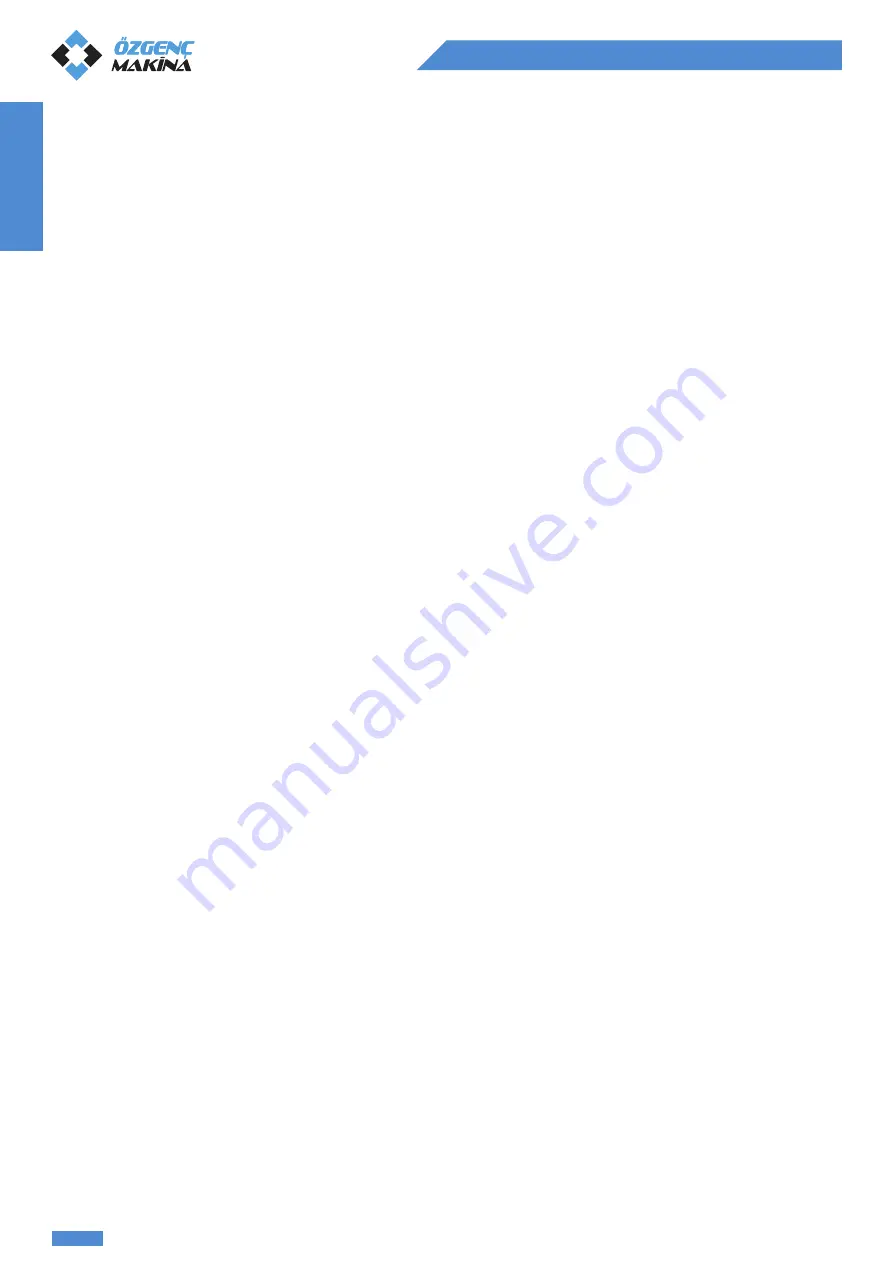
4
2
OMRM 125 PRO machine is designed to cut PVC and aluminum profiles. It is wrong and forbidden to use for
purposes of other than its intended use. Our company cannot be held responsible for misuses.
General Features;
•
It offers precise cutting at 0° to 180° and intermediate angles.
•
Fast adjustment buffers for 0°, 15°, 30°, 45°, 60°, 75°and 90° angles
•
Tray fixation arm for intermediary angles
•
Chip clogging is prevented with special design flat surface
•
Diamond saw diameter of Ø600 mm
•
Protective cover switch for a safe cutting
•
Vertical and horizontal pneumatic press system
•
Adjustable saw output speed
•
Offers the conveyor with meter on the right side and the carrier conveyor on the life side (3 meters each)
•
Hydro-pneumatic and Cooling Assembly for Aluminum cutting
•
Protective cover runs automatically
•
Power supply protects the system against sudden voltage changes
Procedures Performed;
•
Cutting operation of PVC and aluminum profiles takes place at an angle range of 0° - 180°.
INTENDED USE
Summary of Contents for OMRM 125 PRO
Page 1: ...OMRM 125 PRO AUTOMATIC SINGLE HEAD ALUMINIUM PROFILE CUTTING MACHINE OPERATING MANUAL ...
Page 10: ...9 4 4 1 General Structure 10 4 2 Machine Placement 12 MACHINE STRUCTURE AND PLACEMENT ...
Page 43: ...42 OMRM 125 PRO 9 PROBLEMS AND SOLUTIONS ...
Page 45: ...44 OMRM 125 PRO 10 WARRANTY DISCLAIMER ...
Page 49: ...48 OMRM 125 PRO 1 ELECTRICAL CIRCUIT DIAGRAM ...
Page 50: ...49 ...
Page 51: ...50 OMRM 125 PRO ...
Page 52: ...51 ...
Page 53: ...52 OMRM 125 PRO ...
Page 54: ...53 ...
Page 55: ...54 OMRM 125 PRO ...
Page 56: ...55 ...
Page 57: ...56 OMRM 125 PRO ...
Page 58: ...57 ...
Page 59: ...58 OMRM 125 PRO 2 PNEUMATIC CIRCUIT DIAGRAM ...
Page 62: ...61 1 No Name Quan ty 1 Ø40 x 60 mm Double Acting Pneumatic Cylinder 2 Upper Body ...
Page 65: ...64 OMRM 125 PRO Right Conveyor 1 No Name Quan ty 1 Profile Sliding Roller 8 ...
Page 66: ...65 Left Conveyor 1 No Name Quan ty 1 Profile Sliding Roller 8 ...