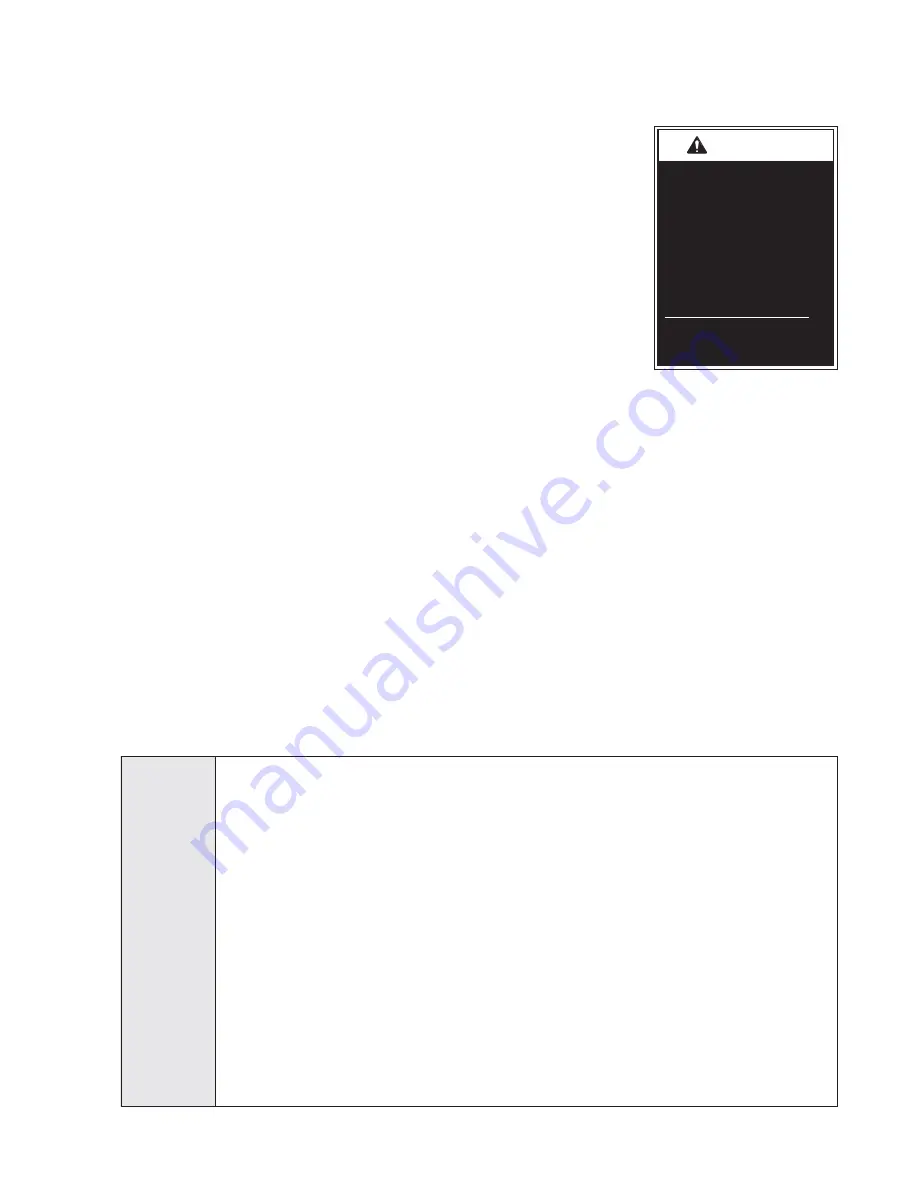
Page 13
Maintenance and Lubrication Schedule
Maintenance and
lubrication procedures
must be performed as
speci
fi
ed by an
authorized service
technician. Failure to
do so may result in
serious bodily injury
and/or property
damage.
Proper maintenance is necessary to ensure safe,
troublefree operation. Inspecting the lift for any wear,
damage or other abnormal conditions should be a part
of all transit agencies’s daily service program. Simple
inspections can detect potential problems.
The maintenance and lubrication procedures speci
fi
ed
in this schedule
must
be performed by a Braun autho-
rized service representative at the scheduled intervals
according to the number of cycles.
Braun dual parallel arm lifts are equipped with hard-
ened pins and self-lubricating bushings to decrease
wear, provide smooth operation and extend the service
life of the lift.
When servicing the lift at the recommended intervals,
inspection and lubrication procedures speci
fi
ed in
the previous sections should be repeated.
Clean
the
components and the surrounding area
before apply-
ing lubricants
. LPS2 General Purpose Penetrating
Oil is recommended where Light Oil is called out.
Use of improper lubricants can attract dirt or other
contaminants which could result in wear or damage
to the components. Platform components exposed to
contaminants when lowered to the ground may require
extra attention.
Lift components requiring grease are lubricated during
assembly procedures. When these components are
replaced, grease must be applied during installation
procedures. Speci
fi
ed lubricants are available from
The Braun Corporation (part numbers provided above).
All
listed inspection, lubrication and maintenance
procedures should be repeated at “750 cycle” intervals
following the scheduled
“4500 Cycles” mainte-
nance. These intervals
are a general guideline
for scheduling mainte-
nance procedures and
will vary according to
lift use and conditions.
Lifts exposed to severe
conditions (weather, envi-
ronment, contamination,
heavy usage, etc.) may
require inspection and
maintenance procedures
to be performed more
often than speci
fi
ed.
Maintenance Indicator:
The Lift Ready green LED
mounted on top of the pump cover will begin to blink
after every 750 cycles. The blinking LED will not affect
the functions of the lift, but is a reminder to complete
necessary maintenance and lubrication.
Once the lift has been serviced, fully stow the lift. Once
stowed, press the UP button on the hand pendant and
the Floor Level Set button on the back side of the pump
cover until the Lift Ready green LED stops blinking.
Discontinue lift use immediately
if maintenance and
lubrication procedures are not properly performed, or if
there is any sign of wear, damage or improper opera-
tion. Contact your sales representative or call The
Braun Corporation at 1-800-THE LIFT
®
. One of our
national Product Support representatives will direct you
to an authorized service technician who will inspect your
lift.
Outer barrier pivot bearings (2)
Outer barrier latch bearings (4)
Outer barrier link arm pivot points (2)
Lift-Tite
™
latches (tower pivot points - 2)
Lift-Tite
™
latch gas (dampening) spring pivot
points (2 springs - 4 points)
Inspect Lift-Tite
™
latches and gas springs (dampen-
ing) for wear or damage (bent, deformed or mis-
aligned), positive securement (external snap rings)
and proper operation
Inspect outer barrier for proper operation
Inspect outer barrier latch for proper operation,
positive securement, and detached or missing
spring
Apply Light Oil - See Lubrication Diagram
Apply Light Oil - See Lubrication Diagram
Apply Light Oil - See Lubrication Diagram
Apply Light Oil - See Lubrication Diagram
Apply Light Oil - See Lubrication Diagram
Resecure, replace damaged parts or otherwise
correct as needed.
Note:
Apply Light Grease to
Lift-Tite
™
latch tower pivot point if replacing latch.
Correct or replace damaged parts.
Correct or replace damaged parts and/or relubri-
cate. See Lubrication Diagram
750
Cycles
WARNING