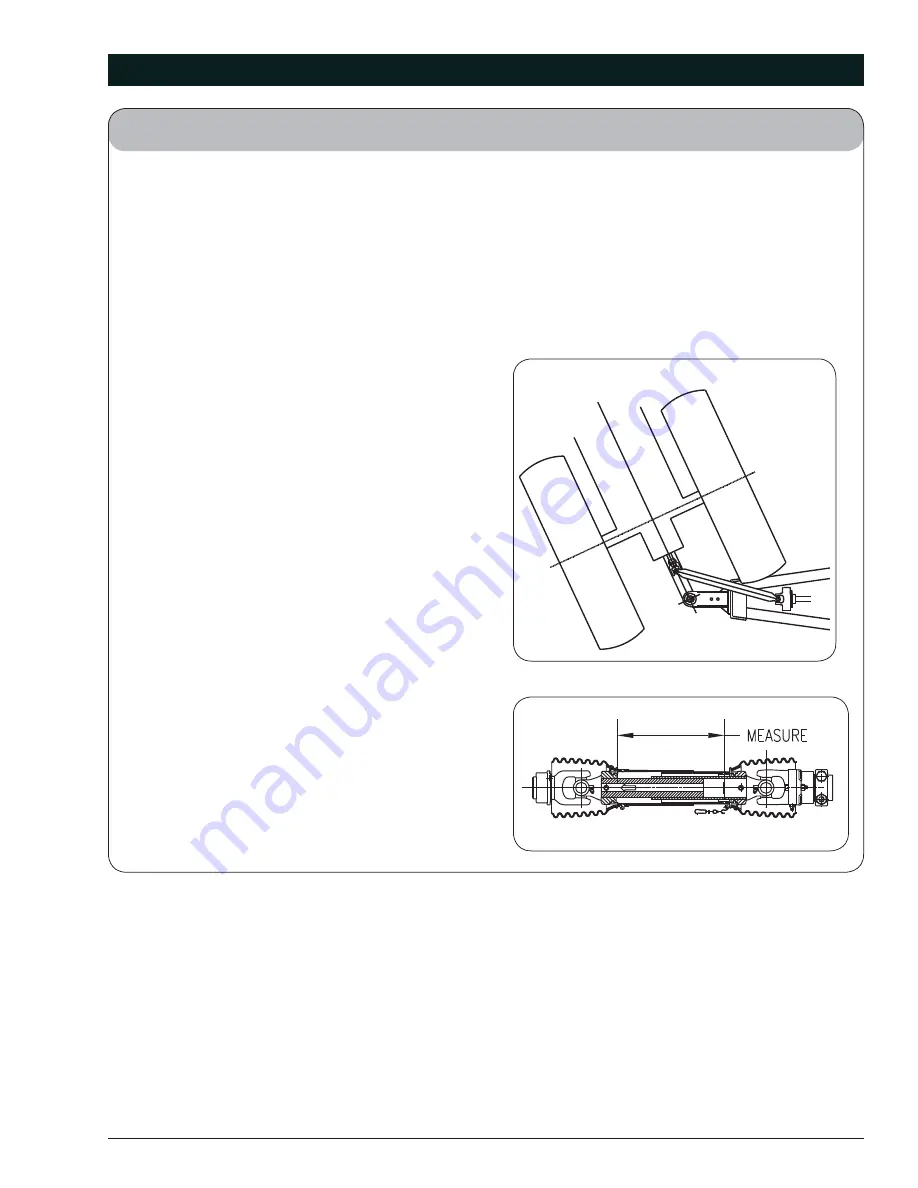
Brent 1082/882
— Maintenance
4-13
Verify Telescoping PTO Shaft Length
(continued)
4. Hitch tractor drawbar to cart, ensuring that tractor and cart are on level ground and coupled as
straight as practical.
5. Connect PTO shaft to tractor, and measure length “L” from same points as used in step 1.
Ensure
that this measurement does not exceed the maximum recommended extended length calculated
in step 3 above.
If necessary, choose a shorter drawbar position, or obtain a longer PTO shaft as-
sembly before operating cart.
6. Position the tractor to obtain tightest turning
angle, relative to the cart.
7. Measure length “L” from same points as used
in step 1. This distance must be at least 1.5
inches greater than the distance measured in
step 1. If necessary, adjust length of PTO shaft
by cutting inner and outer plastic guard tubes
and inner and outer sliding profi les by the same
length. Round off all sharp edges and remove
burrs before greasing and reassembling shaft
halves.
(July 2014)