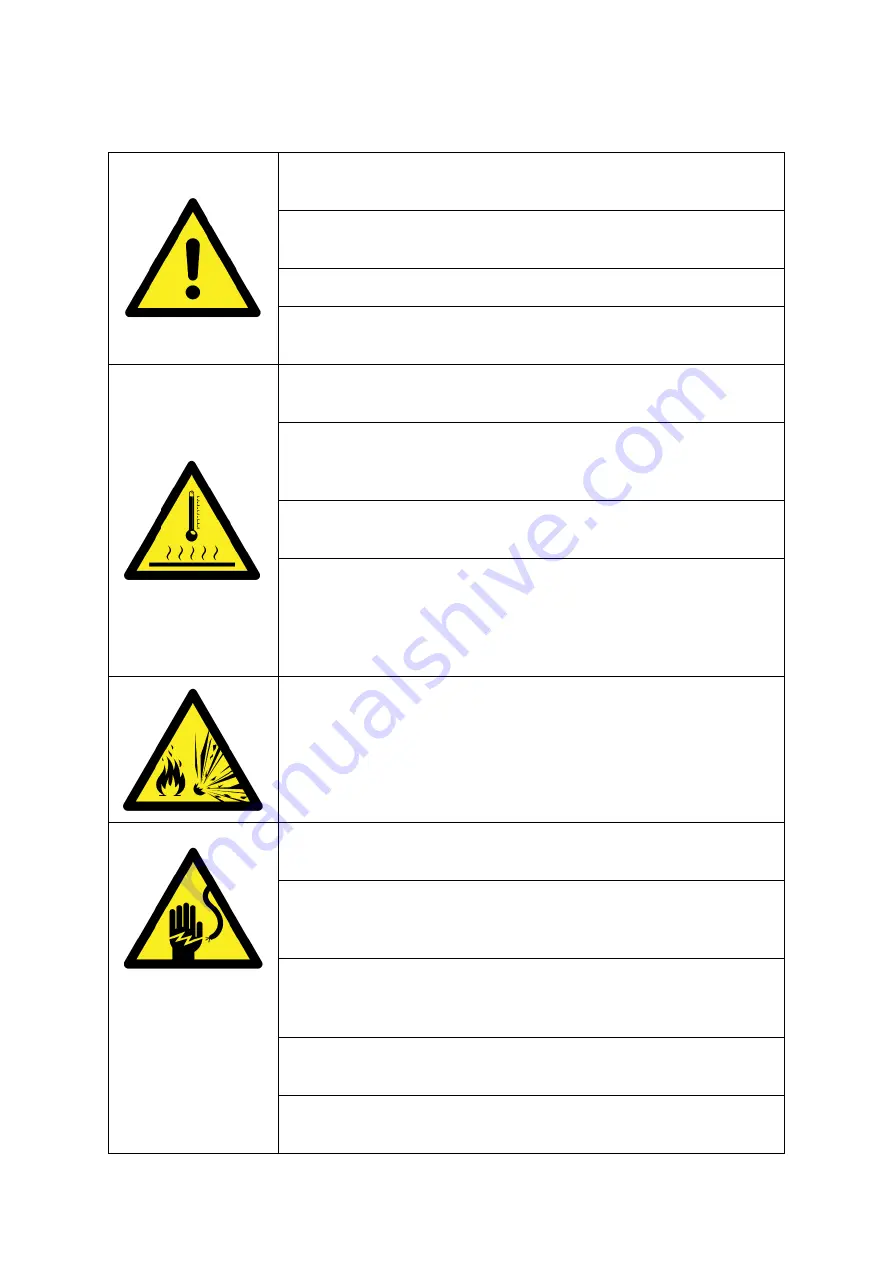
7712206-User Manual-EN-2019-9
3 | 22
Safety instructions
Keep children away from packaging materials. Plastic bags can cause
choking.
Make sure the power cable(s) are undamaged. Do not use the product if
the power cable(s) are damaged due to risk of fire and electric shock.
The product must be positioned on a flat and stable surface before use.
Connectors and clamps should be checked and tightened if necessary,
before each use to avoid leaks.
The surface of the product gets very hot. Do not touch hot steel parts
during use due to risk of scalding and burns.
Learn the function of the valves before you fill the tank with water. Use
blind caps on unused output ports due to risk of spillage of boiling/hot
liquid that may cause scalding and burns.
Do not fill the tank passed the maximum mark. During boiling, reduce
the power to avoid boil over. Risk of scalding and burns.
The product has a powerful pump. Before using the pump, make sure
valves are set to the correct position. The pump speed can be adjusted
on the touch screen. Too much flow through the pump, for example
during circulation over the grains can cause liquid to spray outside the
tank. Risk of scalding and burns.
The heating elements are designed to heat liquids and must not be
turned on without being completely submerged. Boiling liquids will
evaporate and reduce the volume in the tank over time. During
circulation the liquid around the malt pipe will be reduced. Make sure
there is always enough flow to keep the heating elements covered. The
product must not be used without supervision
Make sure the power cables are inserted correctly. There are grooves in
the connectors that needs to match the sockets.
During cleaning, the power supply must be disconnected. The machine
must not be sprayed down on the outside. The electrical control system
is protected from water splashes, but not spraying water.
The product is mostly constructed of highly conductive materials. Only
use the product on circuits with a residual circuit breaker due to risk of
electric shock in the event of an electric component failure.
The power cable(s) must be disconnected when the product is not in
use.
If you find a fault with the product that may pose a risk, stop using the
product and contact the manufacturer or the reseller.