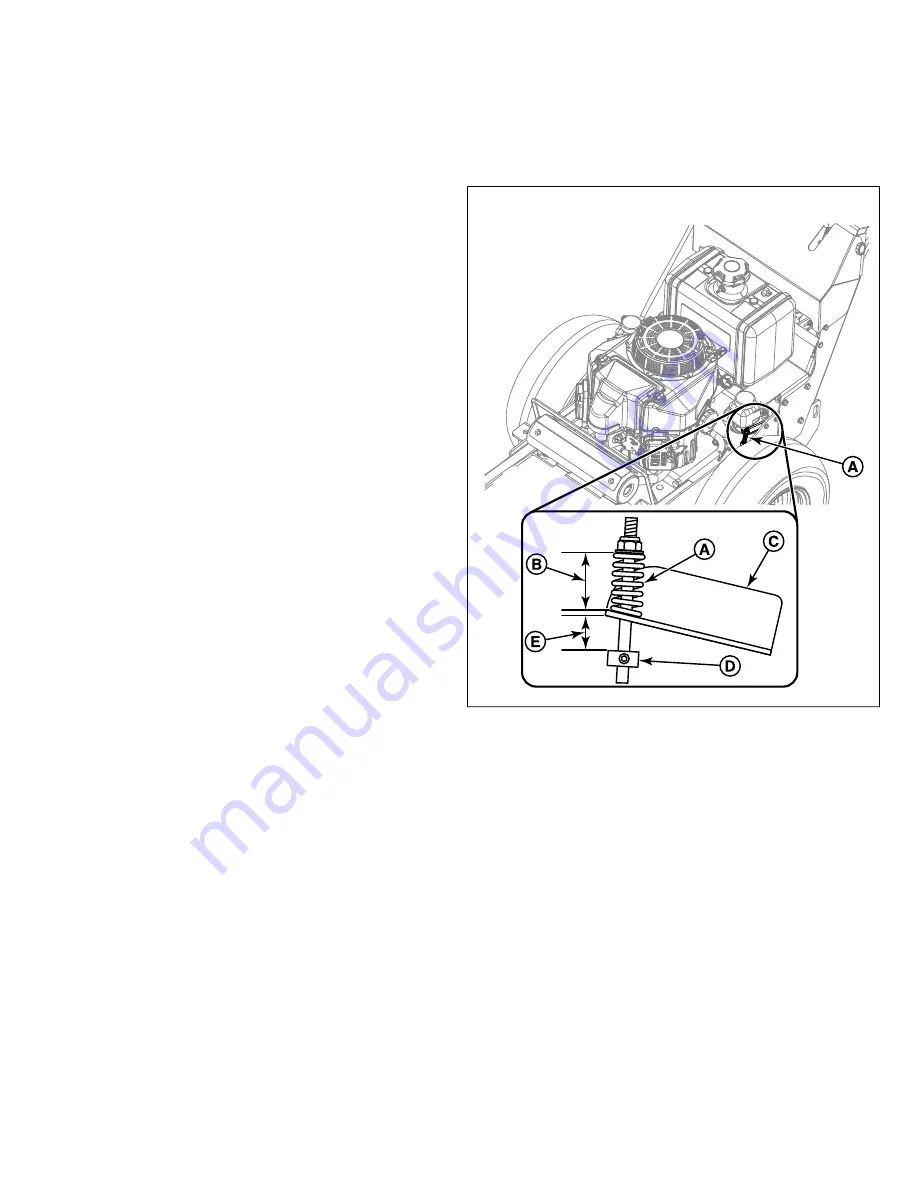
Not for
Reproduction
Purging the Air from the Hydraulic System
Due to the effects air has on efficiency in hydraulic drive
systems, it is critical that it be purged from the system.
These purge procedures should be implemented any time a
hydraulic system has been opened to facilitate maintenance or
any additional oil has been added to the system.
The resulting symptoms of air in the hydraulic system may be:
• Noisy operation.
• Lack of power or drive after short term operation.
• High operation temperature and excessive expansion of
oil.
Before starting, make sure the transaxles/transmissions are at
the proper oil levels. If it is not, fill to the specifications outlined
in the
Check / Fill Transmission Oil Level procedure.
Purging Air from the Hydraulic System:
1.
Chock the front wheels to prevent the machine from rolling.
Raise the rear of the machine so that the vehicle’s rear tires
do not contact the ground. Position jack stands under the
rear bumper of the machine to secure it.
2.
Open the transaxle’s bypass valves (see
Uncrating for the
location and function of the bypass valves), start the engine,
release the parking brake, and slowly move the zero-turn
rider’s ground speed control levers in both forward and
reverse directions (5 to 6 times), as air is purged from the
unit, the oil level will drop.
3.
Stop the engine and engage the parking brake.
4.
Close the transaxle’s bypass valves, start the engine,
release the parking brake, and slowly move the zero-turn
rider’s ground speed control levers in both forward and
reverse directions (5 to 6 times), as air is purged from the
unit, the oil level will drop.
5.
Stop the engine. Remove the jack stands from underneath
the machine.
6.
Repeat the process detailed above but with the unit's drive
wheels on the ground. The procedure should be performed
in an area free of any objects or bystanders.
It may be necessary to repeat the process detailed above until
all the air is completely purged from the system. When the
transaxles/transmissions operate at normal noise levels and
move smoothly forward and reverse at normal speeds, then the
transaxles/transmissions are considered purged.
Parking Brake Adjustment
The parking brake mechanism consists of a single parking brake
rod that connects the parking brake handle to the lower parking
brake shaft. The lower parking brake shaft connects two (2)
transaxle brake linkage rods to the transaxles. There is one
linkage rod per transaxle. On each linkage rod there is one
parking brake spring and a set collar. The parking brake is
adjusted by changing the compressed spring length of the
parking brake spring and the position of the set collar.
1.
Park the unit on a flat, level surface such as a concrete
floor. Disengage the PTO, engage the parking brake, turn
ignition switch to OFF, and remove the key.
2.
Locate the two (2) parking brake springs (A, Figure 26).
The parking brake springs are below the hydraulic oil
reservoir tanks on each side of the machine.
26
3.
With the parking brake engaged, measure the compressed
spring length (B) of the parking brake springs. The
measurement is taken on the front edge of the spring which
is the side that is most compressed with the parking brake
engaged. The parking brake springs should measure 1-1/8"
(2.86 cm) when compressed.
4.
Loosen the hardware (A, Figure 27) the retains the handle
bar guard (B) and tilt it forward. Loosen the two (2) jam nuts
(C) on either side of the neutral lock out plate (D) and turn
the adjustment bolt (E) until the measurement of 1-1/8”
(2.86 cm) is achieved on the compressed parking brake
springs. Tighten the jam nuts.
14