
Page 55: ...3 02 IC 400 3B LUBRICATION CHART...
Page 56: ...3 1 2 IC 400 3B LUBRICATION CHART...
Page 57: ...3 112 IC 400 3B LUBRICATION CHART...
Page 73: ...3 27 JIC HYDRAULIC SCHEMATIC...
Page 85: ...3 39 BOOM CHAIN ADJUSTMENT...
Page 92: ...1 W I R I N G IC 400 B WIRING DIAGRAM...
Page 93: ...2 W I R I N G...
Page 94: ...3 W I R I N G...
Page 95: ...4 W I R I N G...
Page 96: ...5 W I R I N G...
Page 97: ...6 W I R I N G...
Page 98: ...7 W I R I N G...
Page 99: ...8 W I R I N G...
Page 100: ...9 W I R I N G...
Page 101: ...10 W I R I N G...
Page 102: ......