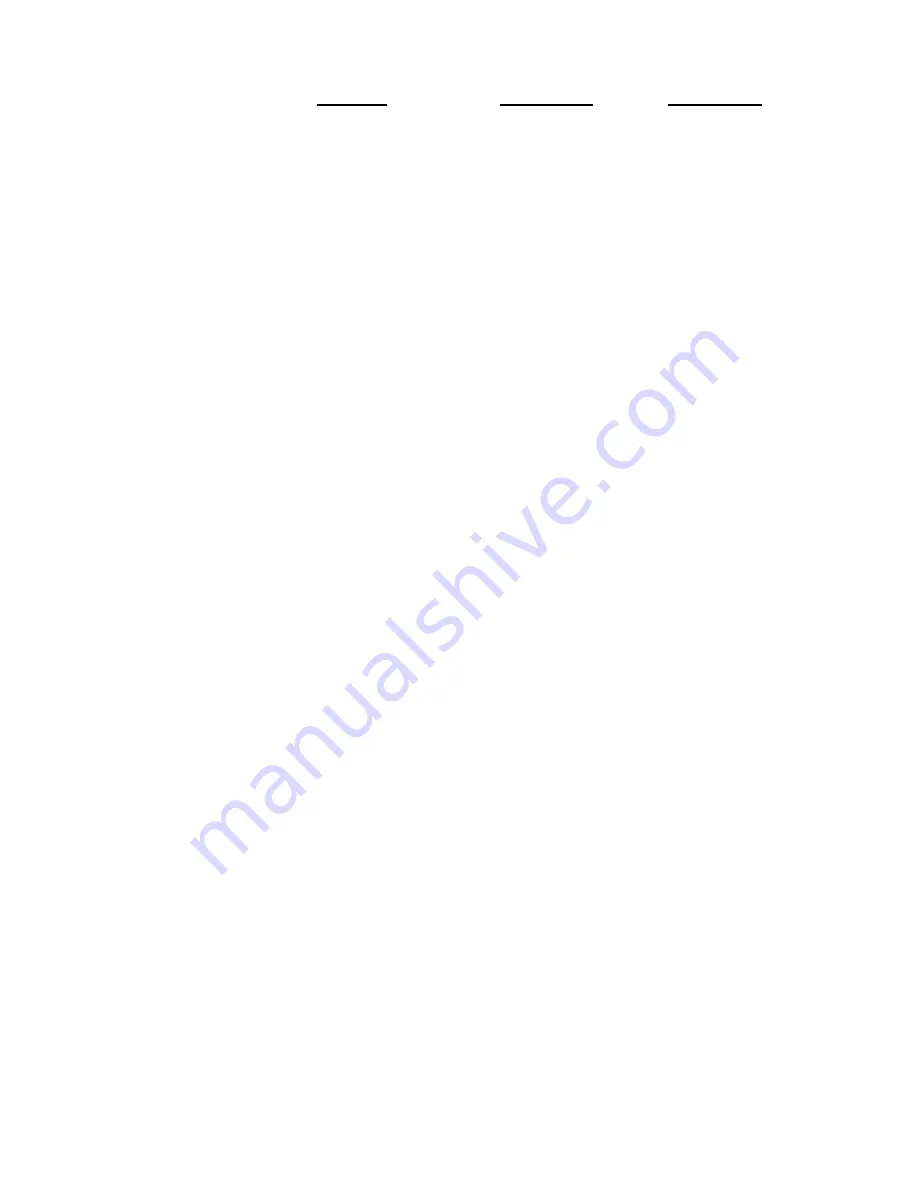
1-7
4X2 GAS
4X2 DIESEL
4X4 DIESEL
Travel
Drawbar Travel Drawbar Travel
Drawbar
Speed
Pull
Speed
Pull
Speed
Pull
Gear
Ratios
MPH
LBS
MPH
LBS
MPH
LBS
(km/h)
(kg)
(km/h)
(kg)
(km/h)
(kg)
1st
5.72/1
4
9500
4
10500
3
13500
(6)
(4300)
(6)
(4800)
(5)
(6100)
2nd
3.23/1
7
5500
7
6000
6
9000
(11)
(2500)
(11)
(2700)
(10)
(4100)
3
rd
1.77/1
12
3000
13
3500
10
5000
(19)
(1300)
(21)
(1600)
(16)
(2300)
4th
1.00/1
19
1800
21
2000
17
2800
(31)
(800)
(34)
(900)
(27)
(1300)
(Calculated values
;
wheels may spin before these values are reached.)
Front
Axle:
Standard:
Planetary drive axle with 11.625/1 ratio. Differential is “No Spin
.
” Front axle
is mounted rigidly to frame.
Optional 4-Wheel drive:
Planetary drive/steer axle with integral drop box input for an overall 13.76/1
ratio. Differential is “No Spin.” Oscillation is 1
½
degrees in either direction.
Only available with mining and industrial tires. Net Weight: 600 pounds (270 kg)
Rear
Axle:
Standard:
Drop-center axle beam casting with 1½ degree oscillation in either direction.
Optional 4-Wheel drive:
Planetary drive/steer axle with overall 13.76/1 ratio including the reduction
through the front-axle-mounted drop box. Differential is limited slip. Oscillation
is 1
½
degrees in either direction. Only available with mining and industrial
tires. Diesel engine is required for this option. Net Weight: 935 pounds (425 kg)
including front axle.
Steering:
Standard:
Hydraulic steering unit with one double-rod cylinder on rear axle and one
double-rod cylinder on front axle. Allows limited steering when engine is not
running. Rear axle is the primary steer. An electric switch in the operator's
compartment is used to select rear-wheel steering, four-wheel round steering or
crab steering. Electronic sensors and control box automatically align the
steering when a new mode is selected.
Brakes:
Standard:
Four-wheel hydraulic. Wet disc brakes are on the front and rear axles. Parking
brake is disc type.
Brakes on Optional 4-Wheel Drive:
Wet disc on both axles. Parking brake is disc type.
Summary of Contents for IC-100-3A
Page 6: ...1 2 IC 100 3A DIMENSIONS...
Page 7: ...1 3 IC 100 A TURNING DIMENSIONS...
Page 18: ......
Page 33: ...2 15...
Page 52: ...3 8 IC 100 LUBRICATION CHART...
Page 57: ...3 13...
Page 58: ...3 14...
Page 68: ......
Page 69: ......