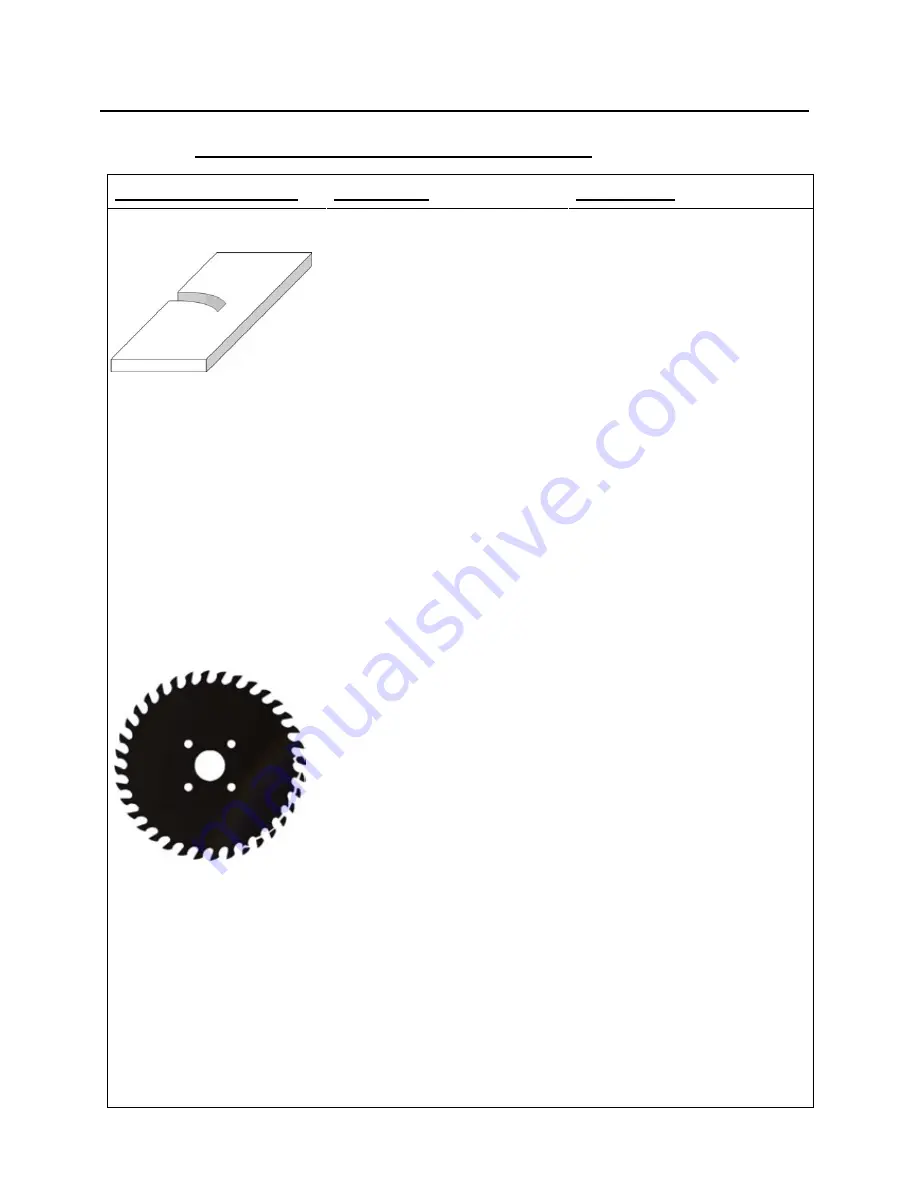
Brobo Group
CHAPTER 7 - Troubleshoot
7.1. Troubleshooting For Blade and Cutting Problems
PROBLEM IDENTIFIED
DIAGNOSIS
SOLUTIONS
Cuts produced are not at 90
and/or are not perpendicular
Frequent and/or excessive
teeth breaking
Head speed too low or too high
Blade with worn teeth
Angularity of blade to workpiece
back fence and vice clamps
Blade not perpendicular to work
surface
Broken teeth
Incorrect lubricant/coolant fluid
Material too hard
Blade not worn in correctly
Reduce or increase head speed
respectively.
Replace with new blade, with
reference to
Section 5.1 Changing
the Blade.
Adjust the position of the blade so
that it is at right angles to the
workpiece back fence using the 0
notch as reference; set the stops at
45
left and right using the method
described in
Section 5.2 Adjusting
the Cutting Angle.
Adjust
the
blade
using
the
appropriate screws such that it is
perpendicular to the work surface.
Check the hardness of the material
being cut corresponds within the
capabilities of the blade.
Check the water and oil mixture;
check that the holes and/or hose are
not blocked; direct the nozzles
correctly;
check
that
the
lubricant/coolant fluid conforms to
those specified in
Section 6.3
General Maintenance of Function
Components.
Check the cutting speed, feed speed,
blade type and parameters are
correct for the particular application.
With a new blade, it is necessary to
start cutting at
half feeding speed
.
After a normalising period (cutting
surface about 300cm
2
for hard
materials and 1000cm
2
for softer
materials), both cutting and feed
speeds can be brought up to normal
values.