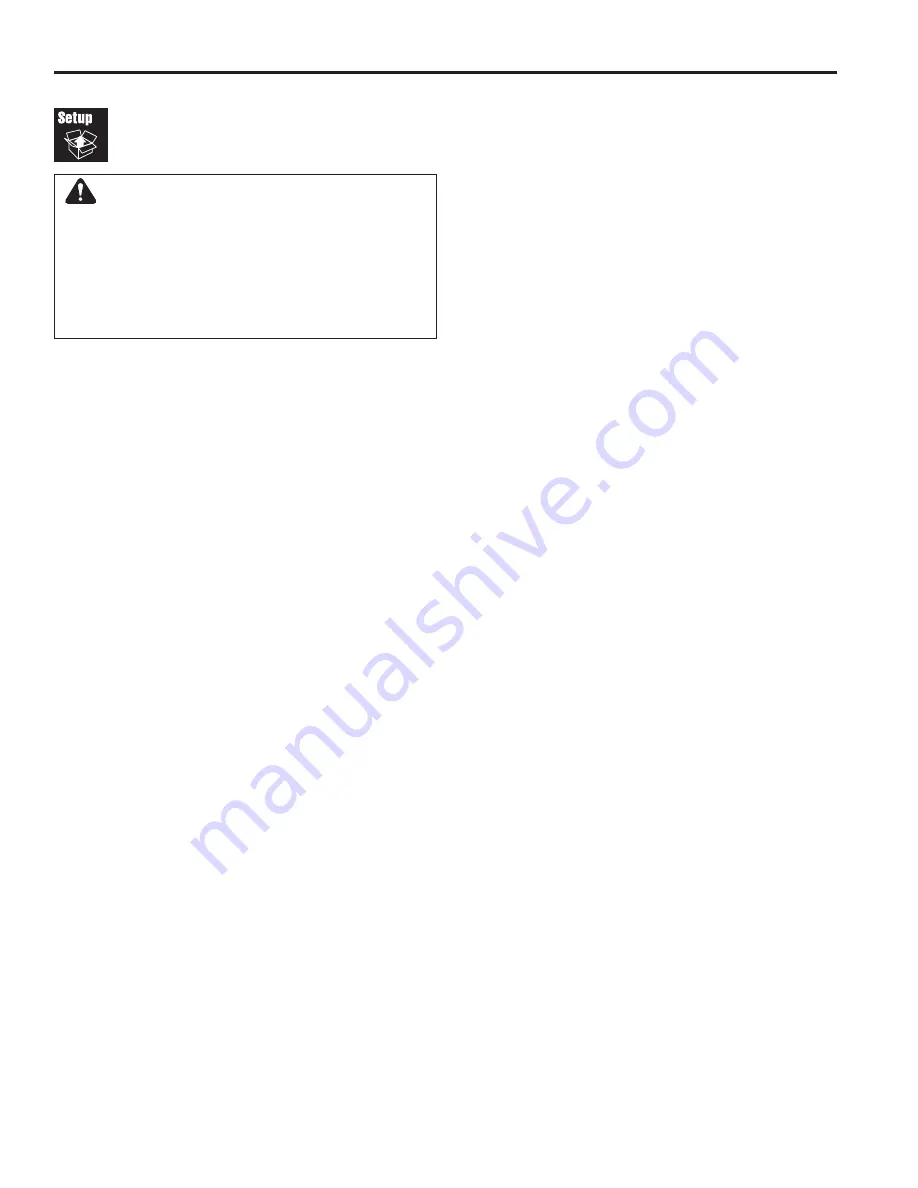
Not for
Reproduction
8
Simplicity / Massey Ferguson / Snapper ZTR
Perform
Safety Checks
Functional Tests
1. Check for loose bolts, screws, nuts, etc.
2. Start the engine and check all controls for proper
operation: ground speed control levers, parking brake
lever, throttle and choke cables, electric PTO clutch,
attachment lift, etc.
3. Stop the engine and check for fluid leaks: oil, gaso-
line, or transmission oil.
4. If any control fails to operate properly during testing or
seems to be out of adjustment, check and readjust it
according to the following Adjustments section.
4. Turn the key to OFF to end the demonstration.
Mower Blade Stopping Check
Mower blades and mower drive belt should come to a
complete stop within five seconds after the electric clutch
switch is turned off.
With the rider in neutral, the electric clutch switch dis-
engaged, and an operator in the seat, start the tractor
engine. Run the engine at full throttle. Engage the electric
PTO clutch switch and wait several seconds. Disengage
electric clutch switch and check the time it takes for the
mower drive belt to stop. If the mower drive belt does not
stop within five seconds, adjust the PTO clutch according
to the instructions in the Electric Clutch Adjustment sec-
tion.
Seat Switch Connection
Check that the seat switch wire harness (D, Figure 2) is
connected to the seat switch.
Burnish Electric PTO Clutch
1. Select a safe area to operate the mower deck. With
the drive in neutral, the PTO switch disengaged, and
an operator in the seat, start the tractor engine. Run
the engine at full throttle.
2. Engage the PTO switch and run the deck for fifteen
seconds. Disengage the PTO switch and wait for the
mower drive belt to stop.
3. Repeat step 2 above ten times, and then re-check the
mower blade stopping time. (Stopping time must be
five seconds or less.)
WARNING
Disengage the PTO, stop the engine, set the
parking brake, and wait for moving parts to stop
before leaving operator’s position for any reason.
If the unit does not pass the test, do not operate
it. Under no circumstance should you attempt to
defeat the purpose of the safety system.