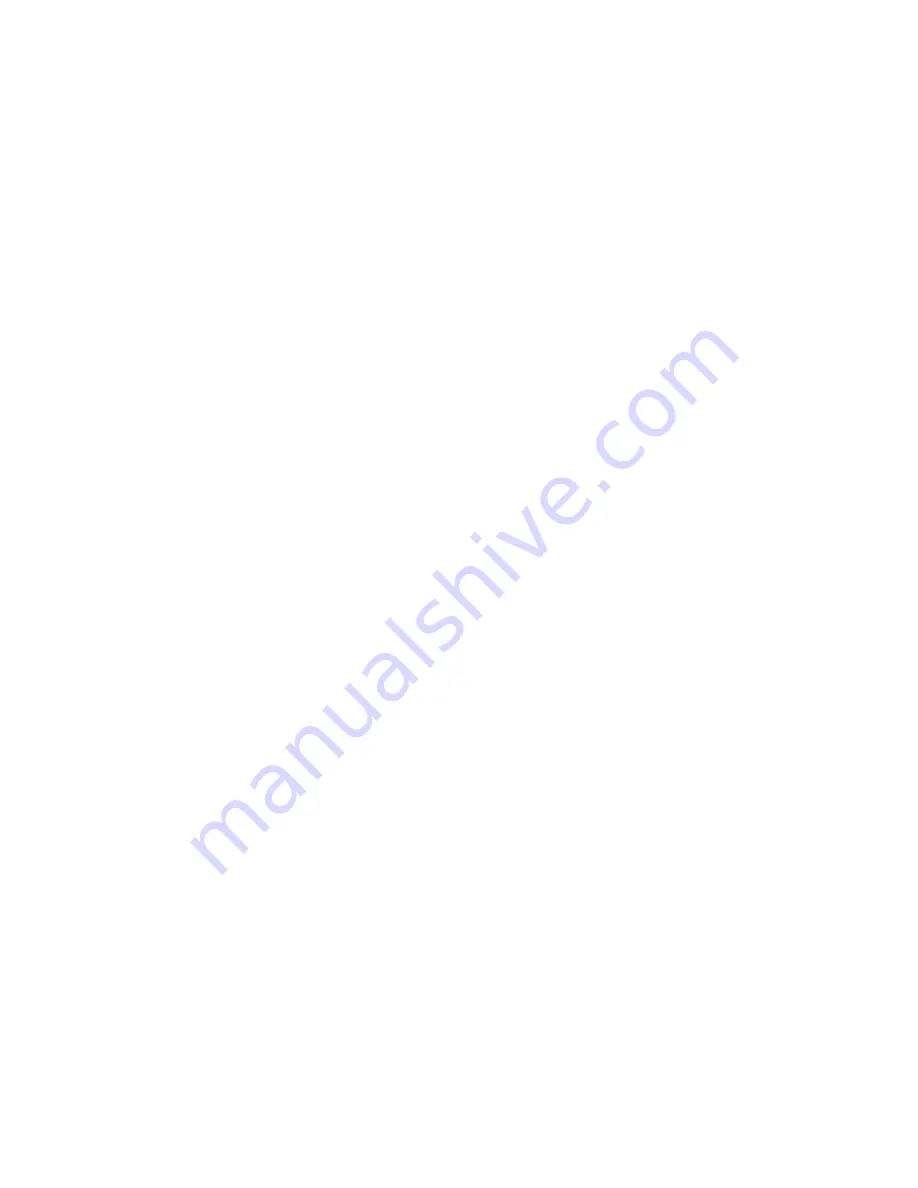
3-11
7.
Slowly rotate the hoist while applying tension on the cable in front of the boom.
Wear heavy leather gloves and wrap rags around the cable to wipe off any dirt from
the cable. Keep hands away from the sheaves and hoist drum while the cable is
moving.
8.
After two turns of the hoist drum, stop the hoist and push the cable tightly against
the flange of the drum with a wooden or rubber mallet.
9.
Slowly rotate the drum until the first layer of cable is on the drum. If any gaps
between the rope appear, stop the hoist and tap the cable toward the flange. There
must be no gaps.
10. After the first layer is on the drum, the hoist may be turned a little faster until the
remainder of the cable is installed.
11. Leave about 15 feet (4.6 m) of cable on the ground to install the sheave block. See
the Operation Section for instructions on reeving and wedge socket attachment.
12. Install the cable retainer pins and cotters in the tip sheave plates.
13. For the cable break in, lower the outriggers and attach a load of about 1,000
pounds (450 kg). Extend the boom fully. Position the load at a 6 foot (2.0 m) load
radius over the left-hand side of the crane. Hoist and lower the load three times
and check winding of the rope on the hoist.
14. Attach about 2,500 pounds (1100 kg) and repeat. Be sure that the cable winds
evenly on the hoist.
15. If the cable appears to twist too much, remove the sheave block and rewind the
cable on the drum as in Steps 7-11.
16. Never lift more than the rated load on the Capacity Chart for the parts of line and
type of wire rope being used.
17. Lubricate the cable as recommended in the "Wire Rope Lubrication" section.
Inspect, maintain and replace the cable in accordance with ANSI B30.5-2007,
Section 5-2.4.
Summary of Contents for IC-20-1J
Page 6: ...1 2 DIMENSIONS AND ORIENTATION IC 20 1J Courtesy of Crane Market...
Page 7: ...1 3 TURNING DIMENSIONS Courtesy of Crane Market...
Page 25: ...2 11 Courtesy of Crane Market...
Page 26: ...2 12 Courtesy of Crane Market...
Page 36: ...Courtesy of Crane Market...
Page 44: ...3 8 IC 20 LUBRICATION CHART Courtesy of Crane Market...
Page 48: ...3 12 JIC SCHEMATIC Courtesy of Crane Market...
Page 50: ...3 14 STEERING SYSTEM Courtesy of Crane Market...
Page 52: ...3 16 IC 20 PROPULSION SYSTEM Courtesy of Crane Market...
Page 62: ...Courtesy of Crane Market...
Page 63: ...Powered by TCPDF www tcpdf org Courtesy of Crane Market...